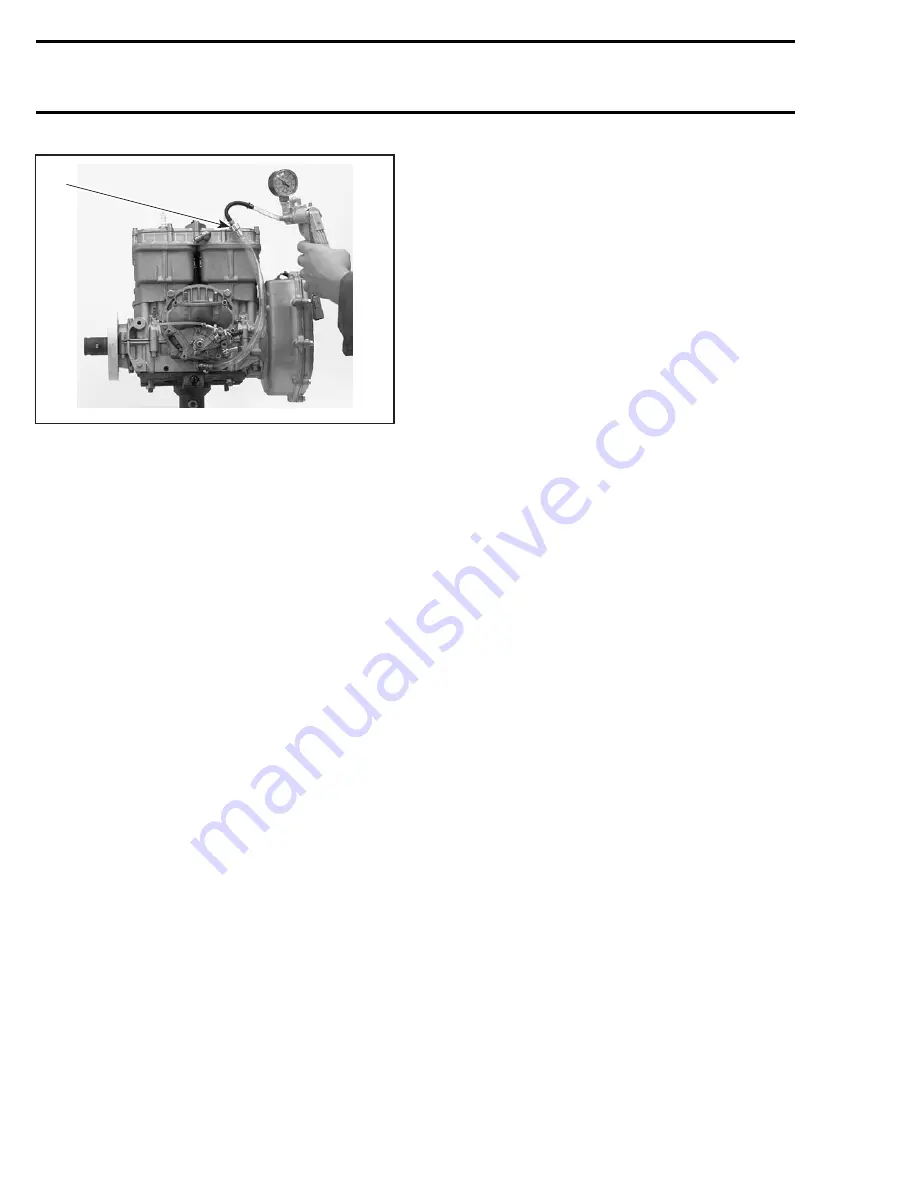
Section 02 717 ENGINE
Subsection 01 (LEAK TEST)
F01B32A
1
1. Pump with reducer and nipple
Activate pump and pressurize to 34 kPa (5 PSI).
Check plug of the rotary valve shaft in crankcase.
Remove PTO side spark plug. If pressure drops,
it indicates a defective PTO side crankshaft inner
seal or crankcase is not sealed correctly.
Remove MAG side spark plug. If pressure drops,
it indicates a defective MAG side crankshaft inner
seal or crankcase is not sealed correctly.
If the above mentioned components are not leak-
ing and there is a pressure drops, remove the ro-
tary valve cover. Check the seal of the rotary valve
shaft.
If the rotary valve shaft is not leaking, it could
indicates a defective engine casting. Disassem-
ble engine and carefully check for defects in cast-
ings. Pay attention to tapped holes which may go
through sealed areas of engine and thus lead to
leakage.
14
smr2005-075
www.SeaDooManuals.net