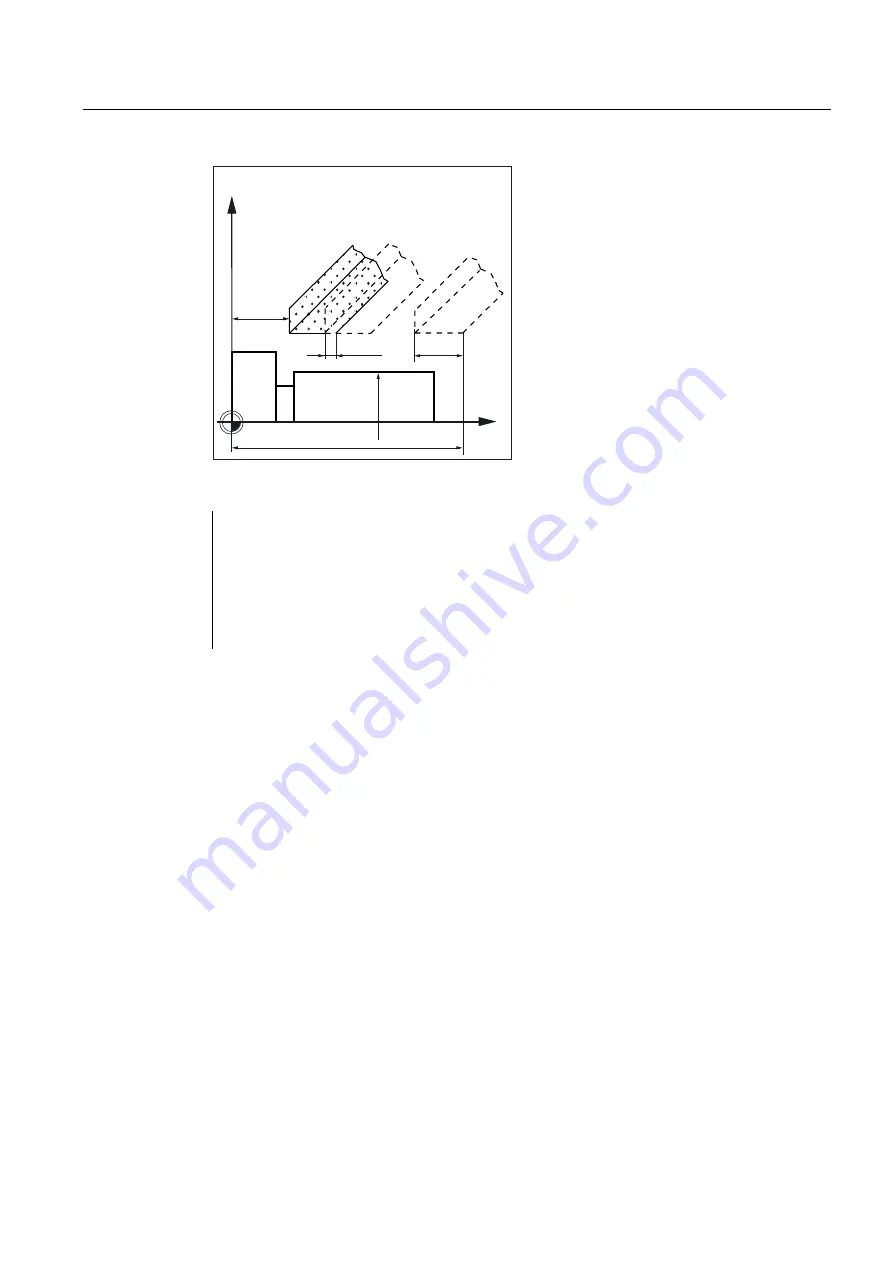
Cycles
9.9 Multiple plunge-cutting – CYCLE411
Cylindrical grinding
Programming and Operating Manual, 07/2009, 6FC5398-4CP10-2BA0
177
;
=
N10 T1 D1 M7
; Determine technology values, coolant ON
N20 S1=2000 M1=3
; Turn on workpiece speed
N30 S2=1100 M2=4
; Turn on wheel speed
N40 CYCLE411(1, 200, 30, 255, 15, 3, 5,
0.5, 0.3, 0.2, 0.1, 0.005, 1, 0, 0, 100,
50, 40, 30, 3, 1, 1, 600, 20)
; Cycle call
N50 M30
; End of program
Sequence of operations
The machining start position is first approached in X, then in Z, corresponding to the initial
position of the grinding wheel in X, if the current X value is less than the X allowance.
The X starting position is calculated as the setpoint di stock all air
allowance. Thereafter, optional surface sparking is done using an acoustic emission sensor,
roughing through plunge-cutting to finishing allowance, retraction to the X starting position
and offsetting of the wheel in the Z direction with overlapping.
Once the roughing plunge-cutting is completed over the whole workpiece width, the starting
position for reciprocation in Z is approached at the position of the finishing allowance in X.
Finishing and fine-finishing are carried out by the infeed amount at the selectable infeed
points using the subsequent reciprocation grinding technology.
The infeed is performed at the reversal points of the reciprocating motion, either on the right,
on the left or at both points. The motion behavior at these reversal points can be
programmed.
After a sparking-out time, the subsequent retraction to the starting position is performed at
the end position for machining.
When using a measurement control, there is a compensation capability with the aid of the
variable _GC_KORR. This parameter specifies whether additional compensation should be
computed for the measurement control.