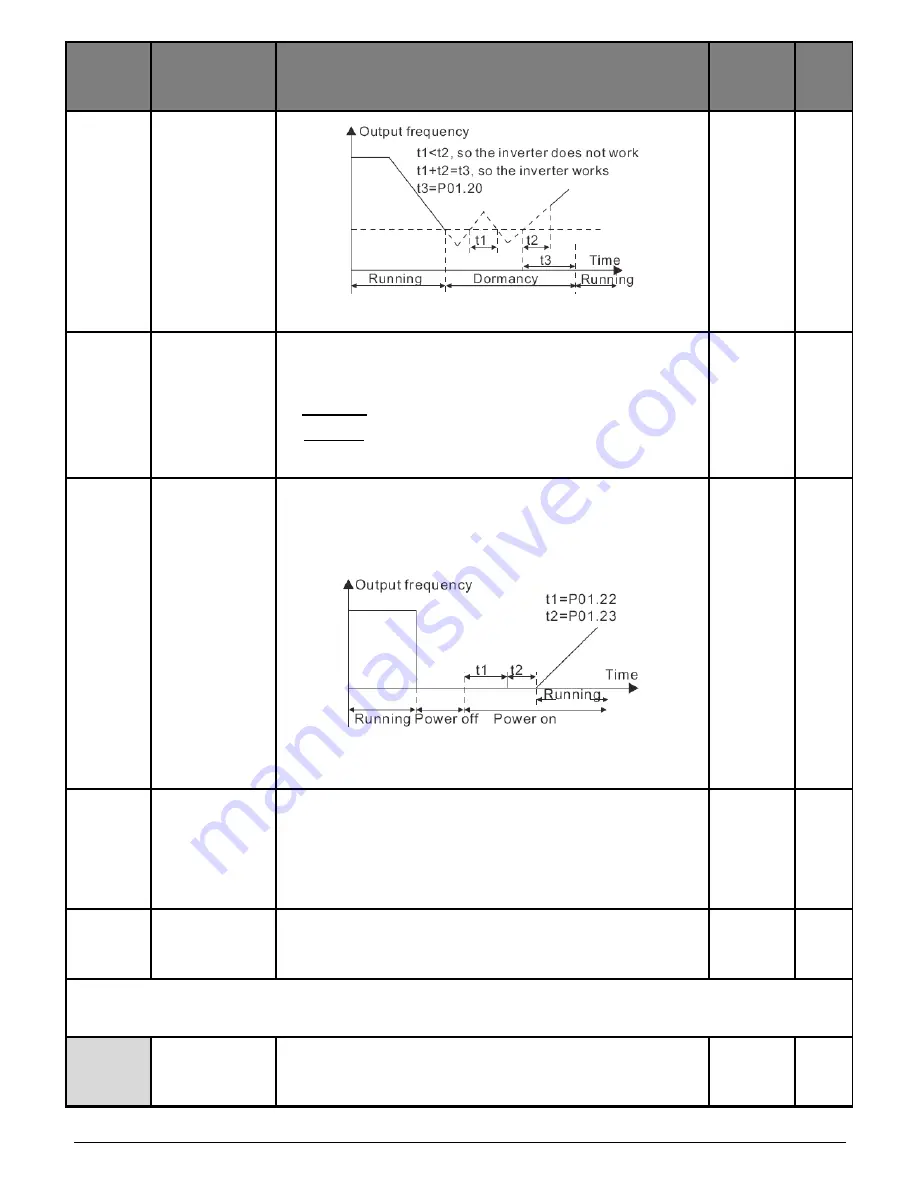
Function Parameters
31 - 104
Function
code
Name
Detailed instruction of parameters
Default
value
Modify
Setting range: 0.0~3600.0s (valid when P01.19=2)
P01.21
Restart after
power off
This function can enable the inverter start or not after the
power off and then power on.
0: Disabled
1: Enabled
, if the starting need is met, the inverter will run
automatically after waiting for the time defined by P01.22.
0
○
P01.22
The waiting
time of restart
after power off
The function determines the waiting time before the
automatic running of the inverter when powering off and then
powering on.
Setting range: 0.0~3600.0s (valid when P01.21=1)
1.0s
○
P01.23
Start delay time
The function determines the brake release after the running
command is given, and the inverter is in a stand-by state and
wait for the delay time set by P01.23
Setting range: 0.0~60.0s
0.0s
○
P01.24
Delay of the
stopping speed
Setting range: 0.0~100.0 s
0.0s
○
P02 Group Motor
P02.01
Motor rated
power
0.1~3000.0kW
Depends
on model
◎
Summary of Contents for CV10-002-S2
Page 1: ...USER MANUAL INVERTER CONTROLVIT CV10...
Page 2: ......
Page 67: ...Function Parameters 67 104 5 2 Diagram of quick start...
Page 100: ......
Page 101: ......
Page 102: ......
Page 103: ......