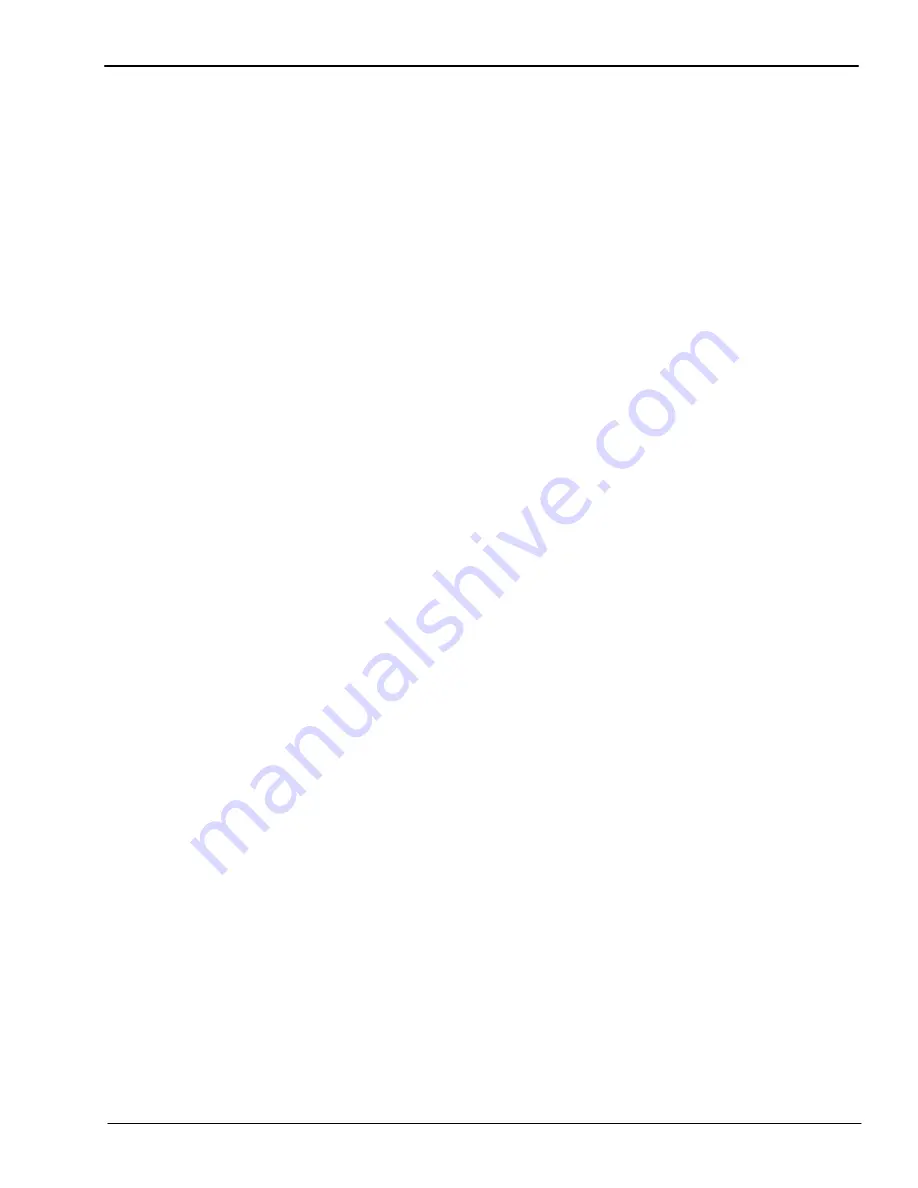
CWS
−
D100
−
B Welding System
Optional Equipment
2005 Swagelok Company, all rights reserved
September 2005
B-5
When selecting data recording equipment, consider the
accuracy of the printout required. The frequency response of
a recorder determines its ability to respond to a signal
change, which determines printout accuracy.
To record accurate data during the welding process, it is
suggested that the data collecting device have a sampling
rate ten times faster than the maximum weld impulse rate. If
the sampling rate is not sufficient, the data is not recorded
accurately. The SWS maximum pulse frequency is 99 pulses
per second. This pulse rate suggests a minimum sample rate
of 1000 samples per second. In addition to the sampling
rate, the equipment must also have the capability to gather
data over the longest programmed weld time, 198 seconds.
When an analog strip chart recorder is used, the 0 V (dc) to
5 V (dc) signals drive the strip chart pens. This type of
recorder generally has limited memory and does not store
data for future retrieval.
When the data must be captured and stored for future
reference, digital recording equipment is used. This
equipment converts the analog signals to data patterns that
are stored to some device, such as a memory unit or a hard
disk. The data can be recalled as needed and can be used for
later analysis of the welding process.
Remember that data recording is just a method used to
monitor the welding process and does not guarantee the
quality of the weld.