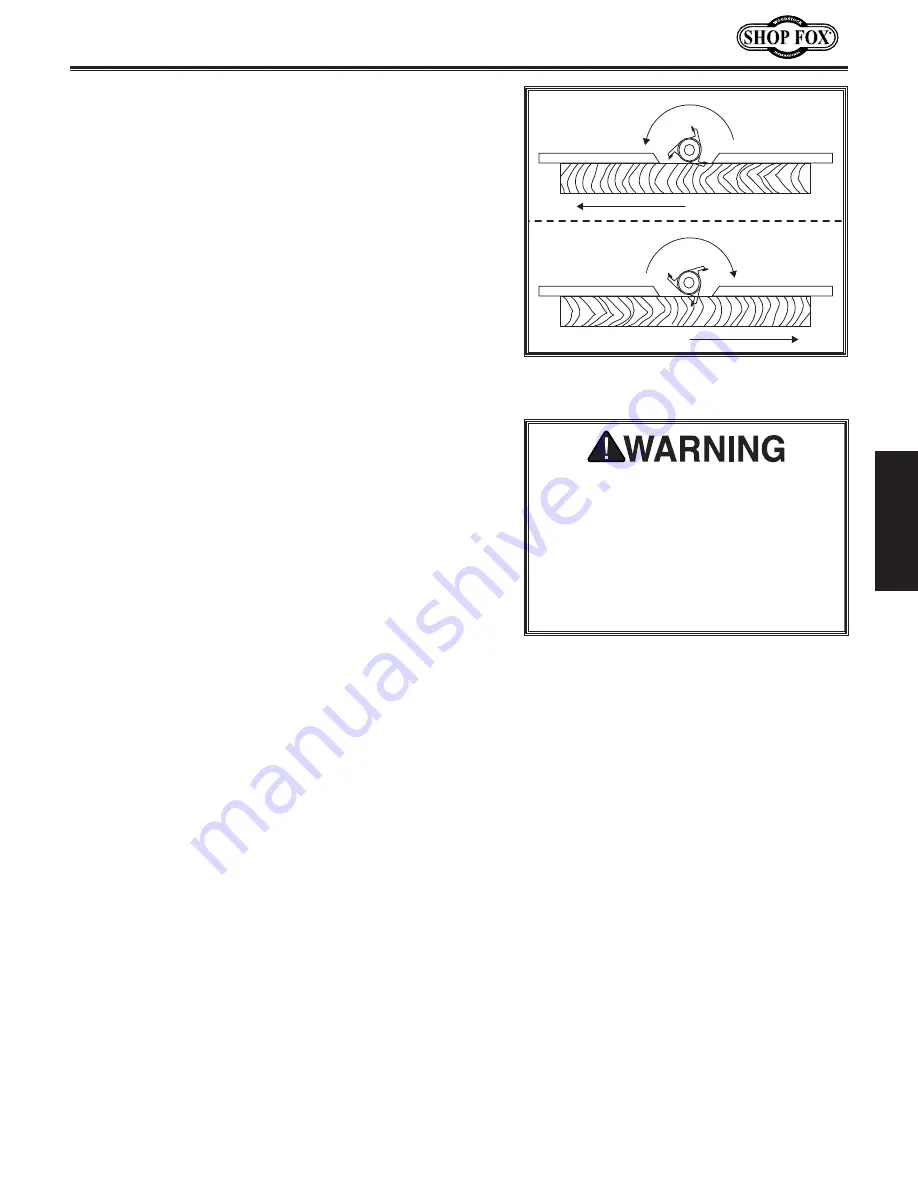
-21-
SE
TU
P
Model W1807 7
1
⁄
2
HP Heavy-Duty Industrial Tilting Spindle Shaper
Verifying Spindle Rotation
To operate the shaper safely and reduce the risk of
workpiece kickback, you must verify that the spindle is
rotating in the correct direction as indicated by the for-
ward/reverse switch (see
Figure 14
).
Safely start and stop the shaper. As the spindle slows,
visually verify the rotation direction.
— When the
Fwd
(forward) direction is selected, the
spindle must rotate
counterclockwise
as you look
down on it from above. The workpiece passes the
cutter from right-to-left.
— When the
Rev
(reverse) direction is selected, the
spindle will rotate
clockwise
as you look down on
it from above. The workpiece passes the cutter
from left-to-right.
An incorrect spindle rotation can be resolved by switch-
ing any two hot leads at the power connection. If you are
unsure how to do this, have a qualified electrician do it
for you. If this procedure does not solve the spindle rota-
tion problem, call Tech Support for help.
�������
�����
��������
��������������
�������
�����
��������
��������������
Figure 14.
Illustration of correct spindle
and cutter rotation.
You MUST verify that the spindle rotates
in the expected direction according
the position of the forward/reverse
switch. The workpiece MUST be fed
into the cutter against the rotation of
the cutter. Otherwise, workpiece kick-
back could occur resulting in serious
personal injury.
Summary of Contents for W1807
Page 6: ......
Page 9: ...3 Model W1807 71 2 HP Heavy Duty Industrial Tilting Spindle Shaper INTRODUCTION...
Page 10: ...4 Model W1807 71 2 HP Heavy Duty Industrial Tilting Spindle Shaper INTRODUCTION...
Page 58: ...52 PARTS Model W1807 71 2 HP Heavy Duty Industrial Tilting Spindle Shaper Table Cabinet...
Page 64: ......