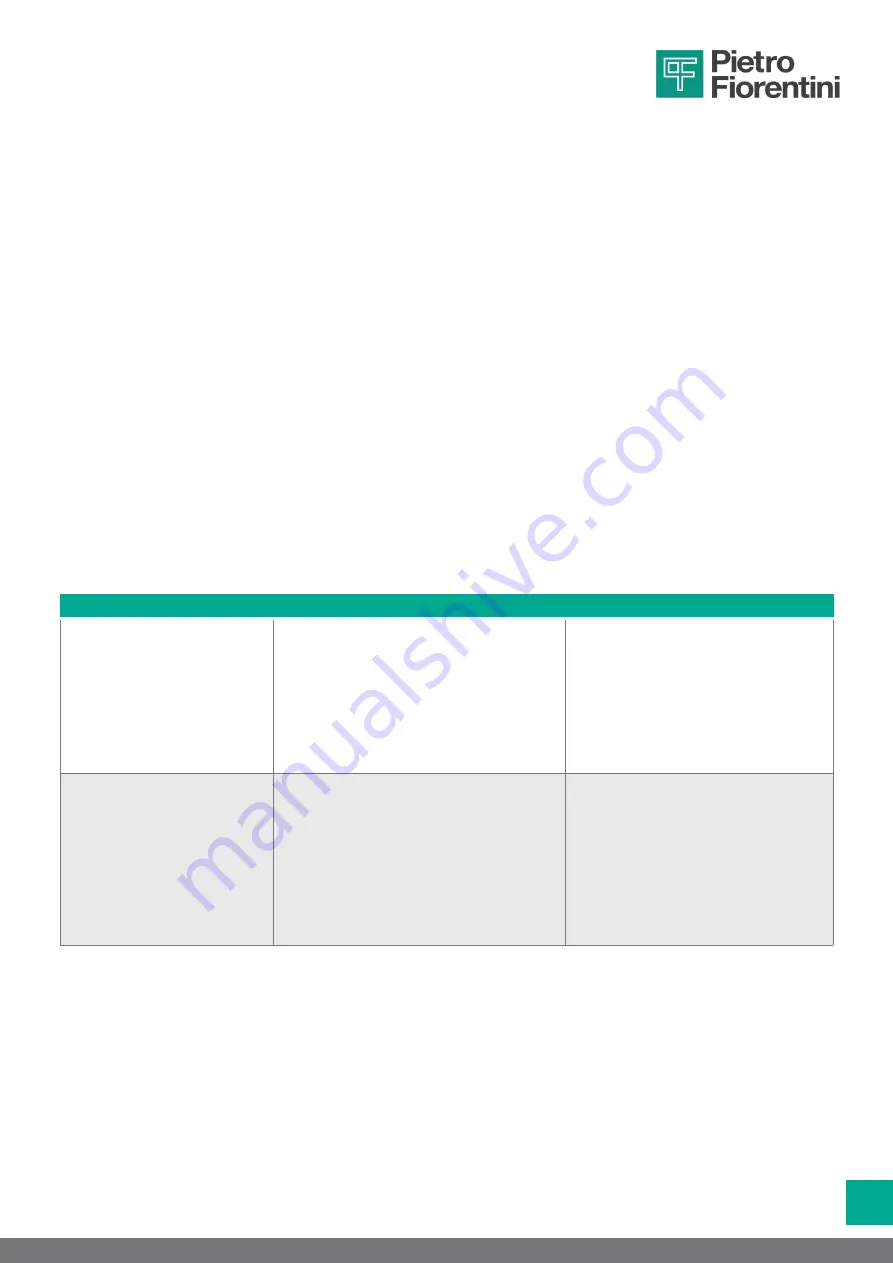
35
ASX 176
Use, maintenance and warning instructions
HIGH PRESSURE REGULATOR
|
DESCRIPTION AND OPERATION
|
REV. 00
EN
In depressurised conditions, the regulator plug (5) is kept in a shut-off position by the spring (8) and rests on the reinforced
gasket (6). The upstream pressure, although variable, does not change this position since the regulator plug (5) is fully
balanced.
The position of the regulator plug (5) is controlled by the main diaphragm (7) on which the following forces act:
• during shut-off: load of the spring (8) and thrust resulting from the downstream pressure (Pd) in the chamber (C);
• when opening: thrust generated by the loading pressure (Pm) supplied by the pilot (4) in the chamber (A).
When the regulator is installed in a vertical position, the weight of the mobile unit acts on the above mentioned forces
during both opening and shut-off.
The loading pressure (Pm) is obtained from the upstream piping of the regulator (1). The gas enters the pre-regulator (3),
passes through the filter (9) and its pressure is reduced to a fixed value of the pressure in the pre-regulator (Pep), which
depends on the regulator calibration pressure.
Pressure at the pre-regulator (Pep) enters the pilot (4) from the pre-regulator (3). The pilot (4) regulates the value of the
loading pressure (Pm) to be supplied into the chamber (A) of the regulator in order to open the plug (5) of the regulator
through the opening of the plug (14).
The loading pressure (Pm) is set by comparing:
• the force exerted by the pilot calibration spring (11);
• the action of the downstream pressure (Pd), which acts on the diaphragm (12) in the chamber (B).
The loading circuit is an open circuit with continuous discharge by means of a transfer hole (16) in the diaphragm protec-
tion disc with discharge to the downstream pressure in the chamber (C).
Under normal operating conditions, the plug (14) of the pilot is positioned so that the value of the motorised pressure (Pm)
is such that the value of the downstream pressure (Pd) remains around the calibration value.
Operating conditions
Operating consequences
Concluding outcome
Decrease in downstream
pressure (Pd) for:
• increase in the request-
ed flow rate;
• or drop in upstream
pressure (Pu).
Imbalance in the mobile unit (13) of the
pilot (4), which causes the plug (14) of the
pilot (4) to open.
• Increase in loading pressure (Pm);
• Move the regulator plug (5) dur-
ing opening until the downstream
pressure calibration value (Pd) is
restored.
Increased downstream
pressure (Pd) for:
• drop in the required flow
rate;
• or increased upstream
pressure (Pu).
The force exerted by the downstream pres-
sure (Pd) on the pilot diaphragm moves the
mobile unit (13) and shifts the plug (14) of
the pilot (4) to the shut-off position.
• Decrease in loading pressure (Pm);
• Move the regulator plug (5) dur-
ing shut-off until the downstream
pressure calibration value (Pd) is
restored.
Tab. 4.14.
Summary of Contents for ASX 176
Page 32: ...32 ASX 176 EN Use maintenance and warning instructions HIGH PRESSURE REGULATOR SAFETY REV 00 ...
Page 253: ...253 ASX 176 ...
Page 254: ......