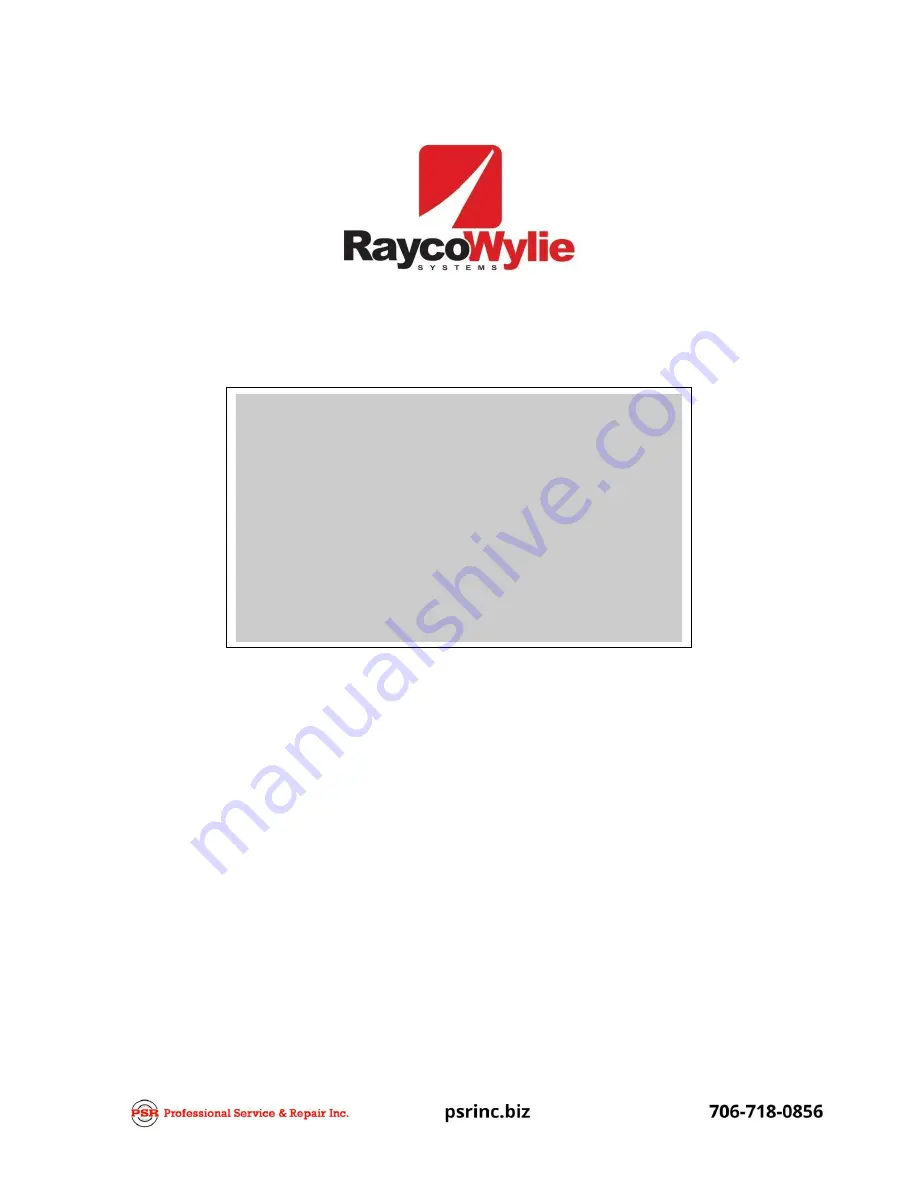
55M4300CCE00 Rev A
Calibration Instructions
i4300 Rated Capacity Limiter/Indicator
for
telescopic cranes, pressure sensing
software ref sc162xxx
Crane safety instrumentation
Copyright 2017
(Rayco-Wylie Systems).
All rights reserved.
Any part of this document may not be reproduced or transmitted in any form or by any means including
photocopy or any other information storage and retrieval system without the permission from
RaycoWylie Systems which will not normally be withheld assuming that the material is for internal use
only.
Summary of Contents for i4300
Page 2: ...55M4300CCE00 Rev A ...