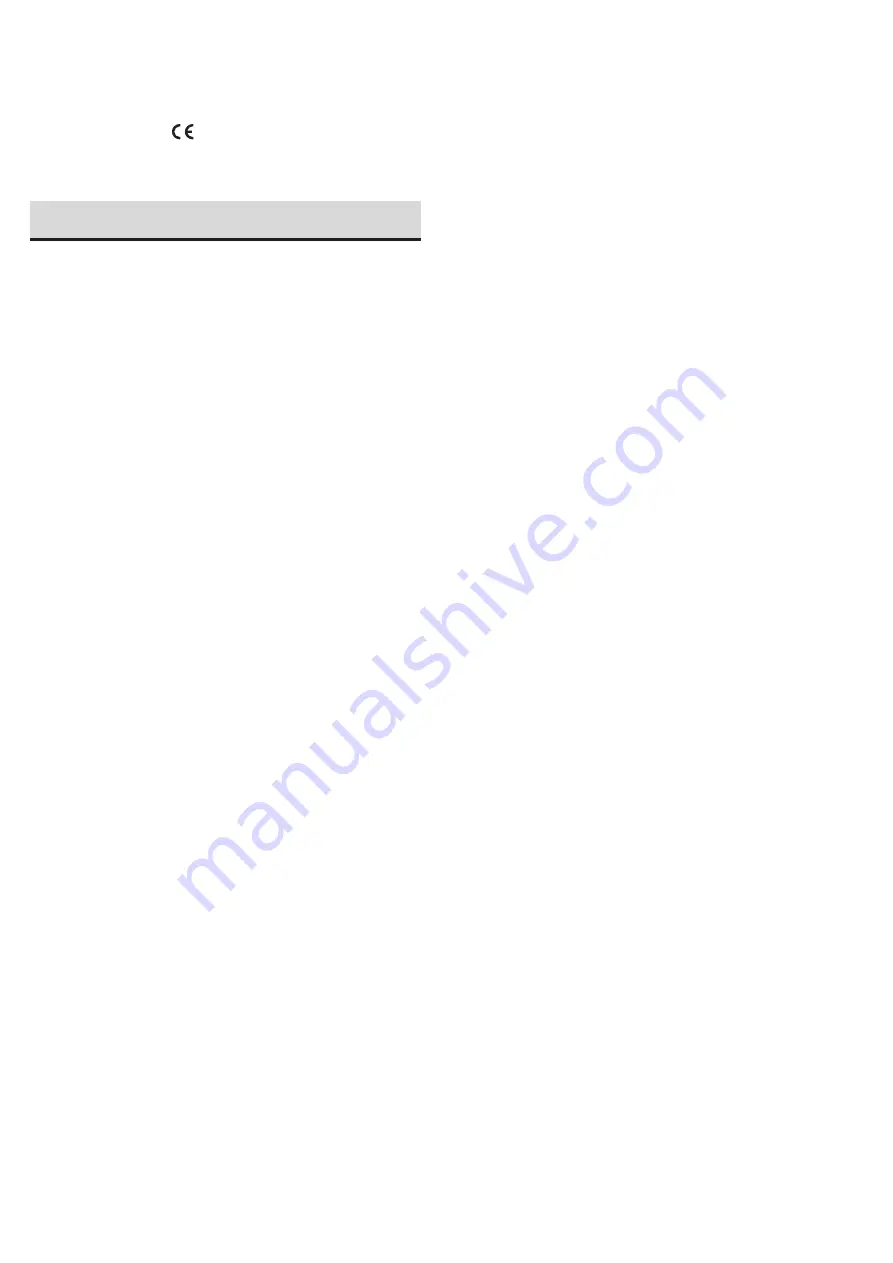
- 18 -
Any duplication of this instruction manual, whether in full or in part, is prohibited without written approval from Grégoire-Besson, regardless of the country, format or medium.
9901.00.34DE00; 02.2017
Subject to technical modifications
T
ABLE
OF
CONTENTS
S
UPER
A
LBATROS
140 MW; S
ERIES
2
9.7 Maximum permissible dimensions and weights
for transport by road ........................................ 41
9.8 Explanation of the type designation ................ 42
9.9 Type
plate, mark ....................................... 42
10 Loading ............................................................ 42
OPERATION ............................................ 43
11 Preparing the tractor ...................................... 43
11.1 Checking requirements for the tractor ............. 43
11.2 Checking the tractor’s air pressure ................. 43
11.3 Checking the track width ................................. 43
11.4 Ballast weight
.................................................. 43
12 Coupling the implement ................................. 44
12.1 Notes on coupling ........................................... 44
12.2
Bottom link connection .................................... 44
12.2.1. Connection
categories
..............................44
12.2.2.
Ball bush and guide cone for bottom link
bolt ............................................................44
12.3 Couple the bottom links ................................... 45
12.4 Couple the top link .......................................... 45
12.5 Couple the top link .......................................... 46
12.6 Connect the hydraulic lines ............................. 46
12.6.1.
Required hydraulic connections ...............47
12.6.2.
Connect the hydraulic lines ......................47
12.7 Connecting the lighting cable .......................... 47
13 Sliding in and folding up the parking support .
48
14 Carrying out the turning test ......................... 49
15 Adjusting the working width .......................... 50
16 Adjusting the track of the contact or combina-
tion wheel ........................................................ 51
17 Preparing the machine, pre-adjustments .... 53
17.1 Information on the model ................................ 53
17.2 Required preparations
..................................... 53
17.3 General adjustment instructions ...................... 53
17.4 Pre-adjusting the traction point ...................... 54
17.4.1. Adjustment
instructions
............................54
17.4.2.
Ploughs with turnbuckle ...........................54
17.4.3.
Ploughs with hydraulic frame slewing .......55
17.5
$GMXVWLQJWKH¿UVWERG\ZRUNLQJZLGWK
............. 56
17.5.1.
Adjusting the ploughs with adjusting spindle
56
17.5.2.
Adjusting the ploughs with hydraulic cylin-
ders ...........................................................56
18 Moving the plough into the transport
position ............................................................ 57
18.1
Turning the plough onto the right-hand side ... 57
18.2
Turn the ploughs with combination wheel into the
transport position ............................................. 57
18.2.1.
Turning the combination wheel into
the transport position ................................58
18.2.2.
Locking the central lock ............................59
18.2.3.
Turning the plough into the transport position
59
18.2.4.
Uncoupling the top link .............................59
18.3
Lifting the ploughs with depth guide wheel into
the transport position ....................................... 60
19 Travelling by road ........................................... 60
19.1
Preparations for travelling by road .................. 60
19.2 Driving instructions
.......................................... 60
19.3 Check before moving off ................................ 61
20 Moving the plough from the transport position
to the working position .................................. 61
20.1 Removing the lighting ...................................... 61
20.2
Turn the plough with combination wheel into the
working position .............................................. 62
20.2.1.
Coupling the top link .................................62
20.2.2.
Unlocking the central lock .........................62
20.2.3.
Turning the plough onto the right-hand
side ...........................................................62
20.2.4.
Turning the combination wheel into the
working position ........................................63
20.3
Lowering the plough with depth control wheel
into the working position .................................. 64
20.4 Moving the subsoiler into the working position 64
21 Working information ....................................... 65
21.1 Safety during operation ................................... 65
21.2
:RUNLQJYDOXHV:RUNLQJVSHHGZRUNLQJ
depth ............................................................... 65
21.3 Working information ........................................ 66
21.4
Driving instructions - turning on headlands ..... 66
21.5 Operational safety on a hillside ....................... 66
22 Adjustments after ploughing ......................... 67
22.1 Adjusting the working depth ............................ 67
22.1.1. Adjustment
instructions
............................67
22.1.2. Preparation
...............................................67
22.1.3.
Depth adjustment, depth control wheel
PS 5 ..........................................................67
22.1.4.
Depth adjustment, depth control wheel
PS 30 and combination wheel D 30 .........67
22.1.5.
Depth adjustment, RJR wheel ..................68
22.2 Aligning the plough parallel to the ground ....... 68
22.3 Adjusting the incline ........................................ 69