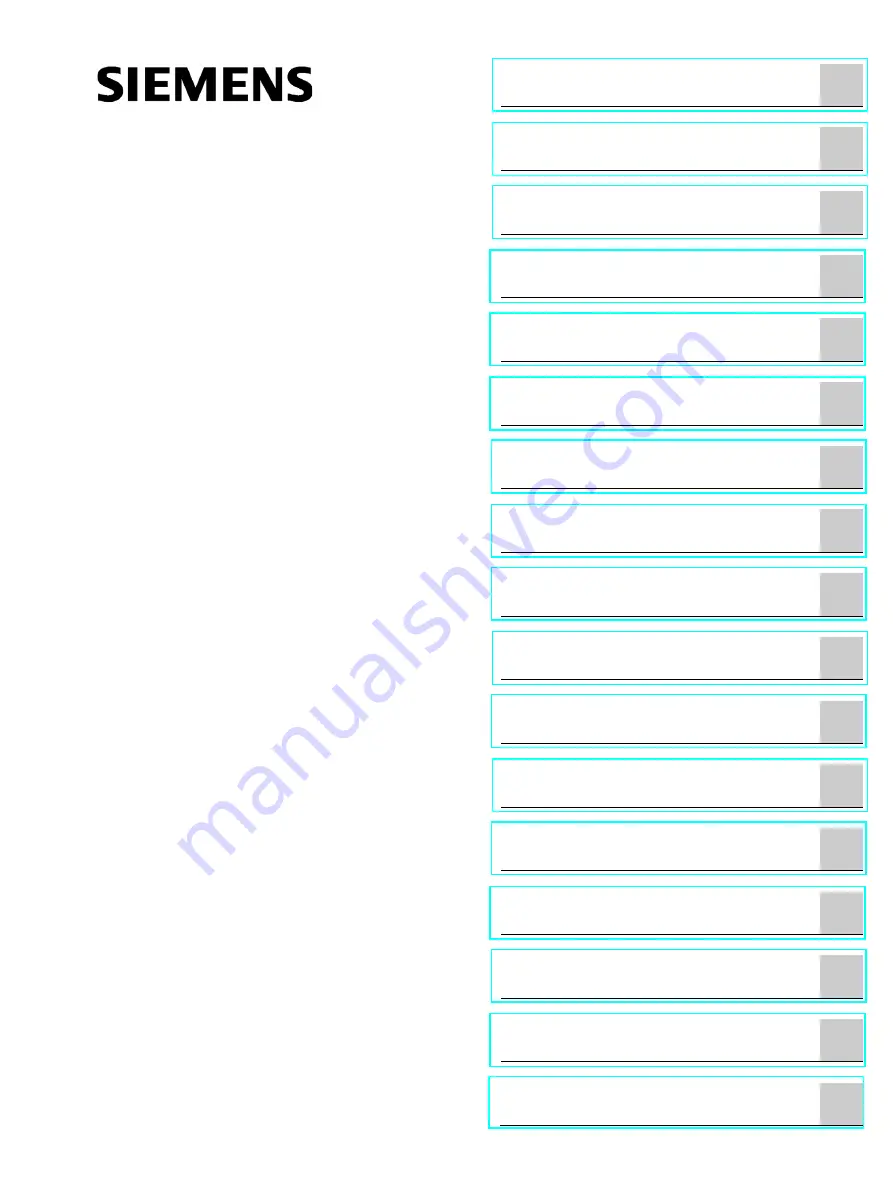
SIMOCODE pro
Industrial Controls
Motor management and
control devices
SIMOCODE pro
System Manual
05/2019
A5E40507475002A/RS-AD/004
Advantages/benefits/configuration
Check list for selecting a device
An overview of system components
Description of system components
Mounting, wiring, connecting, system
interfaces, configuration guidelines
Summary of Contents for SIMOCODE pro C
Page 40: ...Areas of application SIMOCODE pro 40 System Manual 05 2019 A5E40507475002A RS AD 004 ...
Page 46: ...Features SIMOCODE pro 46 System Manual 05 2019 A5E40507475002A RS AD 004 ...
Page 178: ...Accessories SIMOCODE pro 178 System Manual 05 2019 A5E40507475002A RS AD 004 ...
Page 398: ...Glossary SIMOCODE pro 398 System Manual 05 2019 A5E40507475002A RS AD 004 ...