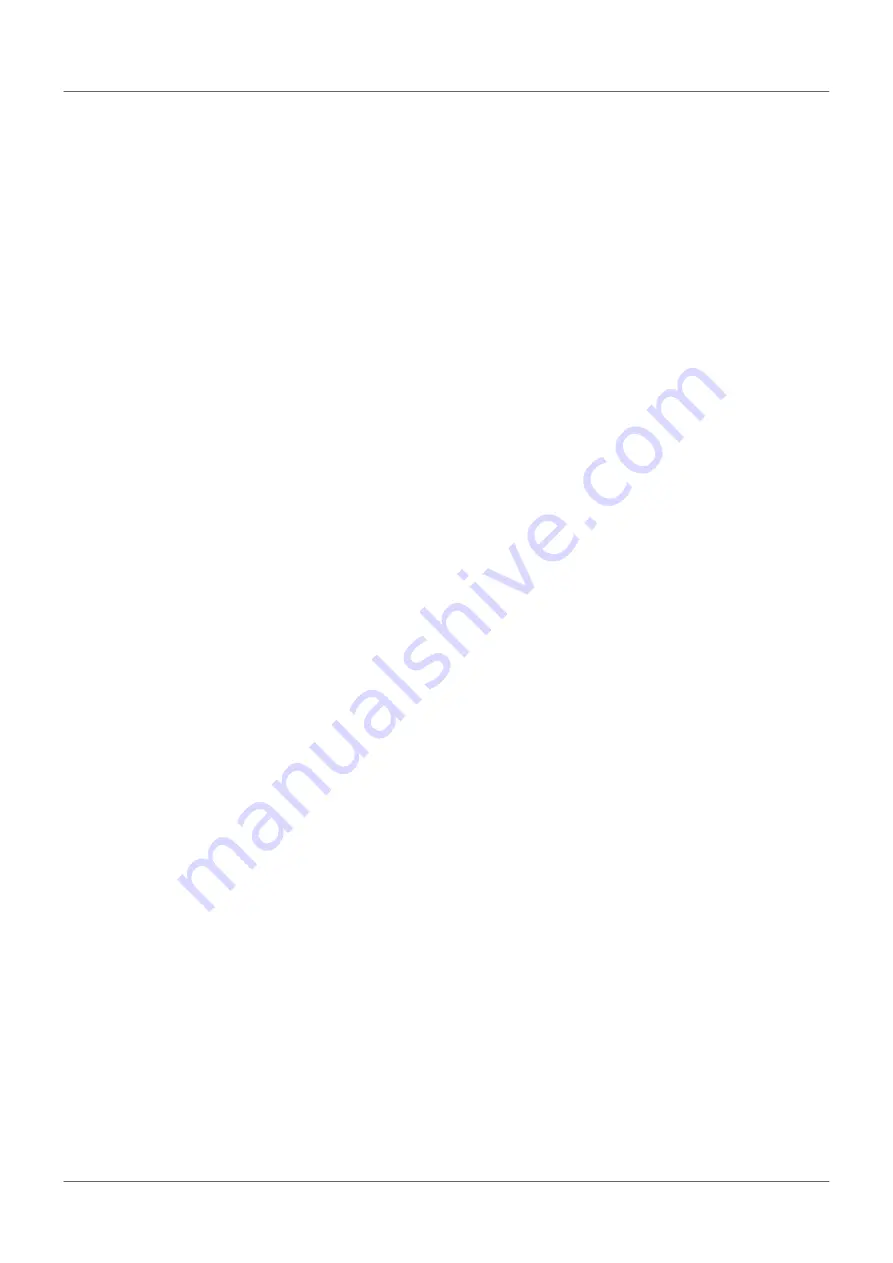
Chapter 9 - Appendix
Version EN-112021-1.30.3
63
Output function blocks detect the absence of fresh PLC output data. If the PLC does not provide fresh
output data then output function blocks will switch into a fault state mode. As the PLC write accesses to
the FG-200 Modbus registers are not synchronized with the cyclic data transfer in the H1 segment it is
necessary that the PLC writes "oversample" the H1 macrocycle. If, for example, the macrocycle time in the
H1 link is one second then it is assumed that the PLC writes fresh output data every 500 milliseconds.
9.1.5
Client/server connections (CTL/SRV connections)
Client/server connections are used for acyclic transfer between FG-200 and field devices. Acyclic data
transfer is performed in the gaps between cyclic data transfer.
For client/server connections the client (FG-200) establishes and server (H1 field device) is established.
Once the connection is established the FG-200 can send read and write requests to the field device. After
processing the request the field device sends a read or write response to the FG-200.
In case of client/server communication the FG-200 build internal read lists with all parameters configured
in the Modbus mapping table or in the point pages. The FG-200 executes this read lists periodically. The
time for executing the read lists depends on various factors. As a rule of thumb you can assume that a read
request and the corresponding read response will take about 100 millisecond. Thus, if you have, for
example, 25 parameters in your Modbus mapping and/or in your point pages each Modbus register and
point page parameter will be updated every two and a half second.
The main time consuming factors in read request handling are the low baud rate in an H1 segment (31.25
kbit/sec) and the processing time of the read request in the H1 field device. The processing time within the
FG-200 is negligible.
The FG-200 supports four H1 segments. If, enhancing the example above, 25 parameters are configured in
each segment the update time of the 4 * 25 parameters will still be two and a half second.
Please consider that the execution of the FG-200 read lists is not synchronized with the periodic execution
of the function blocks. Assuming the function blocks are executed one time per second and the execution
of the read list takes two and a half seconds then you will get only each second or third value produced by
the function block.
9.1.6
Macrocycle
Macrocycle is the period of the function block schedule and the cyclic data transfer schedule. Typical
macrocycle times are 500 milliseconds, one second, two seconds and four seconds.
9.1.7
Input/output parameters (I/O parameters)
Input and output parameters are used for accessing process values (input data and output data). They are
structured parameters composed of a status and a value.
IO parameters are typically transmitted via publisher/subscriber links. If no publisher/subscriber links are
configured IO parameter can be read and written via client/server connection.
9.1.8
Contained parameters
Contained parameters are used for data that are not process values. Contained parameters contain status
information and configuration data.
Contained parameters are read or written via client/server connections. It is not possible to transmit
contained parameters via publisher/subscriber links.
Summary of Contents for FG-200 HSE/FF
Page 1: ...Softing Industrial Automation GmbH FG 200 HSE FF Modbus User Manual Version EN 112021 1 30 3...
Page 49: ...Chapter 6 Using the web interface Version EN 112021 1 30 3 49...
Page 56: ...FG 200 HSE FF Modbus User Manual 56 Version EN 112021 1 30 3...
Page 77: ...Chapter 10 ATEX Type Examination Certificate Version EN 112021 1 30 3 77...
Page 78: ...FG 200 HSE FF Modbus User Manual 78 Version EN 112021 1 30 3...
Page 81: ...Chapter 12 Declarations of conformity Version EN 112021 1 30 3 81...