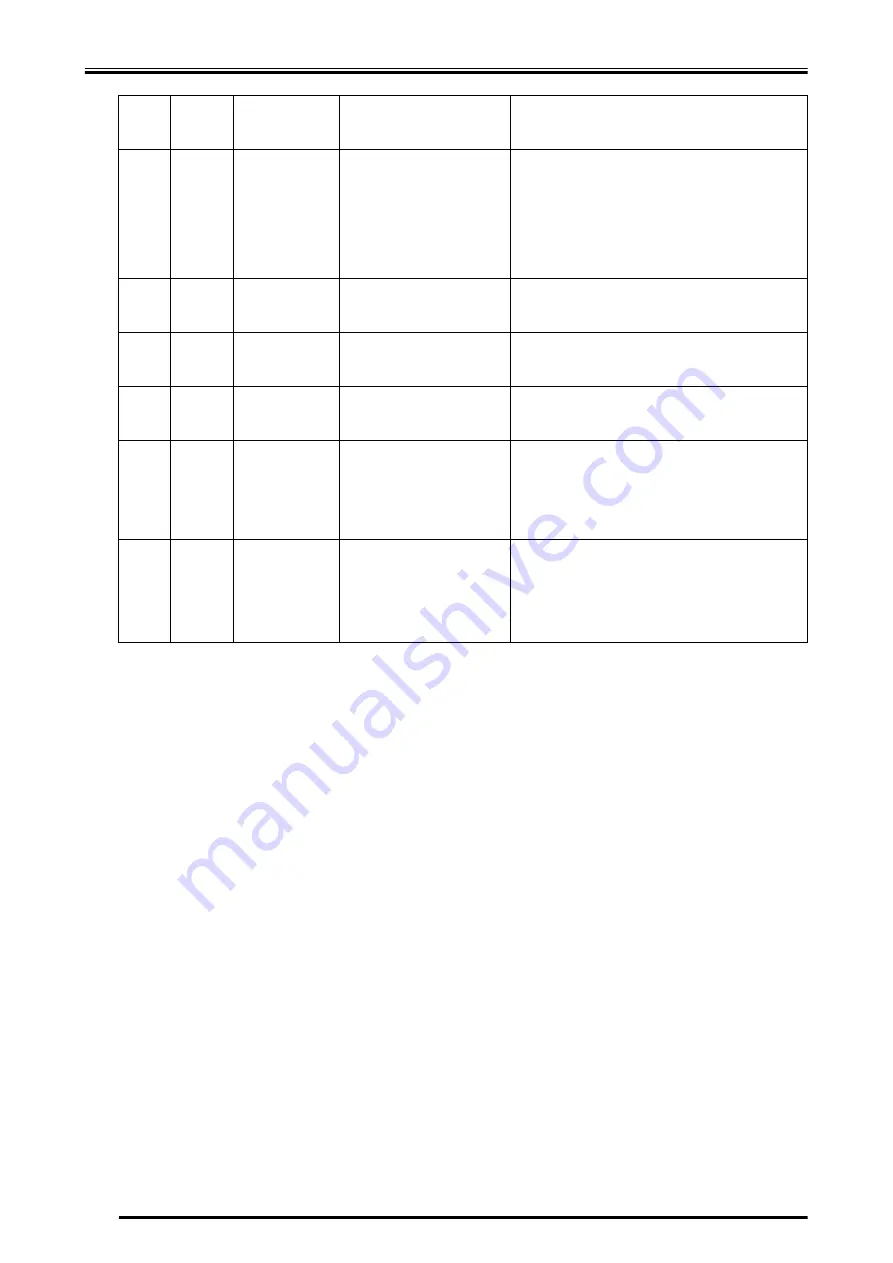
Functional Description of the Connectors/Interfaces
CNC 61.00
Hardware Description CNC 0610510/12
55
DE
ED
137
heat sink-
temperature
reference speed = 0
and
controller OFF
1
the heat sink is too hot.
X
the ambient temperature of the CNC61 is too
hot
DE
DE
138
I
2
t load
reference speed = 0
and
controller OFF
1
the adjusted rated current in the servo amplifier has
been exceeded for quite some time or the motor be-
came too hot.
X
the machine has become more sluggish me-
chanically
X
the parameter of the traveling speed/accelerati-
on is too high
X
error when wiring the motor phases
DD
EE
140
emergency stop
deceleration with the
parameter
"quick delay“
X
emergency stop is released
X
input 0 of the CNC61 is not correctly wired
DD
ED
141
positive
limit switch
reference position = actual
position
reference speed = 0
X
the machine has reached the limit
X
the limit switch or its wiring is faulty
X
input 1 of the CNC61 is not correctly wired
DD
DE
142
negative
limit switch
reference position = actual
position
reference speed = 0
X
the machine has reached the limit
X
the limit switch or its wiring is faulty
X
input 2 of the CNC61 is not correctly wired
DD
DD
143
power fail
deceleration with the
parameter
"quick delay“ and afterwards
ref. speed = 0
and
controller
off
1
main supply is not provided
X
the protective circuit of 24 V has responded
X
the external supply of 24 V is faulty
X
emergency stop is released
X
the main voltage supply of the power module is
not provided
DE
DD
144
tracking error
deceleration with the
parameter
"quick delay“ and afterwards
ref. speed = 0
or
controller
off
1
(acc. to the settings in
the parameter file)
X
the machine has become very sluggish mecha-
nically
X
error when wiring the motor phases
X
the motor accelerates or decelerates too fast
*
error variable in the software
1
the output stage is released and the motor coasts to standstill.
2
this message is also created, if
[A] the CNC61 module is operated with the internal 24 volts and the overvoltage protection (on the
processor card of the CNC 61.00) has responded, or
[B] the CNC61 module is to be supplied with external 24 volts but this voltage is not applied. Rea-
son: The internal or external 24 volts are used for generating the message/signal lines for the
power module. This means that if this voltage is not provided, 0 volt will be applied to the signal
lines which will be interpreted as overvoltage/undervoltage by the CNC 61.00!
Summary of Contents for CNC 0610510
Page 5: ... Content CNC 61 Hardware Description CNC 0610510 12 5 13 Appendix Revisions 101 ...
Page 6: ...Content 6 Hardware Description CNC 0610510 12 CNC 61 ...
Page 8: ...Symbols 8 Symbols ...
Page 14: ...Safety Instruction and Application Advice 14 Safety Instruction and Application Advice ...
Page 16: ...Unit Assembly Complying EMC 16 EMC ...
Page 18: ...General Information 18 Hardware Description CNC 0610510 12 CNC 61 00 ...
Page 24: ...Automation System CNC 61 00 24 Hardware Description CNC 0610510 12 CNC 61 00 ...
Page 31: ... Dimensions CNC 61 00 Hardware Description CNC 0610510 12 31 ...
Page 66: ...General Information Regarding the Wiring 66 Hardware Description CNC 0610510 12 ...
Page 100: ...Appendix Manufacturers 100 List of Manufacturers ...