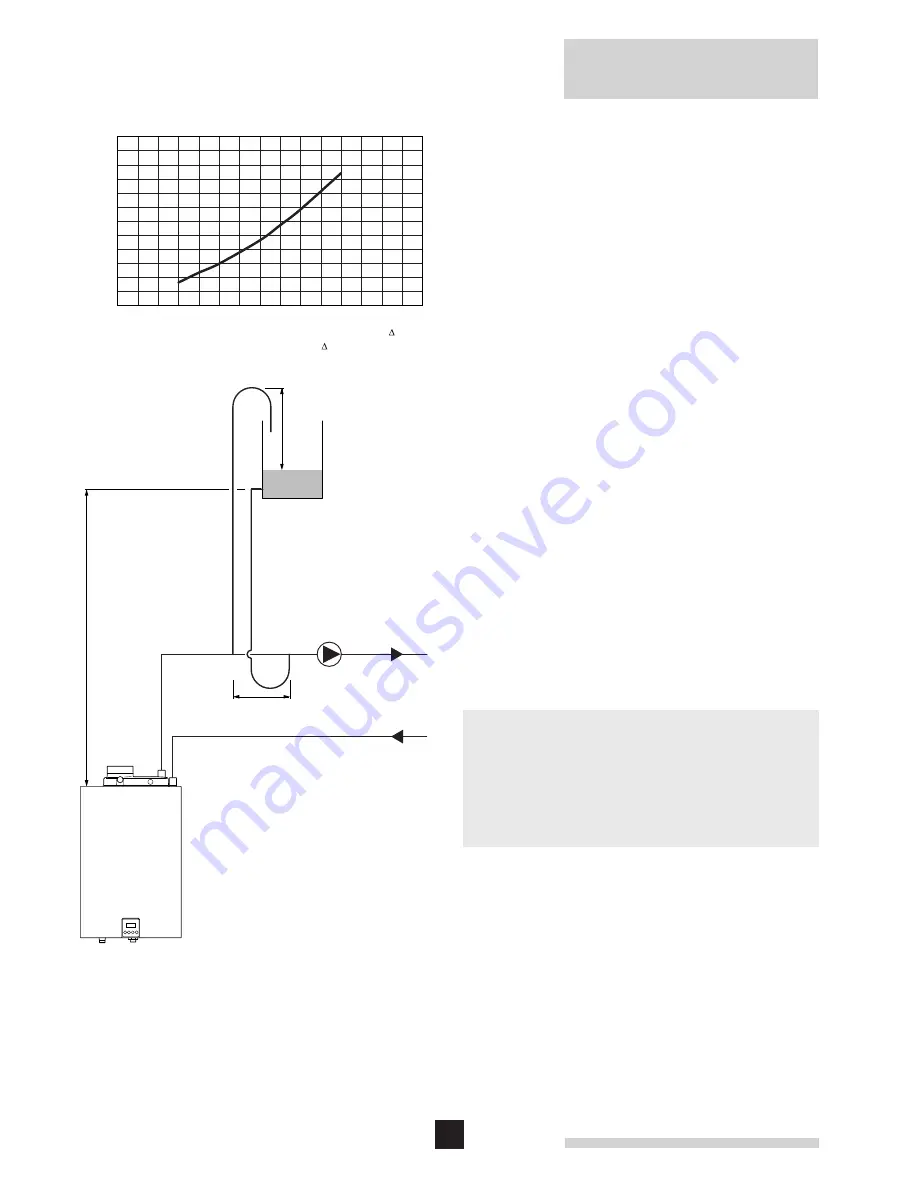
10
Remeha Avanta 18v
Pressure Loss Graph
P
re
ss
ur
e
Lo
ss
[m
ba
r]
Waterflow [m
3
/h]
100
200
300
400
500
600
700
0.5 0.6 0.7 0.8 0.9 1 1.1 1.2 1.3 1.4 1.5 1.6 1.7 1.8 1.9 2
59970LTGBW7H003a
Recommended T 11
o
C
T max. 20
o
C
Feed and
exansion
cistern
Flow
Return
Max. 150 mm
Cold feed
Min. 15 mm
Heating vent
Min. 22 mm
Min. 450 mm
Static head
Min. 1 m
59970LTGBW7H004b
2.3.3 Pressure loss of the boiler
2.3.4 Open-Vented System
The feed and expansion tank must be situated at a minimum
height of 1 metre and a maximum height of 30 metres above
the boiler to provide the correct operating head pressure.
The cold feed must be at least 15 mm and the open vent must
be at least 22 mm. The pipes must rise continuously from the
system. The heating vent must be at least 450 mm above the
water level in the feed and expansion cistern.
The pump should be fitted on the flow pipe from the boiler and
have isolating valves each side.
2.3.5 Sealed systems
If the Avanta 18v is installed on a sealed system, an appro-
priately sized expansion vessel and a safety valve MUST be
installed close to the inlet side of the pump. A mains filling
loop MUST be installed close to the outlet side of the system
pump, along with automatic air vents positioned in the system
pipe work to ensure adequate system venting during filling and
operation. An adequate pressure gauge should be fitted in a
position where it can be seen during filling of the system.
All in accordance with the current issue of the relevant British
Standards.
2.3.6 Additional guidelines for the domestic and CH
water
•
Power flush the pipes and radiators thoroughly before con-
necting the boiler to the central heating system in accord-
ance with BS 7593 (1992).
•
Following power flush, re-fill the system with clean tap water
and run the system up to 60°C – turn boiler off and allow
to cool slightly, then completely drain system from all low
points. Re-fill system.
•
The temperature of the central heating pipes and the
radiators can rise to 95°C.
•
Use untreated tap water only to fill the CH system.
•
The pH value of the system water must be between 6 and 9.
•
In case inhibitors are being used, please follow the
instructions given in,
see par. 2.3.7.
59970.LT.GB.W7H.003
59970.LT.GB.W7H.004