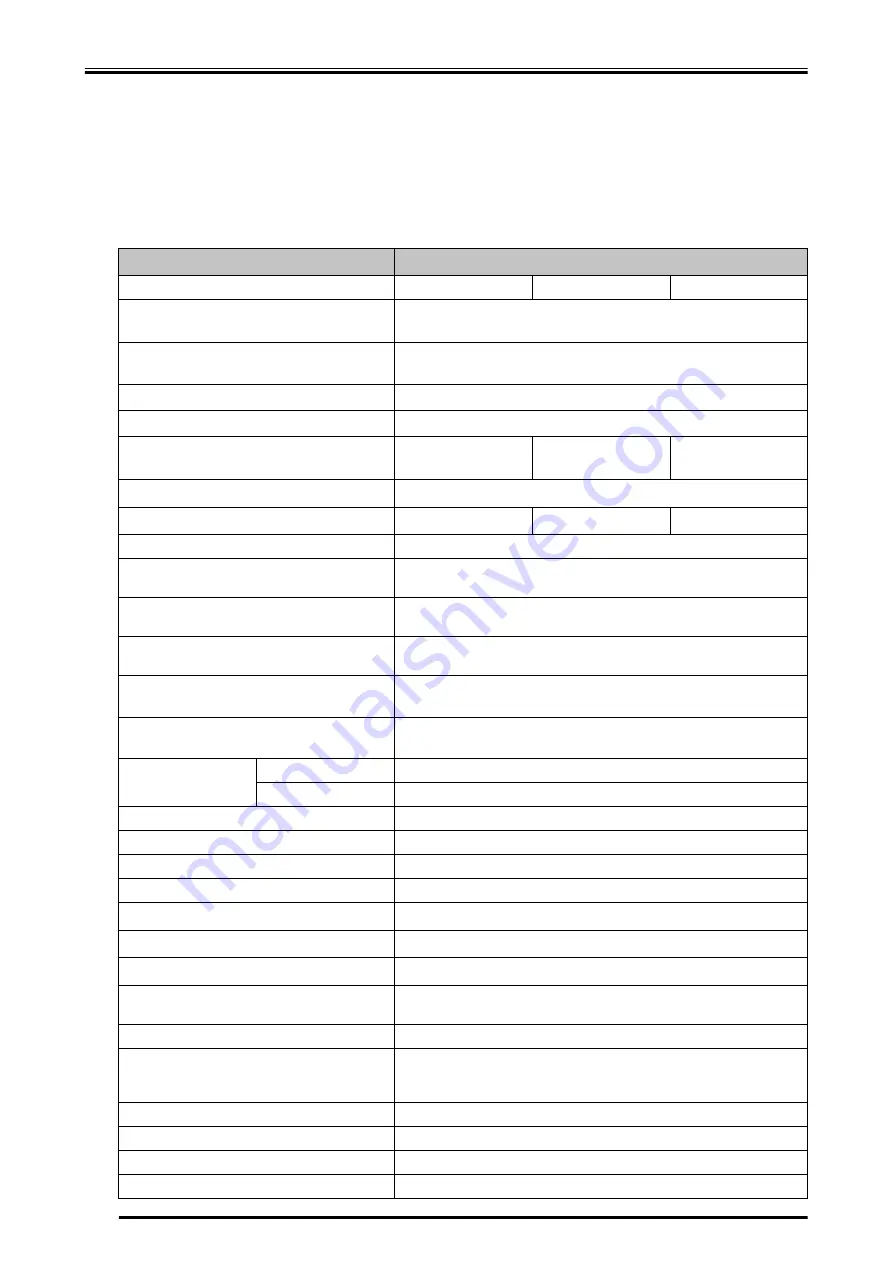
CNC 61.00
Hardware Description CNC 0610510/12
33
7
Technical Data
7.1
Supply Voltage 230 V
AC
Module Type
0610510/12xx
1
Current range/voltage range
DC
EC
SC
Main supply
2
3 x 230 V
AC
-33% / +10%; 50 Hz / 60 Hz
1 x 230 V
AC
-33% / +10%; 50 Hz / 60 Hz
Logic supply
2
2 x 230 V
AC
-33% / +10%; 50 Hz / 60 Hz
same potential as main supply
Max. voltage phase/ground
250 V
AC
Resultant intermediate circuit voltage
325 V
DC
-33% / +10%
Rated current of the ventilated output stage
3,4
10 A
S
7 A
eff
10 A
S
7 A
eff
10 A
S
7 A
eff
Max. values of the output stage at rated current
3 x 230 V
AC
at 0 to 1600 Hz
Peak current
of the output stage for max. 5 s
20 A
S
40 A
S
60 A
S
Switch-off temperature of the output stage
75 °C
Rated direct current of the integrated power
module, single-phase supply
4 A
Rated direct curren of the integrated power mod-
ule, three-phase supply
7 A
Peak direct current of the integrated power mod-
ule, three-phase supply f > 15Hz
50 A for max. 1 s
Mains power of the integrated power module,
230 V
AC
single-phase supply
0.9 kVA
Mains power of the integrated power module,
230 V
AC
three-phase supply
1.6 kVA
Power consumption
Logical unit
max. 20 W
Power unit
max. 5 % of the electrical rated power of the motor, but minimum 20 W
External protection
6 A gL/gG
Internal ballast resistor
20
Ω
/ 10 W
Min. external ballast resistor
15
Ω
Max. activation time of the ballast circuit
750 ms
Overvoltage turn-off limit
410 V
DC
Undervoltage turn-off limit
40 V
DC
Chopper turn-off limit
380 V
DC
Temperature range
5°C to 60°C at a maximum of 95 % relative humidity (no moisture conden-
sation) 100 % rated current up to 40°C
System of protection
IP20
Nominal current reduction:
X
at ambient temperatures >40° C
X
at heights > 1,000 m above mean sea level
-1.5% per 1° C
-15% per 1,000 m
Weight
3.2 kg (0610510xx); 3.6 kg (0610512xx)
Width
65.00 mm (0610510xx); 85 mm (0610512xx)
Height (mounting device included)
318.00 mm
Depth
173.00 mm
Summary of Contents for CNC 0610510
Page 5: ... Content CNC 61 Hardware Description CNC 0610510 12 5 13 Appendix Revisions 101 ...
Page 6: ...Content 6 Hardware Description CNC 0610510 12 CNC 61 ...
Page 8: ...Symbols 8 Symbols ...
Page 14: ...Safety Instruction and Application Advice 14 Safety Instruction and Application Advice ...
Page 16: ...Unit Assembly Complying EMC 16 EMC ...
Page 18: ...General Information 18 Hardware Description CNC 0610510 12 CNC 61 00 ...
Page 24: ...Automation System CNC 61 00 24 Hardware Description CNC 0610510 12 CNC 61 00 ...
Page 31: ... Dimensions CNC 61 00 Hardware Description CNC 0610510 12 31 ...
Page 66: ...General Information Regarding the Wiring 66 Hardware Description CNC 0610510 12 ...
Page 100: ...Appendix Manufacturers 100 List of Manufacturers ...