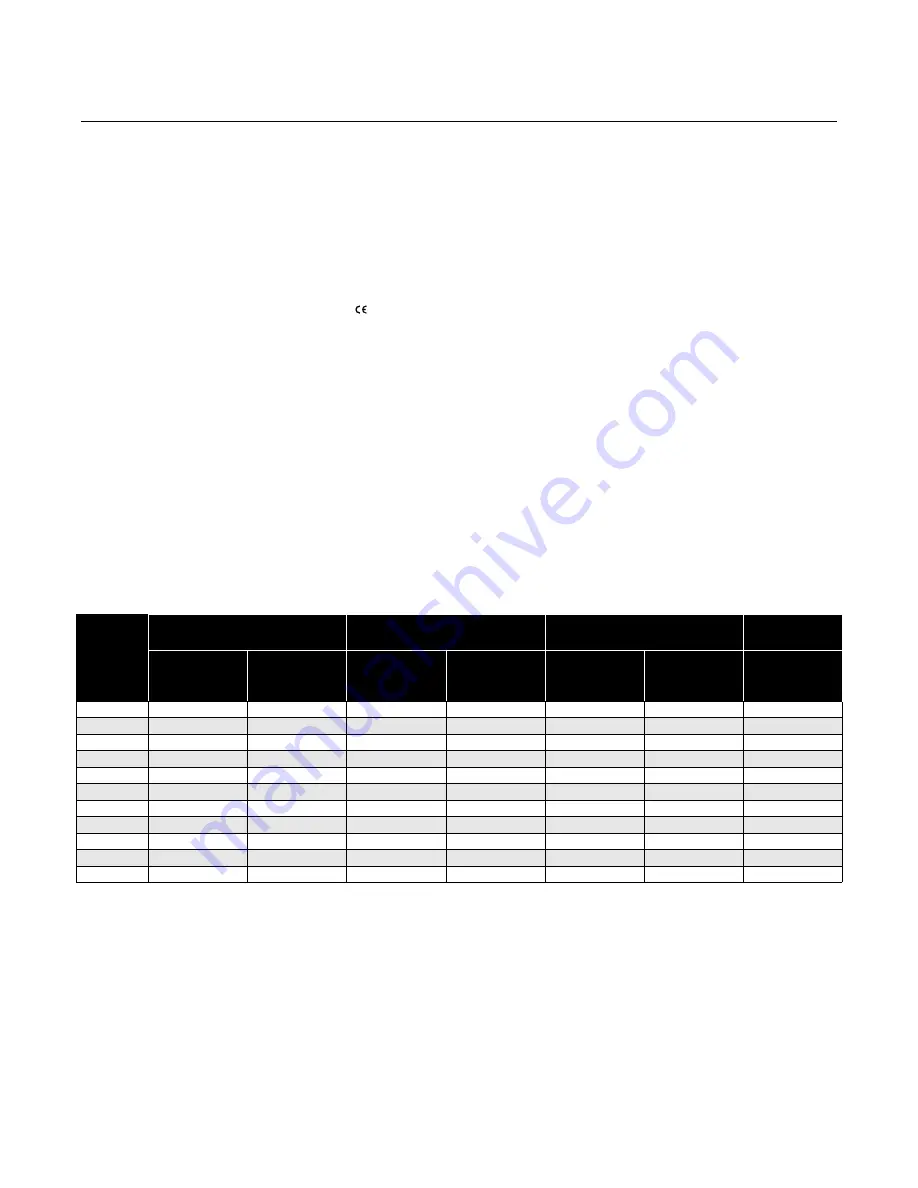
Reference Manual
00809-0100-4664, Rev BA
January 2010
Rosemount 8712
B-2
Canadian Standards Association (CSA)
N0
Non-incendive for Class I, Division 2, Groups A, B, C, and D non-flammable fluids (T4 at 40
°C), and Dust-ignition proof Class II/III, Division 1, Groups E, F, and G (T4 at 40 °C)
Hazardous locations; Enclosure Type 4X
European Certifications
N1
ATEX Type n
ATEX Certificate No: BASEEFA 05ATEX0170X
EEx nA nL IIC T4 (Ta = -40 °C to + 60 °C)
V
max
= 42 V DC
0575
Special Conditions for Safe Use (x)
The apparatus is not capable of withstanding the 500V insulation test required by Clause
8.1of EN 60079-15: 2003. This must be taken into account when installing the apparatus.
International Certifications
IECEx
N7
IECEx Type n
Certificate No: IECEx BAS 07.0036X
Ex nA nL IIC T4 (Ta = -40 °C to + 60 °C)
V
max
= 42 V DC
Special Conditions for Safe Use (x)
The apparatus is not capable of withstanding the 500V insulation test required by Clause
6.8.1of IEC 60079-15: 2005. This must be taken into account when installing the apparatus.
Sensor Approval
Information
Approval
Codes
Rosemount 8705 Sensor
Rosemount 8707 Sensor
Rosemount 8711 Sensor
Rosemount 8721
Sensors
For
Non-flammable
Fluids
For Flammable
Fluids
For
Non-flammable
Fluids
For Flammable
Fluids
For
Non-flammable
Fluids
For Flammable
Fluids
For
Non-flammable
Fluids
NA
•
•
N0
•
•
•
ND
•
•
•
•
N1
•
•
•
•
N5
•
•
•
•
•
•
N7
•
•
•
•
ND
•
•
•
•
NF
•
•
•
•
E1
•
•
•
•
E5
(1)
•
•
•
•
KD
(2)
•
•
•
•
(1) Available in line sizes up to 8 in. (200 mm) only.
(2) Refer to Table B-2 on page B-4 for relation between ambient temperature, process temperature, and temperature class.
Summary of Contents for 8712
Page 2: ......
Page 4: ......
Page 26: ...Reference Manual 00809 0100 4664 Rev BA January 2010 Rosemount 8712 2 16 ...
Page 84: ...Reference Manual 00809 0100 4664 Rev BA January 2010 Rosemount 8712 4 46 ...
Page 102: ...Reference Manual 00809 0100 4664 Rev BA January 2010 Rosemount 8712 5 18 ...
Page 114: ...Reference Manual 00809 0100 4664 Rev BA January 2010 Rosemount 8712 6 12 ...
Page 154: ...Reference Manual 00809 0100 4664 Rev BA January 2010 Rosemount 8712 D 6 ...
Page 194: ...Reference Manual 00809 0100 4664 Rev BA January 2010 Rosemount 8712 E 40 ...
Page 208: ...Reference Manual 00809 0100 4664 Rev BA January 2010 Rosemount 8712 F 14 ...
Page 211: ......