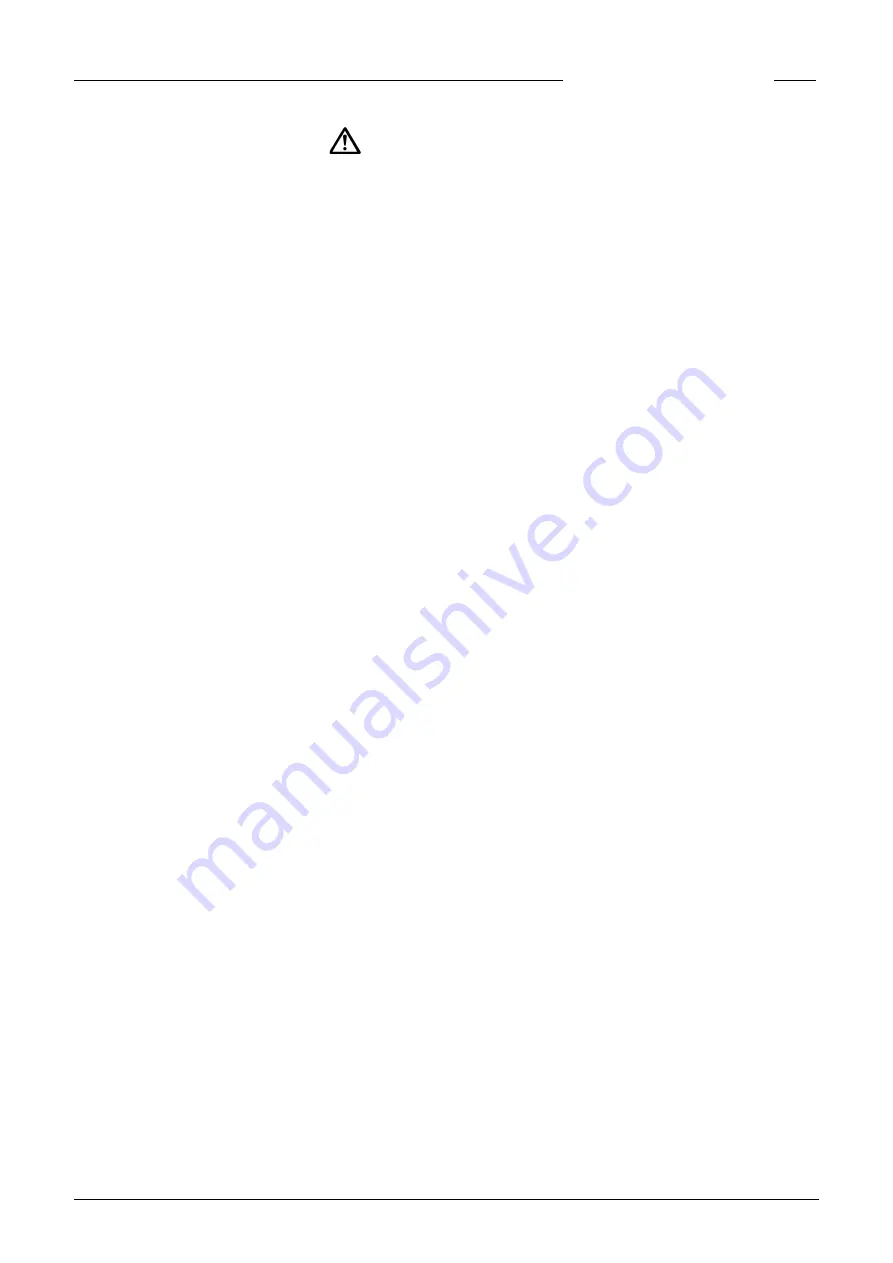
21
ENGLISH
used. The first system is used to detect
the base load; the air hose is connected
to the base load switch or to the static
pressure sensor module. The second
measurement system is used to detect
high water levels (when the pressure
sensor module is used as a redundant
system) and must be connected to the
high water switch. The redundant sys-
tem switches the pump(s) on in the
event of an error. The maximum per-
missible air hose length is 20 m.
It is important that the hose is laid at a
slight downward gradient from the con-
trol unit to the chamber.
Air pressure bell sensors
The switch-on level is determined by
the installation heights of the air pres-
sure sensors in the collecting chamber.
Connect the blue hose to the upper
pressure sensor for peak load/alarm!
To prevent pockets of condensed mois-
ture settling in the hose, the entire
length of the hoses should be laid at
an uphill gradient, rising continuously
from the chamber to the control unit.
Water in the hose will cause the switch-
ing points to be displaced. Also, if the
hose is exposed to frost, the water could
freeze and cause the switching system
to break down!
The hoses may have a maximum length
of 20 m. Existing hoses must not be ex-
tended due to the danger of leaks, but
must be replaced with hoses in one
piece.
Connect the static pressure system for
"base load" to B1, and the "Alarm/peak
load" (blue hose) to B2 on the control.
Dry running
In systems in which there is an explo-
sion hazard, the pump must not be al-
lowed to run in dry conditions. Separate
dry running protection must therefore
be installed. A submersible switch
is connected to terminals 18/20 via a
safety barrier. The submersible switch
remains closed if there is a high wa-
ter level. If the water level sinks to the
height of the pump volute casing, the
submersible switch opens and both
pumps are switched off.
Rechargeable battery
The control unit can be fitted with a 9V
NI-MH rechargeable battery. This ena-
bles a high water alarm to be triggered
even if there is a power failure.
CAUTION!
Only use the 9V-NiMh battery supplied by
the manufacturer! If dry-cell batteries or
Lithium batteries are used there is a dan-
ger of explosion!
NOTICE!
Check the function of the bat-
tery pack at regular intervals! The ser-
vice life is about 5 to 10 years. Note the
insertion date on the battery pack and
after five years the battery pack should
be replaced as a precautionary measure.
Software update
The control unit has a programming
interface that allows new software ver-
sions to be installed. If a new software
version becomes available, the control
unit software can be updated on-site
by JUNG PUMPEN service personnel,
without dismantling the unit.
EMC
When used in connection with our
standard submersible pumps and ac-
cessories, and when installed correct-
ly and used for its intended purpose,
the control unit meets all protective
requirements of the EMC Directive
2014/30 EU and is suitable for domestic
and commercial use when connected
to the public power supply network. If
connected to an industrial power sup-
ply network within an industrial facility,
where the power supply is provided by
an in-house high-voltage transformer,
there may be insufficient immunity to
interference.
Summary of Contents for JUNG PUMPEN HIGHLOGO 1-00
Page 2: ...2...
Page 32: ...32 HighLogo 1 00 E...
Page 35: ...35 HighLogo 1 LCXS...
Page 36: ...36...
Page 38: ...38 HighLogo 2 00 2 910 1...
Page 39: ...39 HighLogo 2 00 2 910 2...
Page 40: ...40 HighLogo 2 LC 1...
Page 41: ...41 HighLogo 2 LC 2...
Page 42: ...42 HighLogo 2 LCXS 1...
Page 43: ...43 HighLogo 2 LCXS 2...
Page 47: ...47...
Page 58: ...4...
Page 59: ...5...
Page 60: ...6...
Page 61: ...7...
Page 62: ...8...
Page 63: ...9...