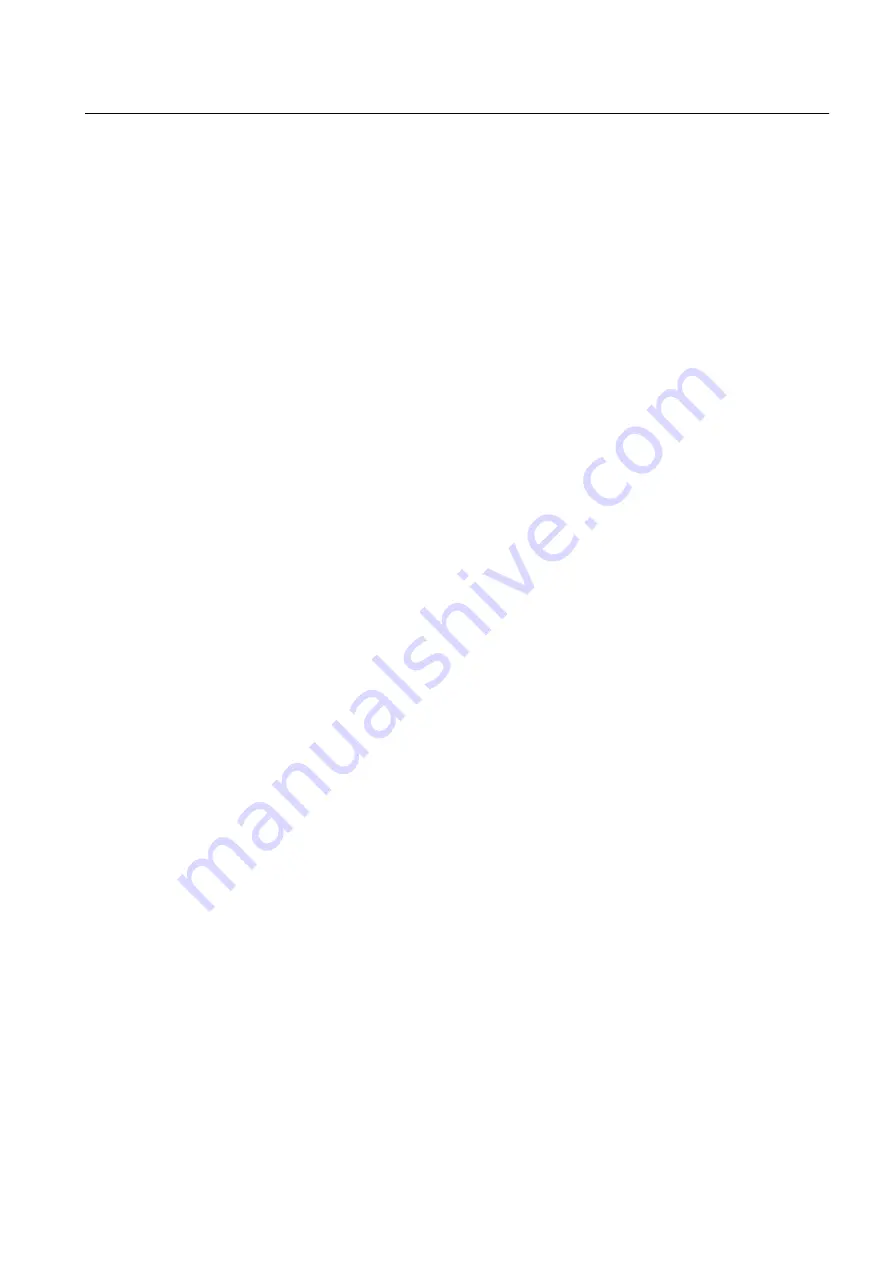
3.5.6
Circuit-breaker (provided by the customer)
To ensure adequate protection for converters, the circuit-breaker provided by the customer
must fulfill the following requirements:
● The maximum time between when the circuit-breaker trips to when a no-current state (I=0)
is reached is 80 ms.
● The circuit breaker must be equipped with an undervoltage tripping function.
● Avoid additional delay times when controlling the circuit breaker. All commands from the
converter to the circuit breaker must act directly without intervention of coupling relays.
● A feedback signal must be available for each of the circuit-breaker states CLOSED and
OPEN. The feedback signals must not be delayed. Consequently, do not use any coupling
relays.
● The circuit-breaker is controlled and released from the converter closed-loop control. If this
has not been enabled, under no circumstances should you switch on the circuit-breaker by
external mechanical or electrical means.
● To protect the converter transformer, ensure that overcurrent protection is in place.
3.5.7
Converter transformer
A two-winding transformer is required for each Active Line Module. When two complete drive
units are connected in parallel, a three-winding transformer with shifted windings can be used
for suppressing line harmonics.
Consider the following properties during the configuration:
● Transformer secondary voltage: 3.3 kV
● Minimum leakage inductance: 1 mH
(short-circuit voltage
u
k
=15% to 28% depending on transformer output)
This value includes all the inductance between the line and the converter: Line short-circuit
inductance, transformer inductance, reactor inductance.
● Transformer taps for voltage adjustments: 2 x ± 2.5
The winding taps are usually located on the high voltage side of the transformer.
Design the transformer for the following loads:
● Max. dU/dt stress at the inverter input terminals: 6 kV/µS
● Peak voltage load phase-phase and phase-ground: 8.4 kV
● Current load with DC component: approx. 4 A to 5 A
Description
3.5 Description of the components
SINAMICS SM150 6SL3845-7NN46-7AA0
Operating Instructions 04/2017
37
Summary of Contents for SINAMICS SM150
Page 2: ...20 04 2017 13 53 V27 00 ...
Page 14: ...Table of contents SINAMICS SM150 6SL3845 7NN46 7AA0 14 Operating Instructions 04 2017 ...
Page 122: ...Start up SINAMICS SM150 6SL3845 7NN46 7AA0 122 Operating Instructions 04 2017 ...
Page 190: ...Maintenance 9 7 Repairs SINAMICS SM150 6SL3845 7NN46 7AA0 190 Operating Instructions 04 2017 ...
Page 192: ...Spare parts SINAMICS SM150 6SL3845 7NN46 7AA0 192 Operating Instructions 04 2017 ...
Page 196: ...Service Support SINAMICS SM150 6SL3845 7NN46 7AA0 196 Operating Instructions 04 2017 ...
Page 217: ......