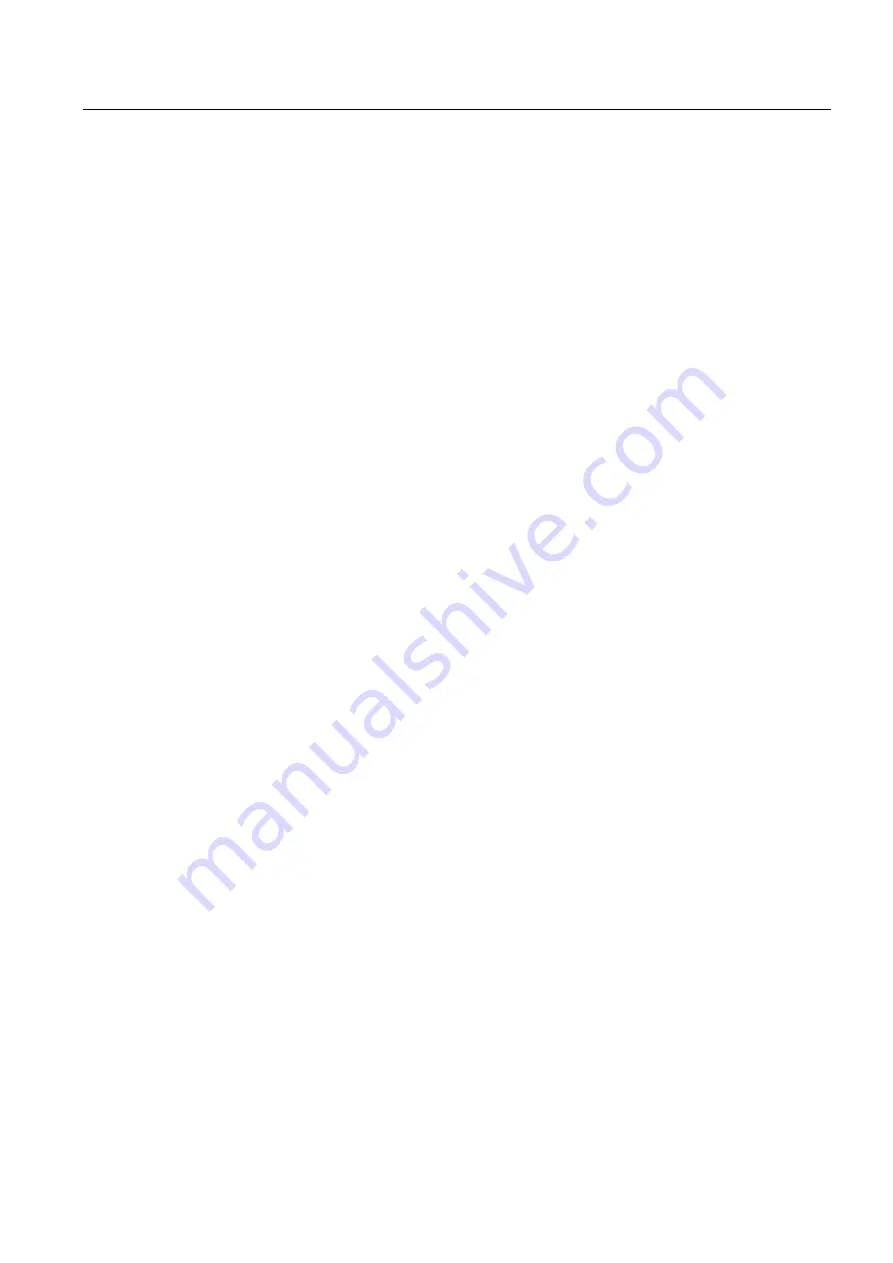
Programming
10.4 Spindle movements
Cylindrical grinding
Programming and Operating Manual, 07/2009, 6FC5398-4CP10-2BA0
281
10.4.4
Gear stages
Functionality
Up to 5 gear stages can be configured for a spindle for speed / torque adaptation.
Programming
The relevant gear stage is selected in the program via M commands:
M40
; Automatic gear stage selection
M41 to M45
; Gear stages 1 to 5
10.4.5
2. Spindle
Function
With SINUMERIK 802D sl plus and 802D sl pro, a 2nd spindle is provided.
For these control systems, the kinematic transformation functions for grinding are possible.
These functions require a second spindle for the driven workpiece.
The main spindle is operated as a rotary axis in these functions.
Master spindle
A series of functions is associated with the master spindle that can only be used with this
spindle:
•
G95
; Rev. feedrate
•
G96, G97
; Constant cutting rate
•
LIMS
; upper speed limit for G96, G97
•
M3, M4, M5, S...
; simple specifications for direction of rotation, stop and speed
The master spindle is defined via configuration (machine data). Generally it is the main
spindle (spindle 1). A different spindle can be defined as master spindle in the program:
•
SETMS(n)
; spindle n (= 1 or 2) is the master spindle as of now.
Switching back can also be performed via:
•
SETMS
; configured master spindle is now master spindle again
•
SETMS (1)
; Spindle 1 is now master spindle again.
The definition of the master spindle changed in the program is only valid until End of
program/program abort. Thereafter, the configured master spindle is again active.