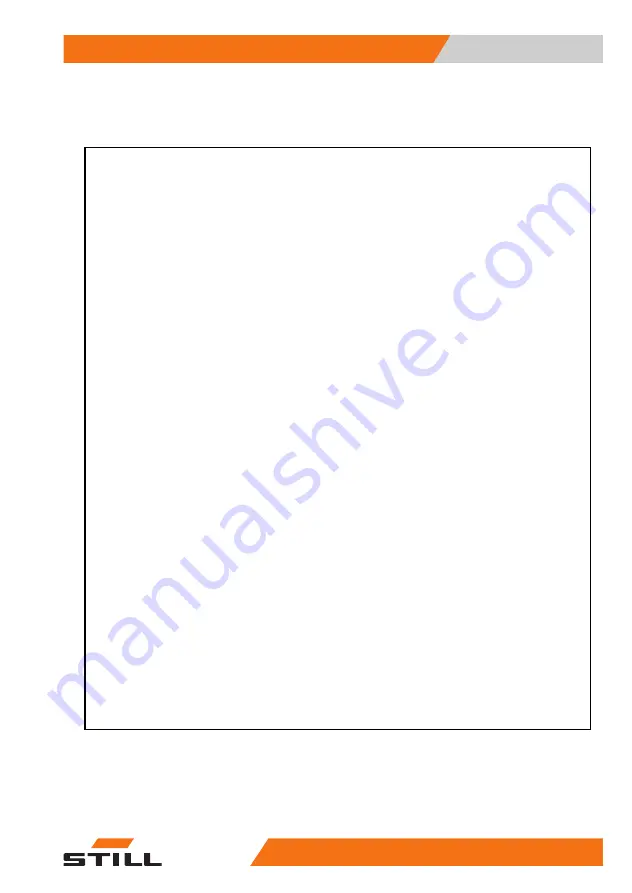
Foreword
1
EC declaration of conformity in accordance with Machinery Directive
EC declaration of conformity in accordance with Machinery Di-
rective
Declaration
STILL GmbH
Berzeliusstraße 10
D-22113 Hamburg Germany
We declare that the
Industrial truck
according to these operating instructions
Model
according to these operating instructions
conforms to the latest version of the Machinery Directive 2006/42/EC.
Personnel authorised to compile the technical documents:
See EC compliance declaration
STILL GmbH
.
Safety information
Explanations of the terms used in these
instructions:
51328042507 [EN]
3
Summary of Contents for FS-X33
Page 1: ...Original instructions FS X33 Seated pallet truck FS X 33 1301 51328042507 EN 07 2012 ...
Page 2: ......
Page 6: ......
Page 7: ...1 Foreword ...
Page 13: ...2 Safety ...
Page 28: ...2 Safety Basic principles for safe operation 22 51328042507 EN ...
Page 29: ...3 Overview ...
Page 38: ...3 Overview Safety equipment 32 51328042507 EN ...
Page 39: ...4 Operation ...
Page 67: ...5 Maintenance ...
Page 76: ...5 Maintenance Battery maintenance 70 51328042507 EN ...
Page 77: ...6 Technical data ...
Page 81: ...7 Special equipment ...
Page 88: ...7 Special equipment Cold store cab 82 51328042507 EN ...
Page 93: ......
Page 94: ...STILL GmbH Berzeliusstrasse 10 D 22113 Hamburg Ident no 51328042507 EN ...