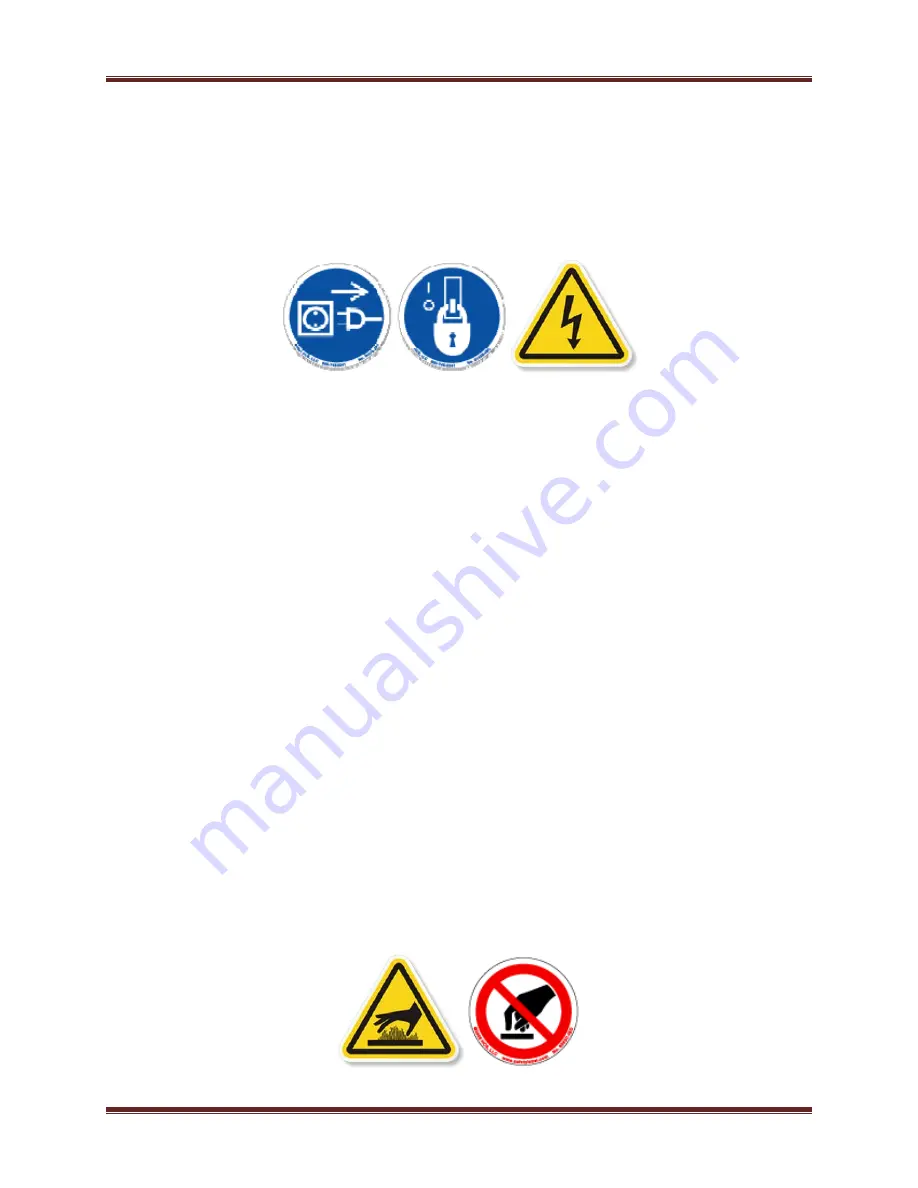
MPS6100 MAINTENANCE MANUAL
ORIGINAL INSTRUCTIONS
Page 8
3.0
GENERAL PROCEDURES
3.1
DE-ENERGIZING AND LOCKOUT PROCEDURE
CAUTION: Risk of electrical shock if the machine has not been properly de-energized and
locked out prior to performing maintenance procedures.
1)
First the machine must be powered off. It is recommended to use the cool down cycle
to avoid any possible heat damage to components. The machine can also be shut down
immediately by pressing the “Power Off” icon.
2)
Proceed to unplug the main power cord from the wall outlet or the back of the control
box. To lockout the machine the main power cord must be COMPLETELY
REMOVED and in the possession of the service technician at all times.
3.2
HEATING BAR COOLING TIME
The heating bars of the MPS6100 operate between 120°C and 200°C (250-400°F)
which can cause serious burns if touched by the service technician. Table 2 below shows
average cooling times from the maximum temperature of 200°C over a time lapse of ten
minutes. Using the cool down cycle will ensure the heating bars are below the set cool down
temperature (usually around 60°C). At this point the machine will automatically shut down
and be ready for maintenance. When servicing the machine be aware of the possible dangers
posed by the temperature of the sealing bars.
CAUTION: Hot surfaces may be exposed. To prevent personal injury do not attempt to
touch the heating bars or surrounding areas while hot.
Summary of Contents for MPS6100
Page 6: ...MPS6100 ORIGINAL Page vi ISO SAFETY SYMBOLS LOCATION...
Page 7: ...MPS6100 OPERATION MANUAL ORIGINAL Page x MPS6100 OPERATION MANUAL...
Page 27: ...MPS6100 MAINTENANCE MANUAL ORIGINAL Page xii MPS6100 MAINTENANCE MANUAL...
Page 55: ......
Page 56: ......
Page 57: ......
Page 58: ......