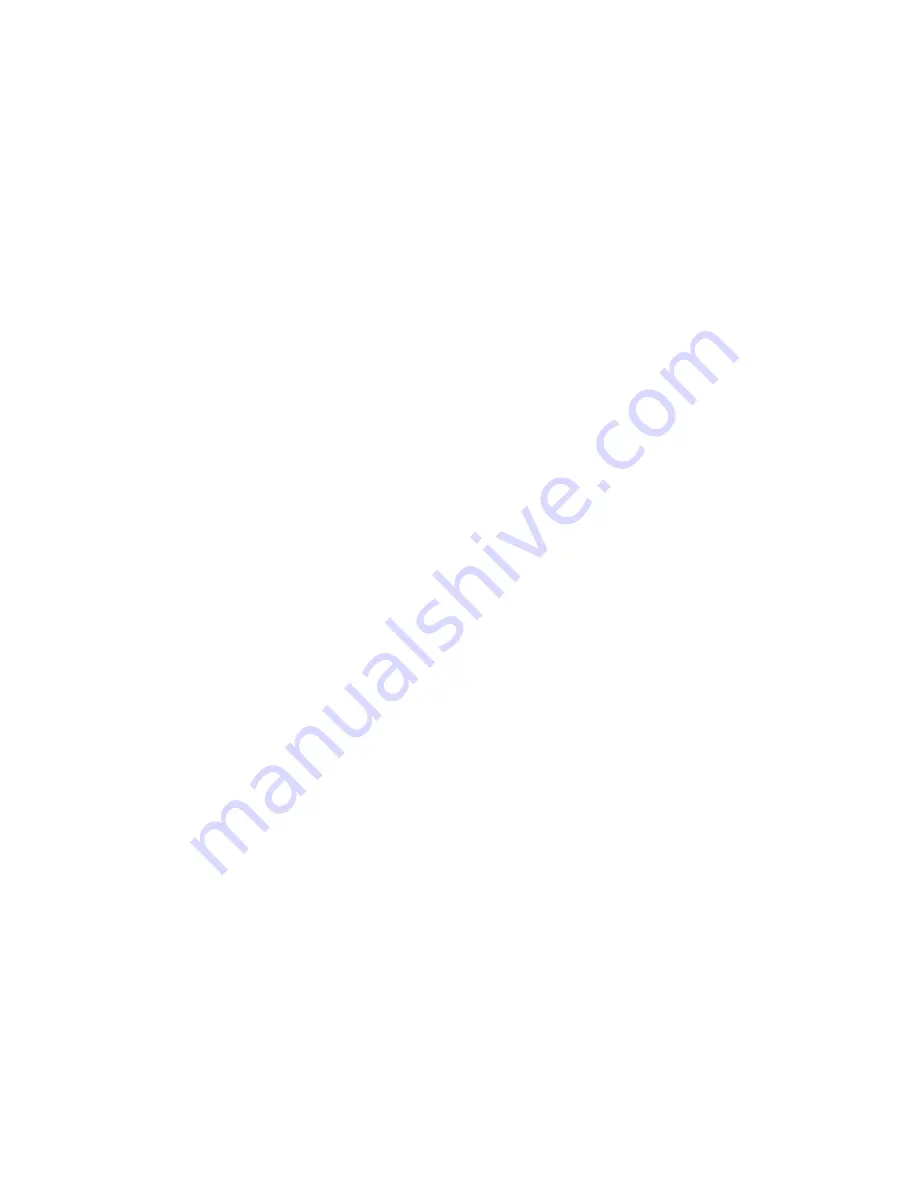
49
The Feed Pump and Clark Pump
The feed pump and the Clark Pump require no routine maintenance except inspection for
leaks. Tighten any hose clamps or fittings that show signs of leakage. The high pressure fittings
threaded into the Clark Pump have O-ring seals with a straight thread. These should never leak
and should never be over-tightened. If one of the tube nuts starts to leak, it can be un-
threaded, sealed with a bit of silicone grease or oil, and tightened with two wrenches very
tightly. See instructions on page 23.
The Membrane
Always perform a flow test (page 60) before cleaning your membrane. Cleaning is hard on
membranes, so only clean a membrane if you have ruled out other possibilities for low pro-
duction or poor water quality. The leading cause of fouling is biological growth that forms
when the system is left unused without flushing or pickling. Fouling from mineral scaling can
happen under certain seawater conditions, or from rust. Monitor the product salinity and feed
pressure for higher than normal readings, take environmental conditions into consideration:
Cold feed water can cause high pressure.
Low product flow is usually due to low voltage, a worn feed pump, or worn Clark Pump.
Test to see if biological growth has occurred: Before running the system, remove the prefil-
ter and examine its condition. If the filter housings are full of smelly, discolored water, the sys-
tem was not properly stored. Install a clean pre-filter.
Next check the membrane. Detach the brine discharge hose, attach the brine service hose, and
lead it to a bucket. Open the pressure relief valve 1/2 turn, and manually run the system for 30
seconds (metal toggle switch on feed pump module). Examine the brine water: If it is discol-
ored and smells bad, perform an SC-2 cleaning with unchlorinated water before running the
system pressurized. If the brine is fairly clean, follow the New System Startup procedure on
page 41 and run normally. Check for performance. Clean the membranes only if performance
is reduced.
See the Cleaning Procedure on page 56 for complete instructions.
Maintenance continued...
Summary of Contents for Catalina 340 Z
Page 2: ...2 ...
Page 4: ...4 ...
Page 6: ...6 ...
Page 8: ...8 ...
Page 10: ...10 ...
Page 11: ...11 Installation ...
Page 12: ...12 ...
Page 22: ...22 John Guest Super Speedfit Fittings ...
Page 34: ...34 ...
Page 35: ...35 Operation ...
Page 36: ...36 ...
Page 44: ...44 ...
Page 45: ...45 Maintenance Storage and Troubleshooting ...
Page 46: ...46 ...
Page 64: ...64 ...
Page 65: ...65 MPC 5000 Programming and Controls ...
Page 66: ...66 ...
Page 76: ...76 ...
Page 78: ...78 ...
Page 79: ...79 Exploded Views and Part Numbers ...
Page 80: ...80 ...
Page 88: ...88 Parts ...
Page 89: ...89 Parts PL MTS 3 8X1 2B HP CYL SST HP CYL CCA SO HPP ECCB HP CYL EC HP CYL R HP CYL PT Parts ...
Page 90: ...90 ...