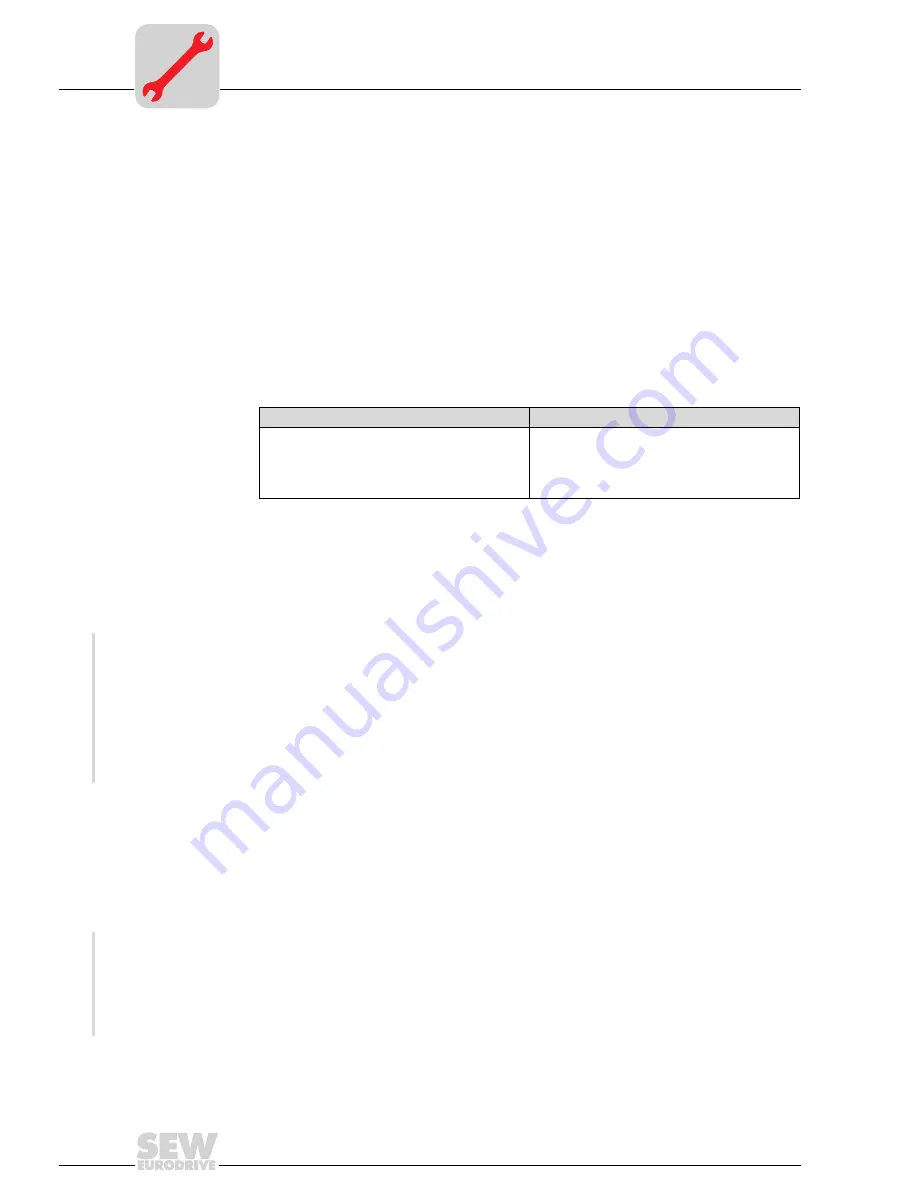
4
12
R..7, F..7, K..7, S..7, Spiroplan
®
W Gear Units – Operating Instructions
Mechanical Installation
4
Mechanical Installation
4.1
Required tools / material
•
Set of spanners
•
Torque wrench (for shrink discs, AQ motor adapter, input shaft assembly with
centering shoulder)
•
Mounting device
•
Shims and distance rings, if necessary
•
Fastening devices for input and output elements
•
Lubricant (e.g. NOCO
®
fluid)
•
Agent for securing screws, e.g. Loctite 243 (for input shaft assembly with centering
shoulder)
Mounting
tolerances
4.2
Before you begin
The drive may
only be installed
if
•
the entries on the name plate of the drive match the mains power supply,
•
the drive is undamaged (no damage caused by transport or storage) and
•
it is certain that the following requirements have been fulfilled:
-
with standard gear units:
ambient temperature according to lubricant table in section lubricants (see standard),
no oil, acid, gas, vapors, radiation, etc.
-
with special versions:
drive configured in accordance with the ambient conditions
-
with helical worm/Spiroplan
®
W gear units:
no large external mass moments of inertia which could exert a retrodriving load on
the gear unit
[where h’ (retrodriving) = 2 – 1/
η
< 0.5 self-locking]
4.3
Preliminary work
The output shafts and flange surfaces must be thoroughly cleaned of anti-corrosion
agents, contamination or such like (use a commercially available solvent). Do not let the
solvent come into contact with the sealing lips of the oil seals – material damage!
Long-term
storage of gear
units
Gear units of the “extended storage” type have
•
a mineral oil fill (CLP) or synthetic oil fill (CLPHC) suitable for the mounting position
so the unit is ready to run. However, you should still check the oil level prior to
startup (see section "Inspection/Maintenance" / "Inspection/Maintenance work").
•
a higher oil level with synthetic oil CLP PG). Correct the oil level prior to startup (see
section "Inspection/Maintenance" / "Inspection/Maintenance work").
Shaft end
Flanges
Diameter tolerance according to DIN 748
•
ISO k6 for solid shafts with
∅
≤
50 mm
•
ISO m6 for solid shafts with
∅
> 50 mm
•
ISO H7 for hollow shafts
•
Center hole according to DIN 332, shape DR..
Centering shoulder tolerance according to
DIN 42948
•
ISO j6 with b1
≤
230 mm
•
ISO h6 with b1> 230 mm
Summary of Contents for F 27 Series
Page 2: ...SEW EURODRIVE...