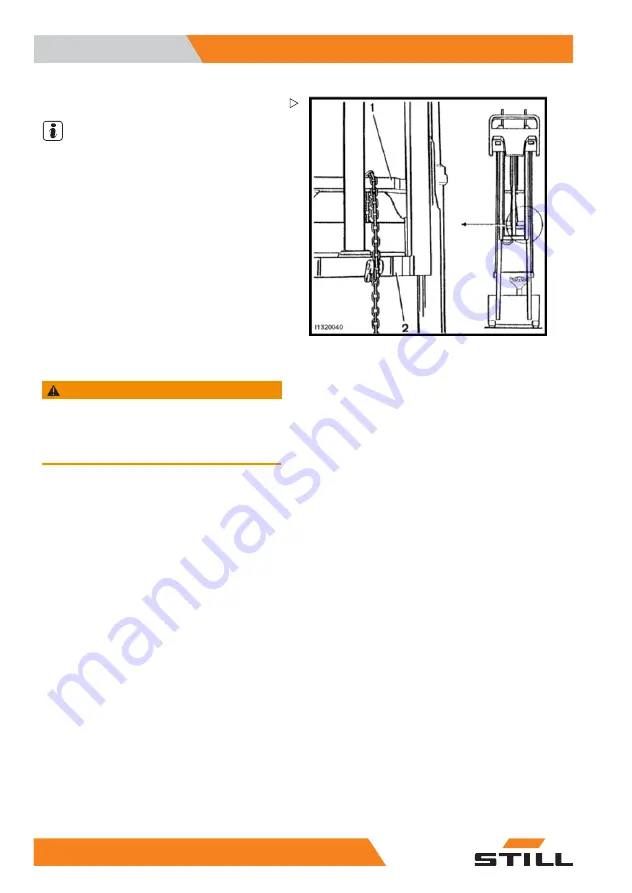
5
Maintenance
Preparation for maintenance
Dual lifting mast
NOTE
The advantage of this mast is that it can be
used in areas with low ceilings such as cellars,
lorries, boat hulls etc., allowing maximum use
of its free lifting ability.
OPERATION
The fork carriage is raised until free lifting
through the return pulley of the centre cylinder
chain. It moves at twice the speed of the
cylinder. Then the inner strut is lifted by the
two side cylinders and brings the fork carriage
with it. The centre cylinder is mounted on the
inner mobile strut.
Safety device for the Duplex lift mast
WARNING
Risk of serious injury and/or serious damage to
equipment.
Choose a chain whose strength is far greater than
the weight of the mast.
– Lift the mast.
– Connect the chain after passing it over the
cross member of the fixed strut (1) and the
cross member of the inner strut (2).
– Lower the inner strut until the safety chain is
under tension.
– Lower the fork carrying carriage to the
bottom of its travel.
90
1170 801 15 09 [EN]
Summary of Contents for EXG-10
Page 2: ......
Page 7: ...1 Introduction ...
Page 20: ...1 Introduction Environmental considerations 14 1170 801 15 09 EN ...
Page 21: ...2 Safety ...
Page 31: ...3 Overviews ...
Page 39: ...4 Use ...
Page 82: ...4 Use Putting Out of Commission and Storage 76 1170 801 15 09 EN ...
Page 83: ...5 Maintenance ...
Page 123: ...6 Technical data ...
Page 135: ......
Page 136: ...STILL GmbH Berzeliusstrasse 10 D 22113 Hamburg Ident no 1170 801 15 09 EN ...
Page 138: ......
Page 139: ...7 Diagrams ...
Page 146: ...7 Diagrams Electrical installation 140 1170 801 15 09 EN ...
Page 148: ...7 Diagrams Electrical installation 142 1170 801 15 09 EN ...
Page 150: ...7 Diagrams Electrical installation 144 1170 801 15 09 EN ...
Page 151: ...Diagrams 7 Electrical installation Mast tilt option EXG10 EXG12 EXG16 1170 801 15 09 EN 145 ...
Page 152: ...STILL GmbH Berzeliusstrasse 10 D 22113 Hamburg Ident no 1170 801 15 09 EN ...