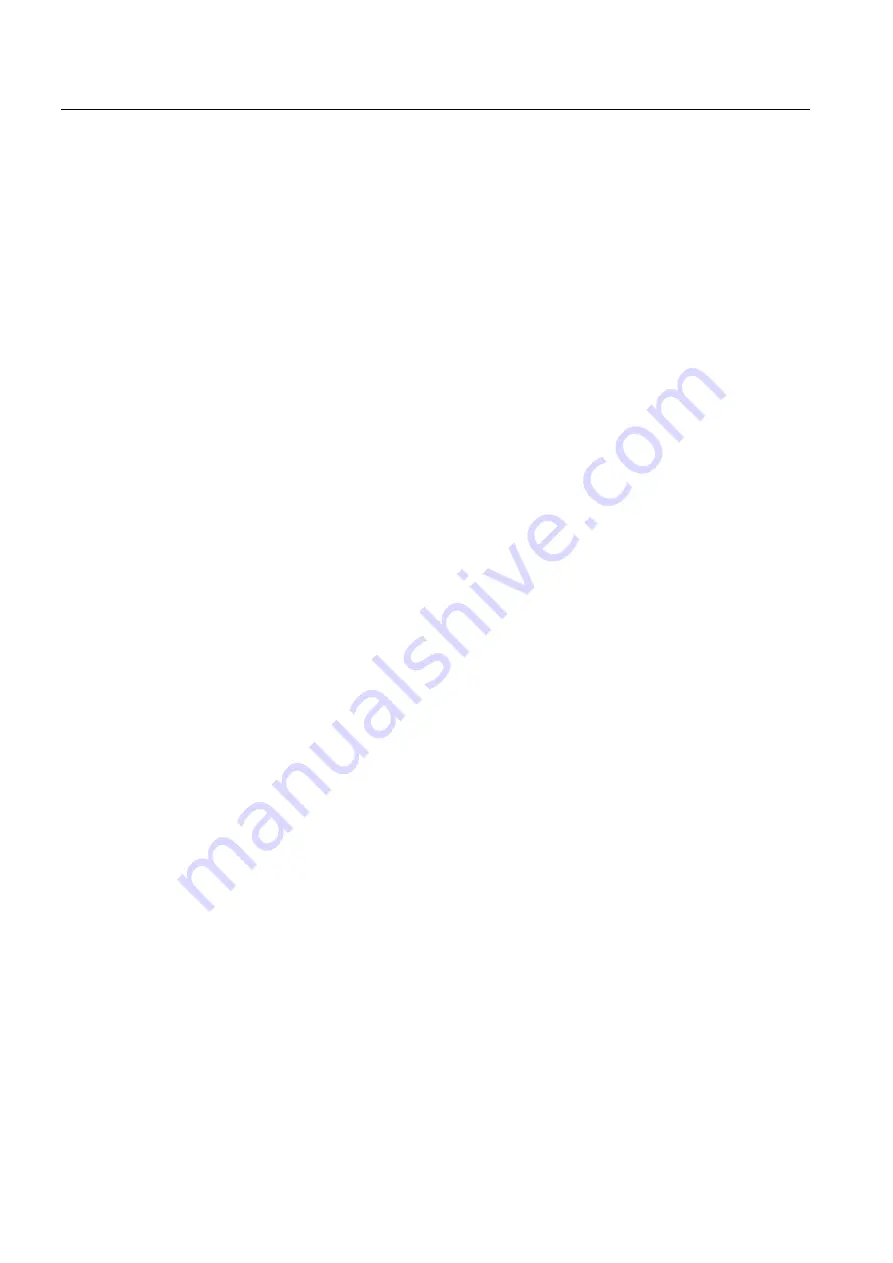
Cycles
9.9 Multiple plunge-cutting – CYCLE411
Cylindrical grinding
176
Programming and Operating Manual, 07/2009, 6FC5398-4CP10-2BA0
Function
If the width of the area to be machined is larger than the wheel width, several plunge-cut
operations are required. These are performed offset by one wheel width with an appropriate
overlap.
During the individual plunge-cuts, roughing is performed up to the finishing allowance.
An acoustic emission sensor can be used to bridge the distance between the starting point
and the actual workpiece surface within an optimum time by sparking.
To obtain a proper surface on the workpiece, the workpiece is subsequently ground up to its
finished dimension using the reciprocating grinding technology. To check the workpieces for
their finished dimension and to switch the individual feedrates in the various technological
sections, a measuring device (caliper) which is already in use during the machining can be
used.
Straight or inclined wheel types can be used.
Example for multiple plunge-cutting
A cylinder (diameter 200) is to be machined completely using a wheel (width 70 mm).
When grinding by reciprocating, the wheel is to be fed in from the right and grinding is to be
performed using the "Exact stop fine" motion behavior. A acoustic emission sensor and a
measurement control are installed on the machine.
Additional specified values:
A_SR=0.5 mm
Roughing allowance
A_SL=0.3 mm
Finishing allowance
A_FS=0.2 mm
Fine-finishing allowance
SLZ=0.1 mm
Infeed amount for finishing
FSZ=0.005
Infeed amount for fine-finishing
N_FR=3
Number of sparking-out strokes