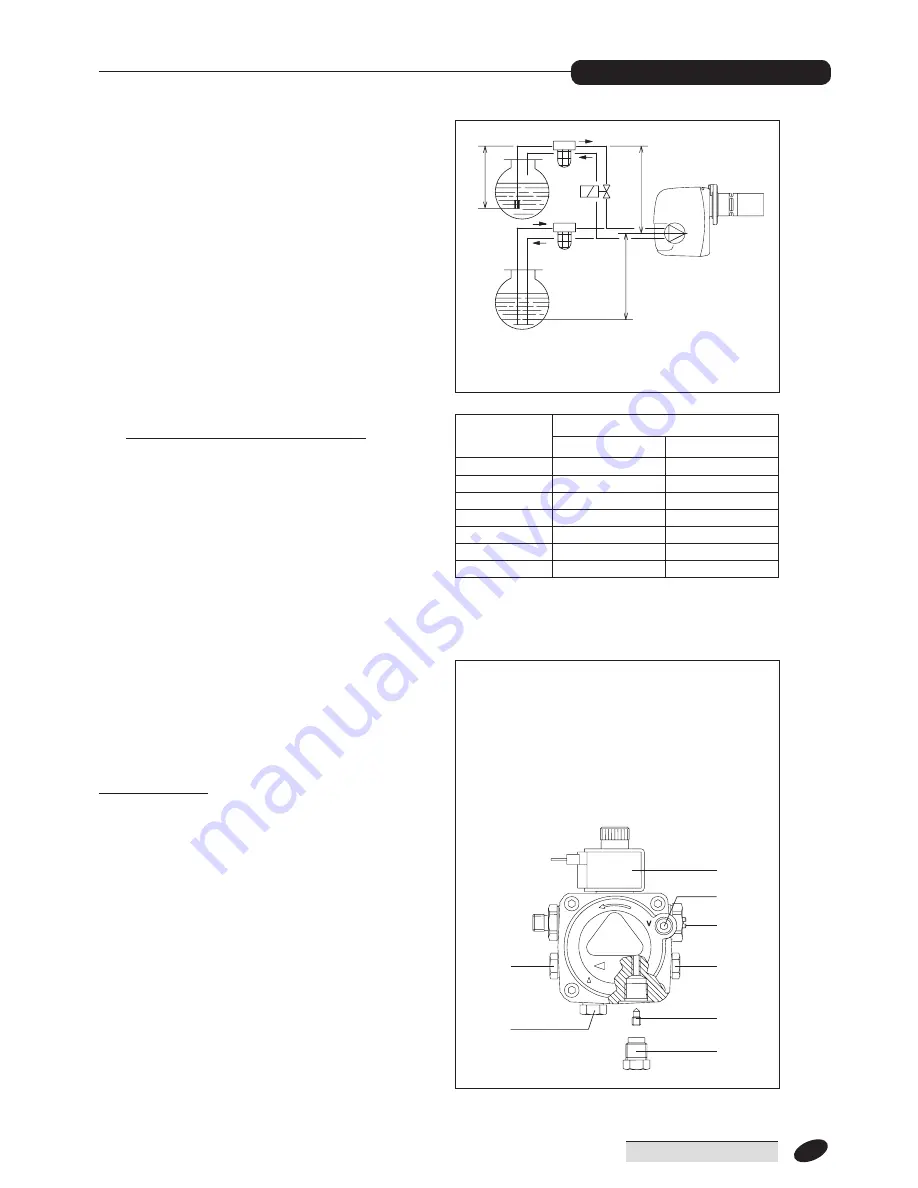
INSTALLER
29
(*)
ma
x.
4
m
H
H
(*) Automatic shut-off device (only where required).
See the wiring diagram on page 14 for details of
the electrical connections.
H
(m)
L
(m)
Øi
(8 mm)
Øi
(10 mm)
0
35
100
0,5
30
100
1
25
100
1,5
20
90
2
15
70
3
8
30
3,5
6
20
r
INSIEME CONDENS
boilers have their fuel connec-
tions at the rear.
Fuel supply hoses must pass through the gap between
the boiler base and the floor before being connected to
the fuel pump.
If the oil feed system is in negative pressure, the return
line must reach the same height as the suction line. This
avoids having to install a bottom valve, which would be
essential if the return hose were to reach above the level
of the fuel.
b
The installer must ensure that negative pressure in
the oil feed never exceeds 0.4 bar (30 cm Hg).
If this value is exceeded, the fuel oil will release gas.
Make sure that the oil hoses are perfectly oil-tight.
b
Clean out the oil tank at suitable intervals.
b
The oil feed line must be suitable for the flow rate
demanded by the burner. The oil feed system must
also be equipped with all the necessary safety and
control devices required by applicable legislation
and standards.
Refer to the table alongside for oil feed line charac-
teristics.
b
A filter must be installed in the oil feed line.
b
Make sure that the oil return line is not kinked or
blocked before starting up the boiler. Excessive
back-pressure can lead to breakage of the pump
seal.
Priming the pump
To prime the oil pump simply start up the burner and
check for a flame.
If the burner enters lockout before any fuel reaches it,
wait at least 20 seconds then press the remote burner
reset button on the control panel and repeat the ignition
procedure until the flame lights.
FuEl CONNECTIONS
H
= Head
L
= Maximum length of suction hose
Øi
= Internal diameter of hose
7
6
5
4
3
2
8
1
1 - Suction port
2 - Return port
3 - By-pass screw
4 - Pressure gauge fitting
5 - Pressure regulator
6 - Vacuum gauge fitting
7 - Valve
8 - Auxiliary pressure measurement fitting