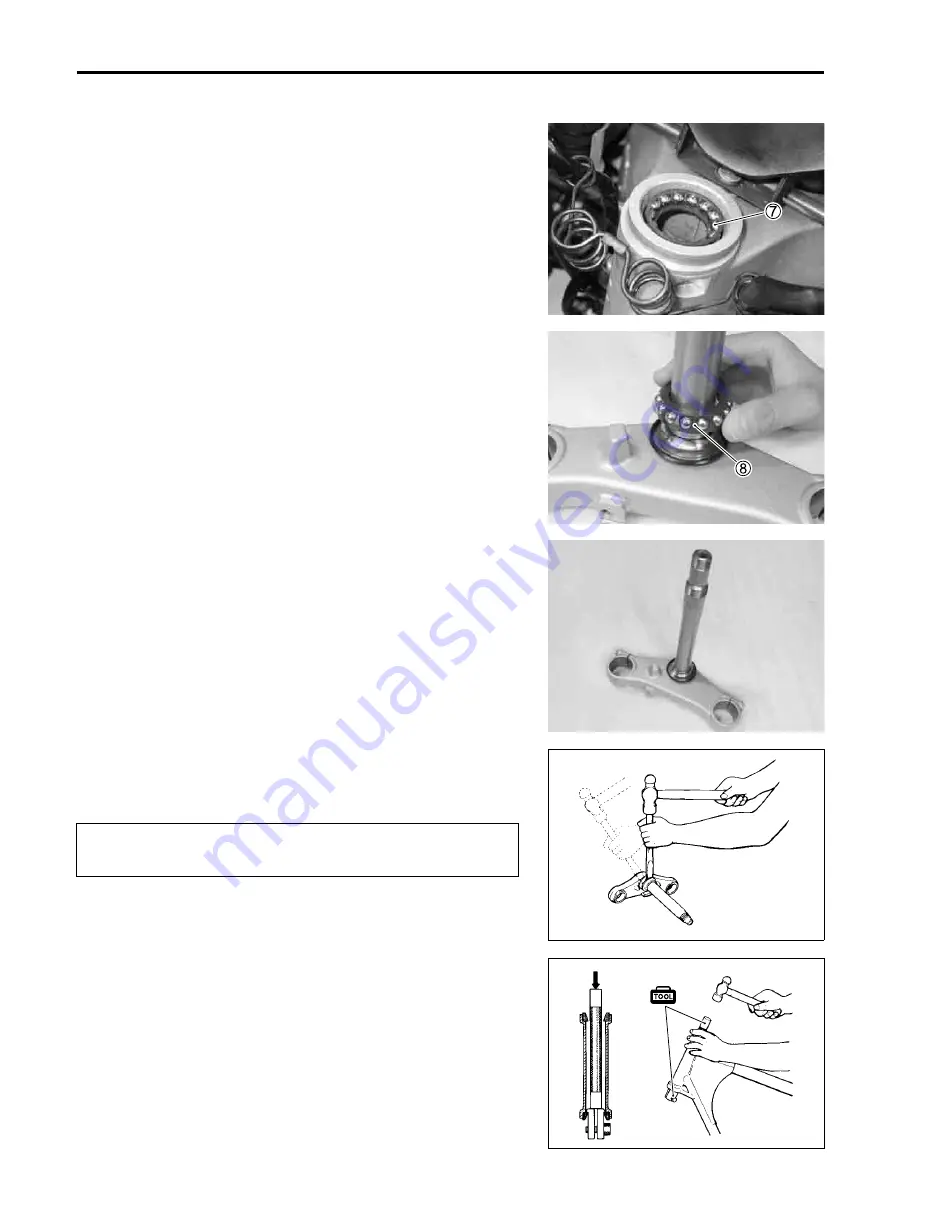
7-30 CHASSIS
• Remove the steering stem upper bearing
7
.
• Remove the steering stem lower bearing
8
.
INSPECTION AND DISASSEMBLY
Inspect the removed parts for the following abnormalities.
* Distortion of the steering stem
* Bearing wear or damage
* Abnormal bearing noise
* Handlebars distriction
* Race wear and brinelling
If any abnormal points are found, replace defective parts with
the new ones.
• Remove the steering stem lower bearing inner race using a
chisel.
#
• Drive out the steering stem upper and lower bearing races
with the special tools.
$
09941-54911: Bearing outer race remover
09925-18011: Steering bearing installer
The removed bearing inner race and dust seal must be
replaced with the new ones.
PartShark.com
877-999-5686
Summary of Contents for 2005 DL650K5
Page 22: ...P a r t S h a r k c o m 8 7 7 9 9 9 5 6 8 6...
Page 51: ...PERIODIC MAINTENANCE 2 29 P a r t S h a r k c o m 8 7 7 9 9 9 5 6 8 6...
Page 54: ...P a r t S h a r k c o m 8 7 7 9 9 9 5 6 8 6...
Page 249: ...P a r t S h a r k c o m 8 7 7 9 9 9 5 6 8 6...
Page 275: ...COOLING AND LUBRICATION SYSTEM 6 25 REAR CYLINDER P a r t S h a r k c o m 8 7 7 9 9 9 5 6 8 6...
Page 460: ...P a r t S h a r k c o m 8 7 7 9 9 9 5 6 8 6...
Page 472: ...P a r t S h a r k c o m 8 7 7 9 9 9 5 6 8 6...