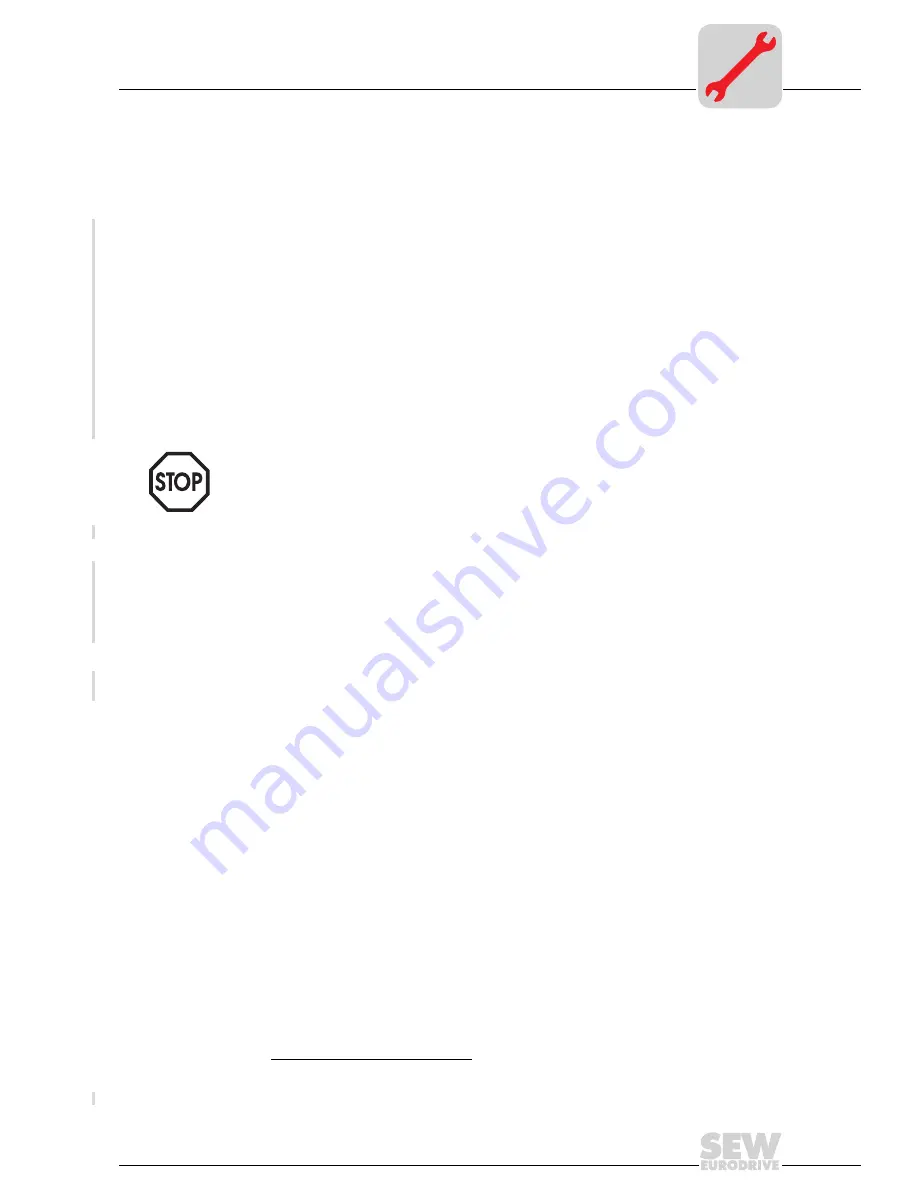
R..7, F..7, K..7, S..7, Spiroplan
®
W Gear Units – Operating Instructions
13
4
Mechanical Installation
4.4
Installing the gear unit
The gear unit or geared motor must be mounted/installed in the specified mounting po-
sition on a level
1
, vibration-absorbing and torsionally rigid support structure (Spiroplan
®
gear units are not dependent on mounting position). Do not tighten housing legs and
mounting flanges against each other and pay attention to the approved overhung and
axial loads
Use only bolts of 8.8 quality for installation of the geared motors
Use bolts of 10.9 quality for fastening of flanges to transmit the rated torques listed in
the catalog for the following helical geared motors in flange design (RF..) and in foot/
flange version (R..F):
•
RF37, R37F with flange-
∅
120 mm
•
RF47, R47F with flange-
∅
140 mm
•
RF57, R57F with flange-
∅
160 mm
At this point of assembly, please check that the oil filling is as prescribed for the moun-
ting position (see "Lubricants" / "Lubricant fill levels" or data on nameplate). In case of
mounting position change, adjust lubricant filling quantities accordingly.
Please consult our service department, if the mounting position for K gear units is chan-
ged to M5 or M6 or within these mounting positions.
Please consult our service department, if the mounting position of S units in sizes S47
... S97 is to be changed to mounting position M2.
Use plastic inserts (2 – 3 mm thick) if there is a risk of electrochemical corrosion between
the gear unit and the driven machine (connection between different metals such as cast
iron and high-grade steel)! Also fit the bolts with plastic washers! Ground the housing
additionally – use the grounding bolts on the motor.
Installation in
damp areas or in
the open
Gear units are supplied in corrosion-resistant versions for use in damp areas or in the
open air. Any damage to the paintwork (e.g. on the breather valve) must be repaired.
1. Maximum permitted flatness error for flange mounting (approximate values with refer-
ence to DIN ISO 1101): with
→
flange 120...600 mm max. error 0.2...0.5 mm
Oil check screws, drain screws and breather valves have to be freely accessible!
Summary of Contents for F 27 Series
Page 2: ...SEW EURODRIVE...