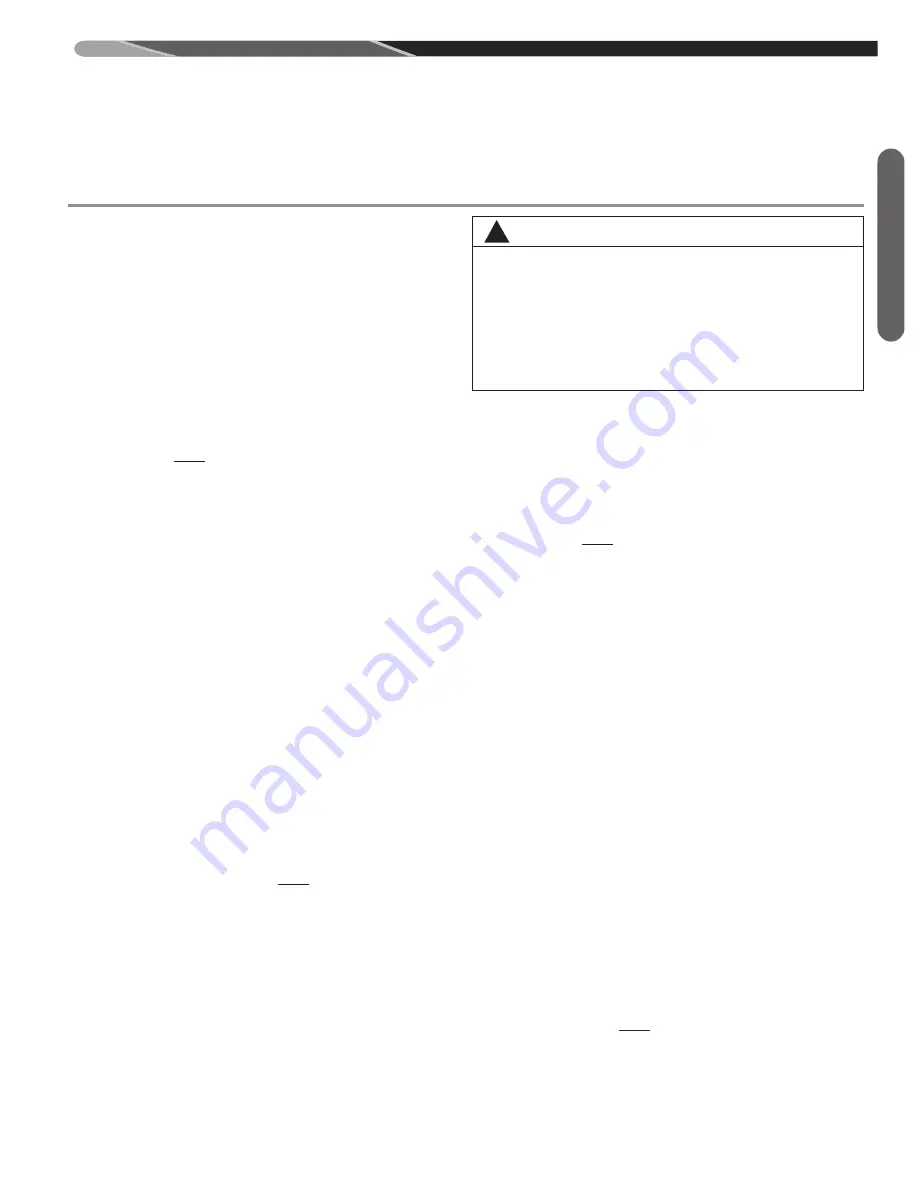
75
SETTING GAS PRESSURE
The maximum gas supply pressure to the furnace
must not exceed 10.5" w.c. natural gas, or 13" w.c. LP
gas.
The minimum supply gas pressure to the gas valve
should be 5 w.c. natural gas or 11 w.c. LP gas. A properly
calibrated manometer is required for accurate gas pres-
sure measurements.
SUPPLY GAS PRESSURE
MEASUREMENT
An inlet pressure tap is on the input side of the gas valve.
1. With gas shut off to the furnace at the manual gas
valve outside the unit.
2. Loosen (do NOT remove) the inlet pressure tap using
a 3/32 allen-head wrench (see Figure 37).
3. Connect a manometer to the pressure tap. The pres-
sure tap requires a 5/16 I.D. hose.
A kit is available from Prostock Replacement Parts
which includes the following:
A. 3/32 allen-head wrench
B. 5/16 to 1/4 I.D. hose reducer fitting
C. Short piece of 5/16 I.D. hose
Kit part number is: F0092-100300S1
4. Turn on the gas supply and operate the furnace and
all other gas-fired units on the same gas line as the
furnace.
5. Note or adjust the line gas pressure to give:
A. 5 - 10.5 w.c. for natural gas.
B. 11 - 13 w.c. for LP gas.
6. Shut off the gas at the manual gas valve and remove
the manometer and hose.
7. Tighten the allen-head screw in the inlet pressure tap
using a 3/32 allen-head wrench (see Figure 37) and
replace the pressure tap plug before turning on the
gas.
8. Turn on the gas supply and check for leaks using an
approved leak detector. Do NOT use a flame of any
kind to check for leaks. Repair any leaks and repeat.
If the supply gas line pressure is above these ranges, in-
stall an in-line gas regulator to the furnace for natural gas
units. With LP gas, have the LP supplier reduce the line
pressure at the regulator.
If supply gas line pressure is below these ranges, either
remove any restrictions in the gas supply piping or enlarge
the gas pipe. See Tables 12 and 13. With LP gas, have
the LP supplier adjust the line pressure at the regulator.
Manifold Gas Pressure Measurement. Natural gas
manifold pressure should be 3.5" w.c. for high fire and
1.8" w.c. for low fire. LP gas manifold pressure should
be 10.0" w.c. for high fire and 4.9" w.c. for low fire.
Only small variations in gas pressure should be made by
adjusting the pressure regulator.
1. With the gas to the unit shut off at the manual gas
valve, remove the outlet pressure tap plug.
2. Loosen (do NOT remove) the outlet pressure tap plug
using a 3/32 allen-head wrench (see Figure 37).
3. Connect a manometer to the pressure tap. The pres-
sure tap requires a 5/16 I.D. hose.
A kit is available from Prostock Replacement Parts
which includes the following:
A. 3/32 allen-head wrench
B. 5/16 to 1/4 I.D. hose reducer fitting
C. Short piece of 5/16 I.D. hose
Kit part number is: F0092-100300S1
4. Turn on the gas supply and operate the furnace (apply
a heat call).
5. Note or adjust the manifold gas pressure to give:
A. 3.5 w.c. for natural gas.
B. 10.0 w.c. for LP gas.
6. To adjust the pressure regulators, remove the regula-
tor caps. (See Figure 37.)
7. Turn the adjustment screw clockwise to increase pres-
sure, or counterclockwise to decrease pressure.
8. Securely replace the regulator caps.
9. Shut off gas at the manual gas valve and remove the
manometer and hose.
10. Tighten the allen-head screw in the inlet pressure tap
using a 3/32 allen-head wrench (see Figure 37).
11. Turn on the gas supply and apply a heat call to the fur-
nace. Then check for gas leaks using an approved
leak detector. Do NOT use a flame of any kind to
check for leaks. Repair any leaks and repeat.
GAS PRESSURE
GAS PRESSURE
Ga
s P
res
su
re
!
CAUTION
ELEVATIONS ABOVE 2000 FT. REQUIRE THAT THE
FURNACE INPUT RATING BE ADJUSTED AND THAT
THE SIZE OF THE BURNER ORIFICES BE RECAL-
CULATED BASED ON ELEVATION AND GAS HEAT-
ING VALUE. THE BURNER ORIFICES MAY (OR MAY
NOT) NEED TO BE CHANGED. SEE THE SECTION
TITLED “HIGH ALTITUDE INSTALLATIONS” OF THIS
BOOK FOR INSTRUCTIONS.
Summary of Contents for 96MDV Series
Page 34: ...Field Conversions 34...
Page 35: ...Field Conversions 35...
Page 36: ...36 Field Conversions...
Page 37: ...37 Field Conversions...
Page 38: ...Field Conversions 38...
Page 115: ...115 TABLE 20 continued R96V FAULT CODES WITH DESCRIPTIONS AND SOLUTIONS Diagnostics...
Page 120: ...120 Diagnostics TABLE 20 continued R96V FAULT CODES WITH DESCRIPTIONS AND SOLUTIONS...
Page 126: ...126 FIGURE 65 2 STAGE ECM FURNACE WIRING DIAGRAM Troubleshooting...
Page 127: ...127...
Page 128: ...128 CM 1015...