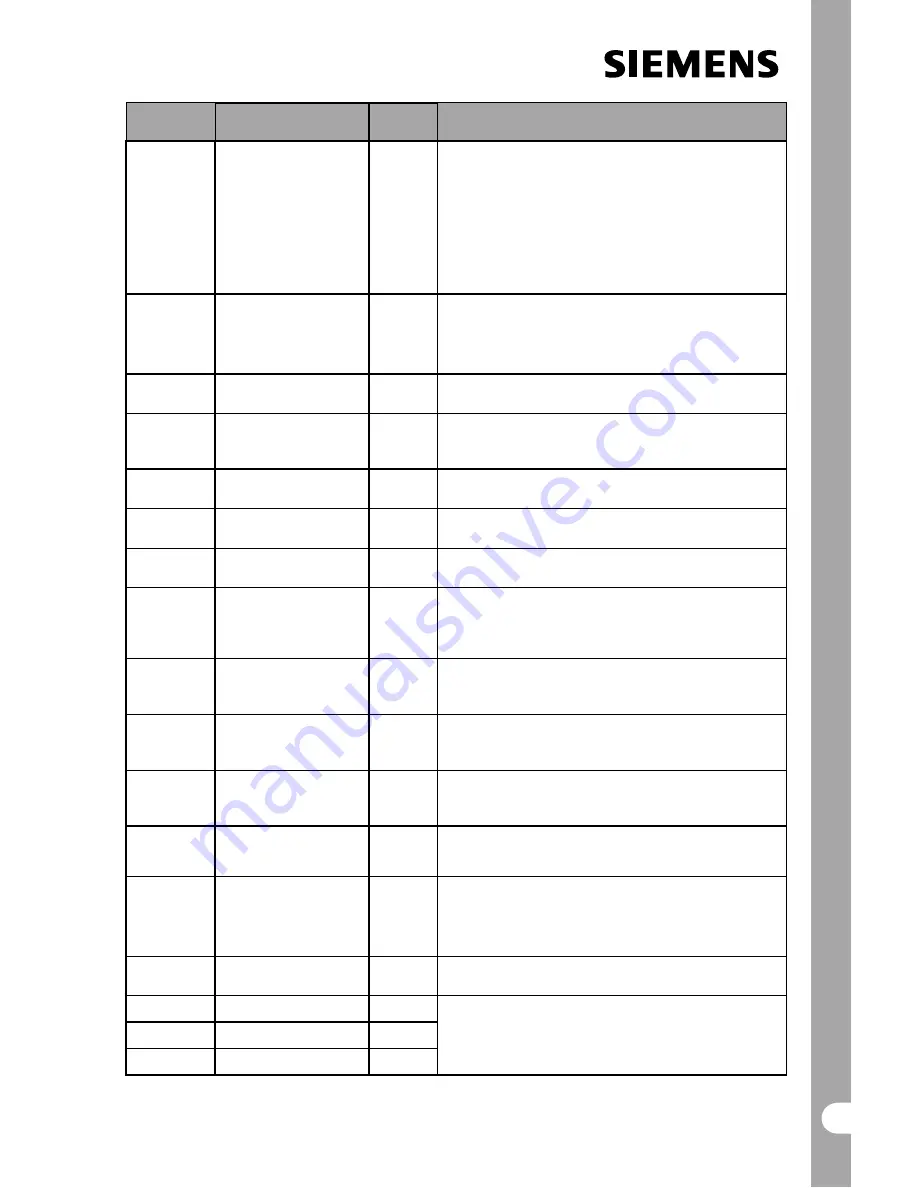
COMBIMASTER & MICROMASTER Integrated
REFERENCE MANUAL
©
Siemens plc. 1999
| G85139-H1731-U300-D2
35
Parameter
Function
Range
[Default]
Description / Notes
P152
••••
Yellow LED function
0 - 5
[5]
0
= Off
1
= On
2
= Fault mode:
On = Tripped
Flashing = Warning
3
= Running mode:
On = Motor running
Flashing = Inverter on but motor
stationary
4
=
Not used
5
= Default mode
(
see table in Operating
Information Section 5
).
P201
PI closed loop mode
0 - 2
[0]
0
= Normal operation (closed loop control
disabled).
1
= Not used
2
= Closed loop control using PI input for
transducer feedback.
P202
••••
P gain
0.0-999.9
[1.0]
Proportional gain.
P203
••••
I gain
0.00 -
99.99
[0.00]
Integral gain.
0.01 corresponds to the longest integral response time.
P205
••••
Sample interval (x 25
ms)
1 - 2400
[1]
Sampling interval of feedback sensor.
P206
••••
Transducer filtering
0 - 255
[0]
0
= Filter off.
1
-
255
= Low pass filtering applied to transducer.
P207
••••
Integral capture range
(%)
0 - 100
[100]
Percentage error above which integral term is reset to zero.
P208
Transducer type
0 - 1
[0]
0
= An increase in motor speed causes an increase in
sensor voltage/current output.
1
= An increase in motor speed causes a decrease in
sensor voltage/current output.
P210
Transducer reading
(%)
0.0 -
100.0
[-]
Read only. Value is a percentage of full scale of the PI input.
(eg.: 100 = 10V / 20mA)
P211
••••
0% setpoint
0.00-
100.00
[0.00]
Value of P210 to be maintained for 0% setpoint.
P212
••••
100% setpoint
0.00-
100.00
[100.00]
Value of P210 to be maintained for 100% setpoint.
P220
••••
PI frequency cut-off
0 - 1
[0]
0
= Normal operation
1
= Switch off inverter at or below minimum
frequency.
P331
Analogue mode
0 - 4
[2]
0
= Internal potentiometer only
1
= External analogue input only
2
= Internal potenti external analogue input
3
= Internal potentiometer fine, external input coarse
4
= Internal potentiometer coarse, external input fine
P332
Fine adjustment (%)
0 - 100
[10]
Percentage of fine tuning adjustment for P331 = 3 or 4.
P700
P701
••••
P702
Specific to PROFIBUS-DP. See PROFIBUS Handbook
for further details. (Access only possible with P099 = 1.)