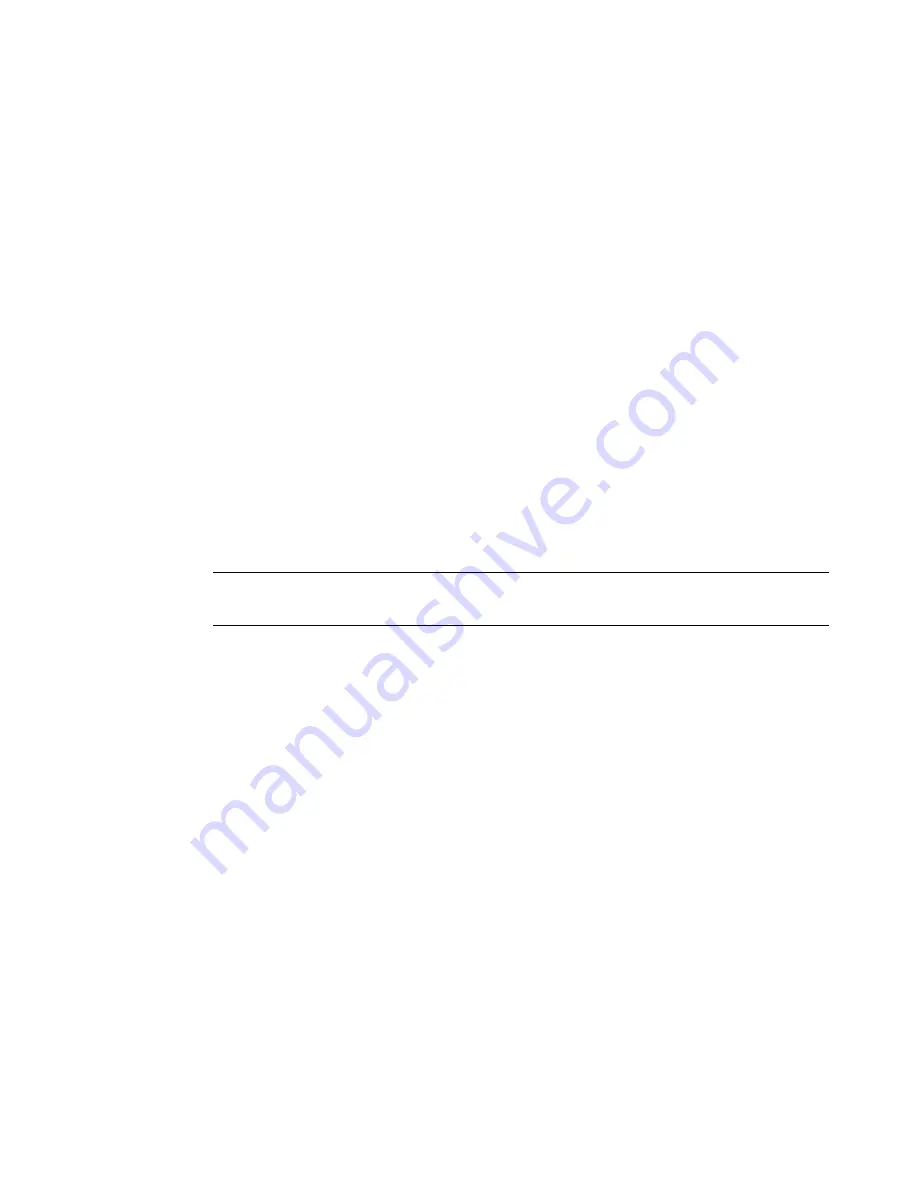
BW500 and BW500/L
Operating Instructions, 12/2016, A5E33482052-AD
107
PID Control
9
The PID control algorithm in the BW500 is designed specifically to work for feed rate control
applications. It is based on motor control type algorithms and includes several anti-wind up
provisions.
One way to prevent wind up is to monitor the input speed frequency from the weighfeeder. If the
input frequency drops below 5 Hz, the PID control output freezes at its current value. Otherwise,
the output winds up to 100% if the feeder is shut off while there is still a set point greater than
zero. When the feeder is turned back on, there would be a surge of product flow until the system
regains stability. With anti-wind up, the feeder can be stopped and started with minimal
disruption to the controlled flow rate.
To operate the BW500 as a controller, address the following:
●
hardware
●
connections
●
setup and tuning
●
programming
Note
PID control not available on the BW500/L.
9.1
Hardware
For the BW500 to operate as a controller, install the optional mA I/O board. Refer to Installation
(Page 21).
9.2
Connections
Connections to process instruments, in addition to standard operating connections, must be
made.
Refer to:
●
Installation (Page 21), specifically:
●
Relay Output (Page 40), for relay connections
●
mA I/O board (Page 43), for mA input and output connections
●
Auxiliary Inputs (Page 38), for optional remote control
Summary of Contents for Milltronics BW500
Page 1: ...Operating Instructions Milltronics BW500 and BW500 L 12 2016 Edition Integrators ...
Page 12: ...Table of contents BW500 and BW500 L 10 Operating Instructions 12 2016 A5E33482052 AD ...
Page 14: ...Safety Notes BW500 and BW500 L 12 Operating Instructions 12 2016 A5E33482052 AD ...
Page 16: ...The Manual BW500 and BW500 L 14 Operating Instructions 12 2016 A5E33482052 AD ...
Page 48: ......
Page 154: ......
Page 218: ...Index BW500 and BW500 L 216 Operating Instructions 12 2016 A5E33482052 AD ...
Page 219: ......