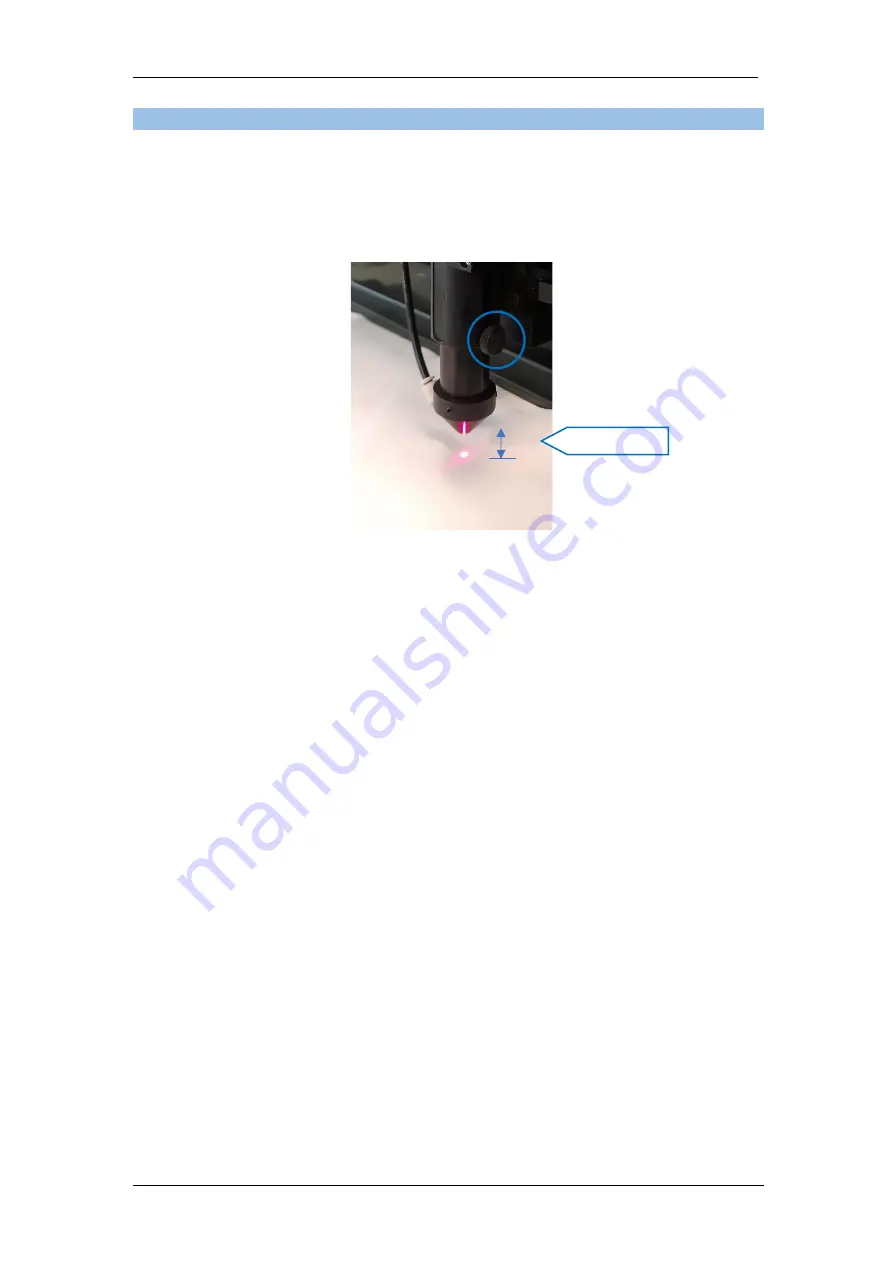
L3214 Laser Cutter
User’s Manual
Maintenance
44
4.1.2.2
Setting the nozzle height
To have a clean cut a good focus of the laser beam is required. Depending on the nozzle, the
thickness and the type of the material that is processed, height may vary.
1.
Loosen the thumb screw to adjust the height.
2. Place the focusing gauge between the nozzle and the material. When using a high-pressure
nozzle, set the focus distance at 4mm from the surface of the media to be cut. When using
a standard nozzle, the focus distance should be set at 14mm. Fix the thumb screw when
the correct height is set.
4mm or 14mm