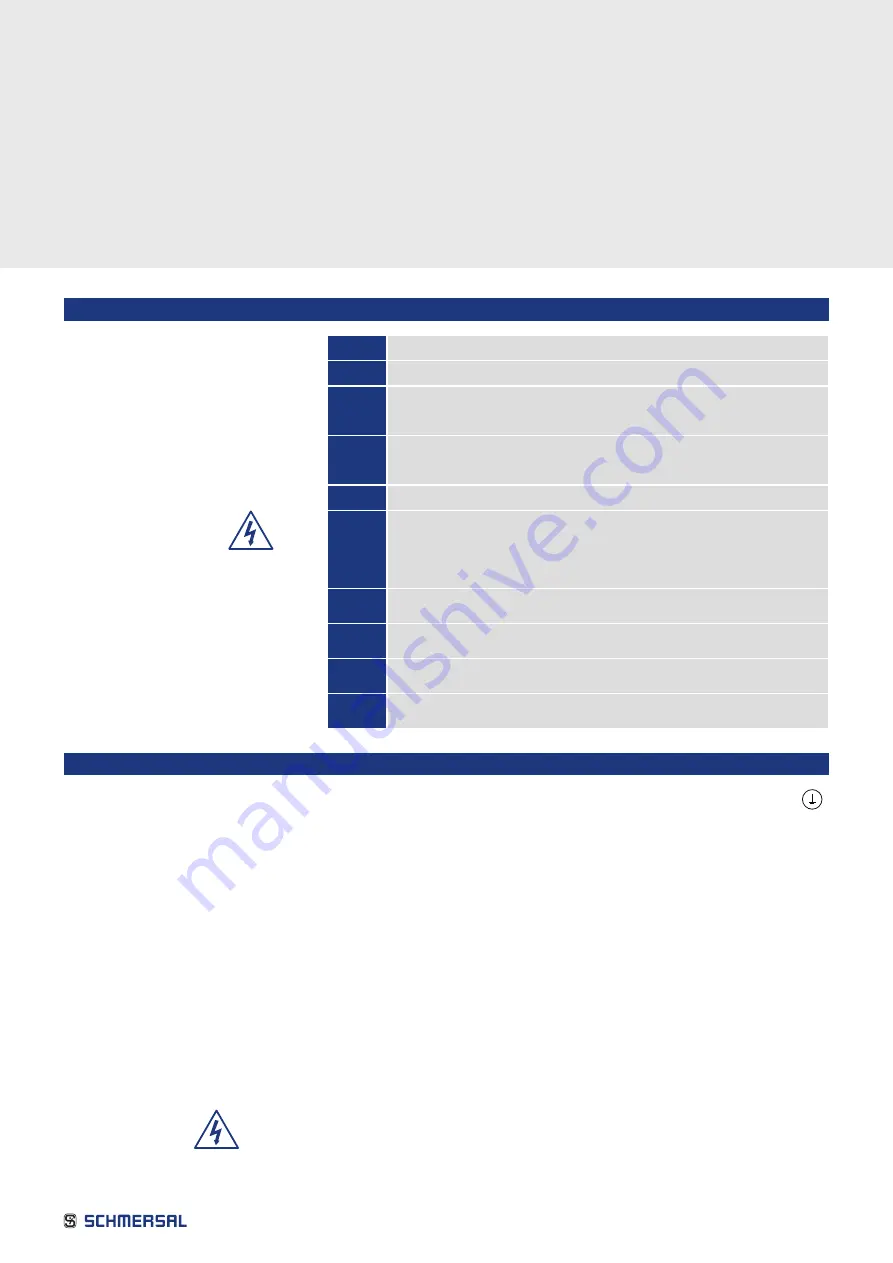
5
1.2 Warning
1.3 Earthing and earth fault protection
1
The AC drive is meant for fixed installations only.
2
Do not perform any measurements when the AC drive is connected to the mains.
3
The earth leakage current of the AC drives exceeds 3.5mA AC. According to
standard EN61800-5-1, a reinforced protective ground connection must be
ensured. See chapter 1.3.
4
If the AC drive is used as a part of a machine, the machine manufacturer is
responsible for providing the machine with a supply disconnecting device
(EN 60204-1).
5
Only spare parts delivered by PRAXI
®
can be used.
6
At power-up, power break or fault reset the motor will start immediately if the
start signal is active, unless the pulse control for Start/Stop logic has been
selected. Futhermore, the I/O functionalities (including start inputs) may change
if parameters, applications or software are changed. Disconnect, therefore, the
motor if an unexpected start can cause danger.
7
The motor starts automatically after automatic fault reset if the auto restart
function is activated. See the Application Manual for more detailed information.
8
Prior to measurements on the motor or the motor cable, disconnect the motor
cable from the AC drive.
9
Do not touch the components on the circuit boards. Static voltage discharge
may damage the components.
10
Check that the EMC level of the AC drive corresponds to the requirements of
your supply network.
The AC drive must always be earthed with an earthing conductor connected to the earthing terminal marked with
.
The earth leakage current of the drive exceeds 3.5mA AC. According to EN61800-5-1, one or more of the following
conditions for the associated protective circuit shall be satisfied:
a.
The protective conductor shall have a cross-sectional area of at least 10 mm
2
Cu or 16 mm
2
Al, through its total run.
b. Where the protective conductor has a cross-sectional area of less than 10 mm
2
Cu or 16 mm
2
Al, a second
protective conductor of at least the same cross-sectional area shall be provided up to a point where the protective
conductor has a cross-sectional area not less than 10 mm
2
Cu or 16 mm
2
Al.
c. Automatic disconnection of the supply in case of loss of continuity of the protective conductor.
The cross-sectional area of every protective earthing conductor which does not form part of the supply cable or cable
enclosure shall, in any case, be not less than:
■
2.5mm
2
if mechanical protection is provided or
■
4mm
2
if mechanical protection is not provided.
The earth fault protection inside the AC drive protects only the drive itself against earth faults in the
motor or the motor cable. It is not intended for personal safety.
Due to the high capacitive currents present in the AC drive, fault current protective switches may
not function properly.
Do not perform any voltage withstand tests on any part of the AC drive.
There is a certain procedure according to which the tests shall be
performed. Ignoring this procedure may result in damaged product.
Summary of Contents for Praxi 100
Page 1: ...Safe solutions for your industry Manual MODBUS Praxi 100...
Page 51: ...51...