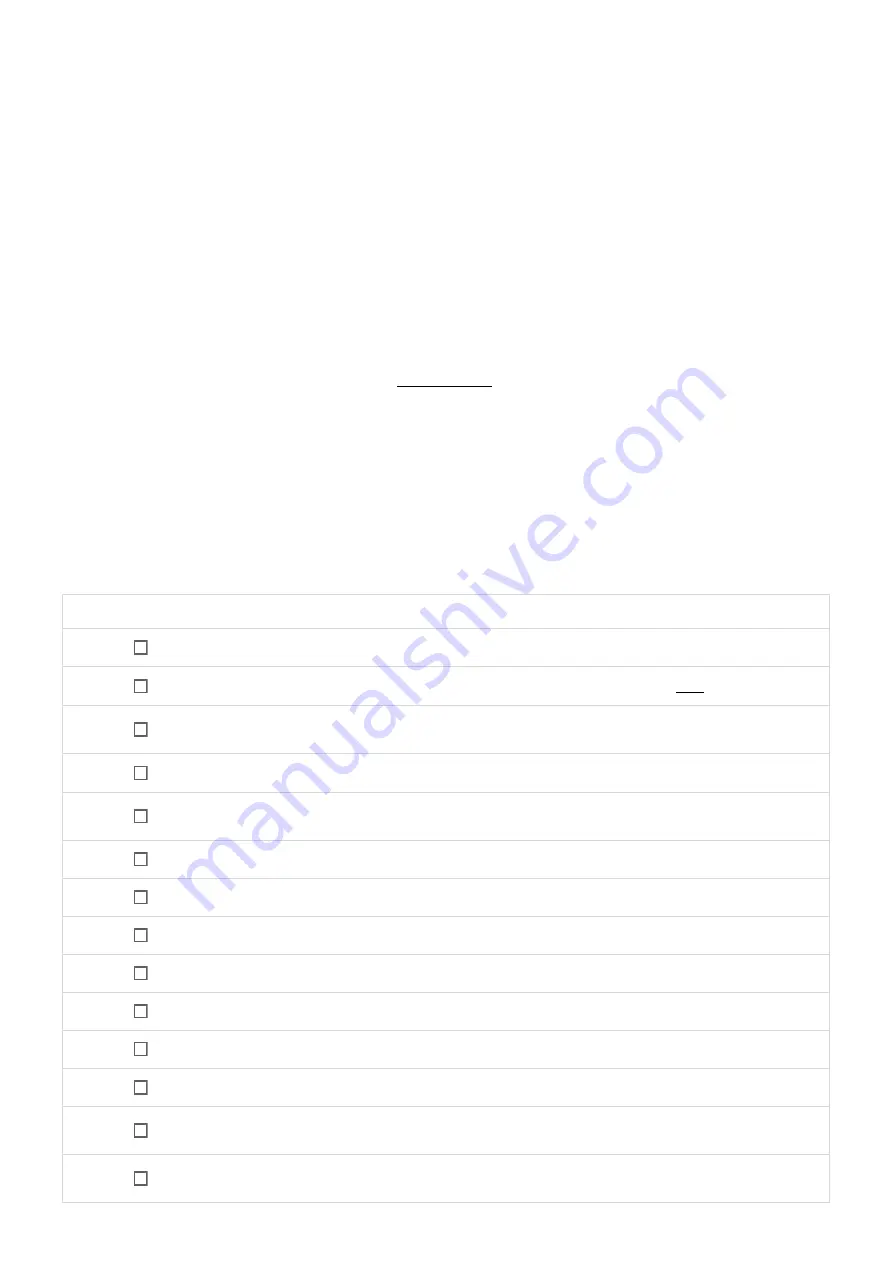
61
88 CCO
OLLLLEEGGAAM
MEENNTTII EELLEETTTTRRIICCII
There are three methods for connecting the thermostat cable and it depends on the application.
NNoottee
When ROOM THERMOSTAT is set , the indoor temperature sensor Ta can
’
t be set to valid, unit running
only according to T1.
M
Meetthhoodd CC
Hydraulic module is connected with two external temperature..
•
On-Off zone 1 from input H - L1
•
On-Off zone 1 from input C - L1
•
Heat-Cool from user interface
User interface setting:
For service man > 6. Room thermostat >
6.1 Room thermostat to Double zone
NNoottee
The wiring of the thermostat should correspond to the settings of the user interface.
See chapter START-UP AND CONFIGURATION - ROOM THERMOSTAT.
Power supply of machine and room thermostat must be connected to the same Neutral Line and (L2)
Phase Line(for 3-phase unit only).
RRoooom
m tthheerrm
moossttaatt -- NNoott ssuupppplliieedd
M
Meetthhoodd BB
•
On-Off from input H - L1
•
Heat-Cool from user interface
User interface setting:
For service man > 6. Room thermostat >
6.1 Room thermostat to One zone
M
Meetthhoodd AA
•
On-Off + Heat from input H - L1
•
On-Off + Cool from input C - L1
User interface setting:
For service man > 6. Room thermostat >
6.1 Room thermostat to Mode set
CCNN1111
CCNN1111
CCNN1111
99 M
MEESSSSAA IINN FFU
UNNZZIIO
ONNEE
GGeenneerraall
The indicated operations should be done by F.GAS qualified technician with specific training on the product.
Upon request, the service centres performing the start-up.
The electrical, water connections and the other system works are by the installer.
Agree upon in advance the star-up data with the service centre.
Before checking, please verify the following:
•
the unit should be installed properly and in conformity with this manual
•
the electrical power supply line should be isolated at the beginning
•
the unit isolator is open, locked and equipped with the suitable warning
•
make sure no tension is present
W
WAARRNNIINNGG
After turning off the power, wait at least 5 minutes before accessing to the electrical panel or any other
electrical component.
Before accessing check with a multimeter that there are no residual stresses.
PPrreelliim
miinnaarryy cchheecckkss
The following check list is a brief reminder of the points to check and of the operations to perform to start
-up the unit.
For details on the points mentioned in the check list refer to various chapters of the manual.
√
Preliminary checks
1
Are the functional spaces of the internal unit and the external unit being observed ?
2
Is the section of the cooling lines correct ? Have the supplied sealing couplings been used ?
3
Does the equivalent length of the refrigerant piping exceed 3 or
≤
30m?
4
Is the height different of the refrigerant piping below 25m?
5
Have emptying and additional load been carried out ? Was there a visual check for oil / leaks ?
6
Water features are suitable? The hydraulic system has been cleaned?
7
Is the water filter from the waterworks inlet correctly installed ?
8
Is the system filter on the supply correctly installed?
9
Are the inlet and outlet of the water lines correct ?
10
Is there a non-return valve on the DHW recirculation line?
11
Present safety valve on the DHW side?
12
Present expansion vessel on the DHW side?
13
Has the compressor support bracket been removed?
14
Does the system contain the minimum required amount of water?
StaRt - up
10. START - UP