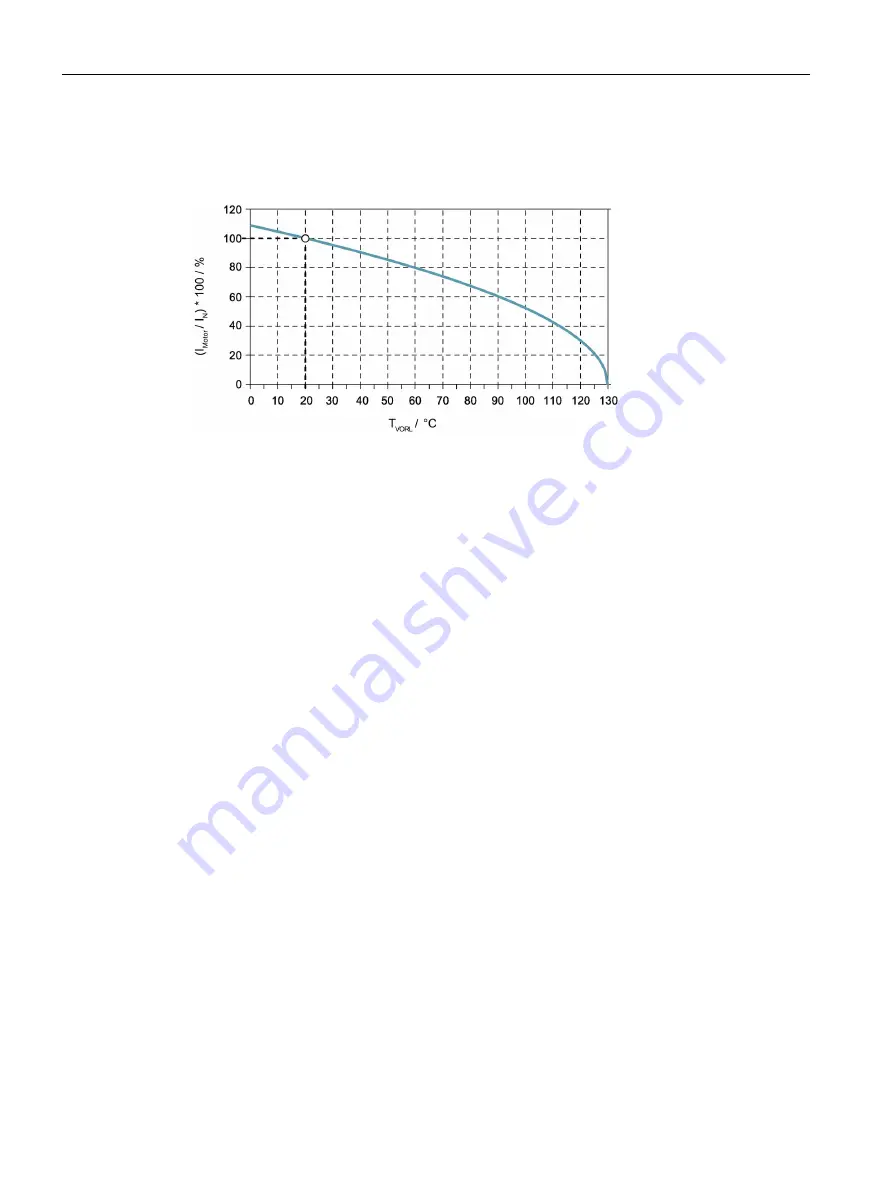
Mechanical properties
3.1 Cooling
1FW6 High Speed built-in torque motors
56
Configuration Manual, 01/2020, 6SN1197-0AE03-0BP3
The following diagram shows the principle dependency of the relative continuous motor
current on the inlet temperature of the cooling water in the main cooler The rotor losses are
omitted as negligible.
Figure 3-1
Influence of the coolant inlet temperature
Heat-exchanger unit
Use a heat-exchanger unit to ensure an inlet temperature of 20 °C. More than one motor can
be operated on a single heat-exchanger unit. The heat-exchanger units are not included in
the scope of supply.
The cooling power is calculated from the sum of the power losses of the connected motors.
Adapt the pump power to the specified flow and pressure loss of the cooling circuit.
For a list of companies from whom you can obtain heat exchanger units, see the appendix.
Dimensioning the heat-exchanger unit
The power loss generated in the motor during continuous operation causes a thermal flow to
take place. The surrounding machine assembly dissipates a small percentage of this thermal
flow. The cooling system coolant dissipates the majority of this thermal flow. The remainder
is dissipated through the surface structure of the motor. Dimension the cooling system rating
in accordance with the data in the data sheets.
If you operate several motors simultaneously on one cooling system, then the cooling
system must be able to dissipate the sum of the individual power losses.
In continuous operation, only load the motor so that the continuous rms torque of the duty
cycle M
eff
does not exceed the rated torque M
N
. In continuous operation, it is not permissible
for the operating point in the M-n diagram to be above the characteristic for S1 duty. As a
consequence, the maximum rms power loss P
V
only reaches the rated power loss P
V,N
.
Summary of Contents for 1FW6092-2PC15-6AB3
Page 1: ...1FW6 High Speed built in torque motors ...
Page 2: ......
Page 299: ......
Page 300: ......