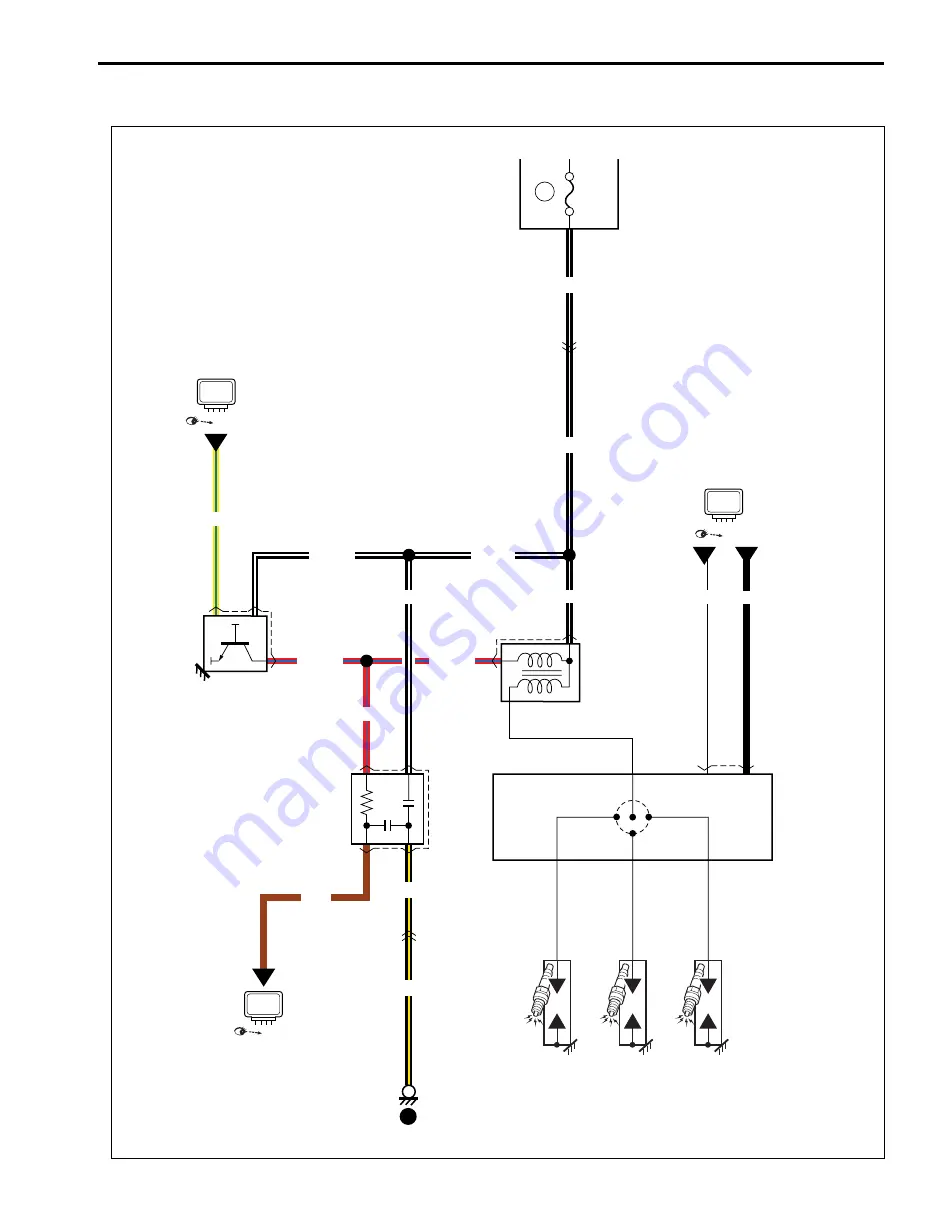
8A-6-5
A-4 Ignition system (G10)
A-4 Z
ü
ndanlage (G10)
A-4 Syst
è
me d
’
allumage (G10)
A-4 Ontstekingssysteem (G10)
15A
IG
COIL
BLK/WHT
G41
E47
E59
E60
13
1
D23
1
2
1
3
2
4
BLK/WHT
BLK/WHT
YEL/BLU
BRN
E58
4
2
3
1
BLK/YEL
BLK/YEL
E40
D02
2
BLK/WHT
BLK/WHT
RED/BLU
RED/BLU
RED/BLU
WHT
BLK
Noise suppressor
Igniter
Distributor
IG COIL
P/S
Cont M
"F-3"
W
B
"A-5"
Br
16
6
YB
"A-5"
ECM
ECM
BLK/WHT
Individual
circuit fuse box
Summary of Contents for WagonR+ RB310
Page 6: ...Foreword...
Page 8: ...Vorwort...
Page 10: ...Avant propos...
Page 12: ...Voorwoord...
Page 66: ...8A 3 30 Memo Notizen Note Memo...
Page 83: ...8A 6 7 Memo Notizen Note Memo...
Page 103: ...8A 6 27 Memo Notizen Note Memo...
Page 111: ...8A 6 35 Memo Notizen Note Memo...
Page 115: ...8A 6 39 Memo Notizen Note Memo...
Page 119: ...8A 6 43 Memo Notizen Note Memo...
Page 154: ...8A 8 4 Memo Notizen Note Memo...
Page 155: ...Prepared by 1st Ed January 2004 146F...
Page 266: ...GROUND POINT MASSEPUNKT POINTS DE MASSE AARDEPUNT 8A 5 4 FLOOR BODEN PLANCHER VLOER...
Page 267: ...GROUND POINT MASSEPUNKT POINTS DE MASSE AARDEPUNT 8A 5 5 REAR T R PORTE ACHTERKANT...
Page 349: ......
Page 351: ......
Page 409: ...0B 30 MAINTENANCE AND LUBRICATION...
Page 423: ...1A 14 HEATER AND VENTILATION...
Page 475: ...3D 16 FRONT SUSPENSION...
Page 525: ...4A 20 FRONT DRIVE SHAFT G10 M13 ENGINE MODELS...
Page 549: ...5 6 BRAKES...
Page 559: ...5B 6 FRONT BRAKE...
Page 814: ...ENGINE MECHANICAL M13 ENGINE 6A2 79 Main Bearings Crankshaft and Cylinder Block Components...
Page 831: ...6A2 96 ENGINE MECHANICAL M13 ENGINE...
Page 915: ...6H 4 CHARGING SYSTEM G10 M13 ENGINES...
Page 935: ...7A2 16 MANUAL TRANSAXLE M13 ENGINE MODEL Transaxle Case Components...
Page 949: ...7A2 30 MANUAL TRANSAXLE M13 ENGINE MODEL Input Counter Shaft Components...
Page 972: ...AUTOMATIC TRANSAXLE M13 ENGINE MODEL 7B1 7 Table of Component Operation...
Page 1086: ...AUTOMATIC TRANSAXLE M13 ENGINE MODEL 7B1 121...
Page 1185: ...7C 14 CLUTCH G10 M13 ENGINE MODELS...
Page 1193: ...7D 8 TRANSFER...
Page 1217: ...8B 4 LIGHTING SYSTEM...
Page 1223: ...8C 6 INSTRUMENTATION DRIVER INFORMATION...
Page 1235: ...8G 12 IMMOBILIZER CONTROL SYSTEM G10 M13 ENGINE MODELS...
Page 1251: ...8G3 16 IMMOBILIZER CONTROL SYSTEM Z13DT ENGINE MODEL...
Page 1257: ...9 6 BODY SERVICE...
Page 1258: ...Prepared by 1st Ed August 2003 Printed in Belgium Printed January 2004 910...
Page 1261: ......
Page 1263: ......
Page 1291: ...5C 14 PARKING AND REAR BRAKE...
Page 1295: ...5E 4 ANTILOCK BRAKE SYSTEM ABS System Schematic...
Page 1297: ...5E 6 ANTILOCK BRAKE SYSTEM ABS System Circuit...
Page 1319: ...5E 28 ANTILOCK BRAKE SYSTEM ABS...
Page 1325: ...8D 4 WINDOWS MIRRORS SECURITY AND LOCKS...
Page 1337: ...10A 4 SEAT BELT...
Page 1338: ...Prepared by Service Department 1st Ed June 2002 Printed in Hungary Printing August 2002 80...
Page 1341: ......
Page 1343: ......
Page 1353: ...0B 4 MAINTENANCE AND LUBRICATION...
Page 1355: ...3B1 2 ELECTRICAL POWER STEERING EPS SYSTEM IF EQUIPPED...
Page 1361: ...5E 6 ANTILOCK BRAKE SYSTEM ABS System Circuit...
Page 1397: ...5E 42 ANTILOCK BRAKE SYSTEM ABS...
Page 1399: ...6 2 ENGINE...
Page 1401: ...6E 2 ENGINE AND EMISSION CONTROL SYSTEM...
Page 1411: ...6F1 10 IGNITION SYSTEM ELECTRONIC IGNITION SYSTEM...
Page 1471: ...7B 60 AUTOMATIC TRANSMISSION 4 A T...
Page 1591: ...Prepared by Service Department 1st Ed November 2001 Printed in Hungary 252...
Page 1592: ...Prepared by Service Department 1st Ed November 2001 Printed in Hungary 252...
Page 1595: ......
Page 1597: ......
Page 1641: ...5C 4 PARKING AND REAR BRAKE...
Page 1645: ...5E1 4 ANTILOCK BRAKE SYSTEM ABS System Circuit...
Page 1653: ...5E1 12 ANTILOCK BRAKE SYSTEM ABS...
Page 1668: ...MANUAL TRANSMISSION 7A 9...
Page 1670: ...MANUAL TRANSMISSION 7A 11...
Page 1687: ...7C 6 CLUTCH...
Page 1737: ...Prepared by Service Department 1st Ed June 2001 Printing August 2001 144...
Page 1959: ...6E1 6 ENGINE AND EMISSION CONTROL SYSTEM IG COIL MAIN FUSE...
Page 2020: ...Prepared by Service Department 1st Ed March 2001 Printed in Belgium Printing March 2001 288...
Page 2023: ......
Page 2025: ......
Page 2069: ......
Page 2111: ......
Page 2123: ......
Page 2173: ......
Page 2241: ......
Page 2255: ......
Page 2273: ......
Page 2321: ......
Page 2327: ...5E1 6 ANTILOCK BRAKE SYSTEM ABS SYSTEM CIRCUIT...
Page 2328: ...ANTILOCK BRAKE SYSTEM ABS 5E1 7...
Page 2359: ......
Page 2412: ...ENGINE DIAGNOSIS 6 53 MEMO...
Page 2434: ...E21 12 ENGINE DIAGNOSIS 6 75 Fig 1 for Step 2 Fig 2 for Step 2...
Page 2466: ...ENGINE DIAGNOSIS 6 107 Fig 1 for Step 1 4 Fuel pressure gauge 3way joint...
Page 2475: ......
Page 2557: ......
Page 2571: ......
Page 2587: ...6C 16 ENGINE FUEL 09919 47020 Quick joint remover SPECIAL TOOL...
Page 2590: ...ENGINE AND EMISSION CONTROL SYSTEM 6E 3...
Page 2591: ...6E 4 ENGINE AND EMISSION CONTROL SYSTEM...
Page 2592: ...ENGINE AND EMISSION CONTROL SYSTEM 6E 5...
Page 2597: ...6E 10 ENGINE AND EMISSION CONTROL SYSTEM...
Page 2598: ...ENGINE AND EMISSION CONTROL SYSTEM 6E 11...
Page 2637: ......
Page 2655: ......
Page 2669: ......
Page 2731: ......
Page 2861: ......
Page 2881: ...8 6 BODY ELECTRICAL SYSTEM POWER SUPPLY DIAGRAM Refer to Wiring Diagram Manual...
Page 2901: ......
Page 2935: ...09913 60910 Bearing puller 8D 24 WINDOWS MIRRORS SECURITY AND LOCKS SPECIAL TOOL...
Page 3083: ......
Page 3084: ......
Page 3085: ......
Page 3086: ...Prepared by Overseas Service Department 1st Ed December 1999 Printing January 2000 1064...