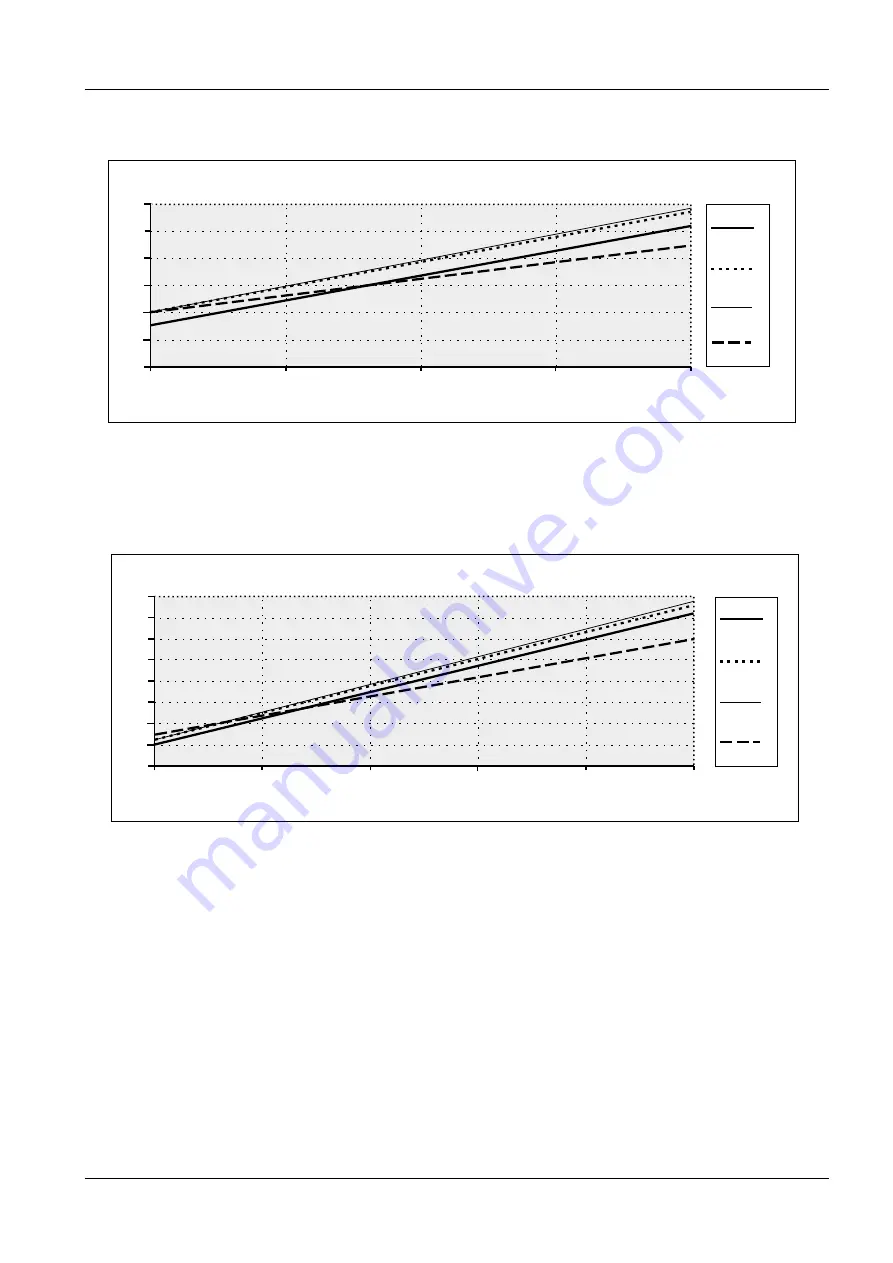
Start-up and functional test of the IONTOMAT
11 - 7
Siemens-Elema AB
Register 3
SP B7-230.033.07
Page 7 of 12
Mammomat 1000/3000
Solna, Sweden
Rev. 03
11.99
SPS-UD
Installation and Start-Up
0
5
10
15
20
30
120
150
quotient
thick object
thin object
O.D.
dark
light
35 kV Mo/Mo Grid
A
B
C
D
Diagram 7
MAM00195
110
130
140
25
0
5
10
15
20
40
110
150
quotient
thick object
thin object
O.D.
dark
light
35 kV Mo/Mo Mag.
A
B
C
D
Diagram 8
MAM00196
100
120
130
140
25
30
35