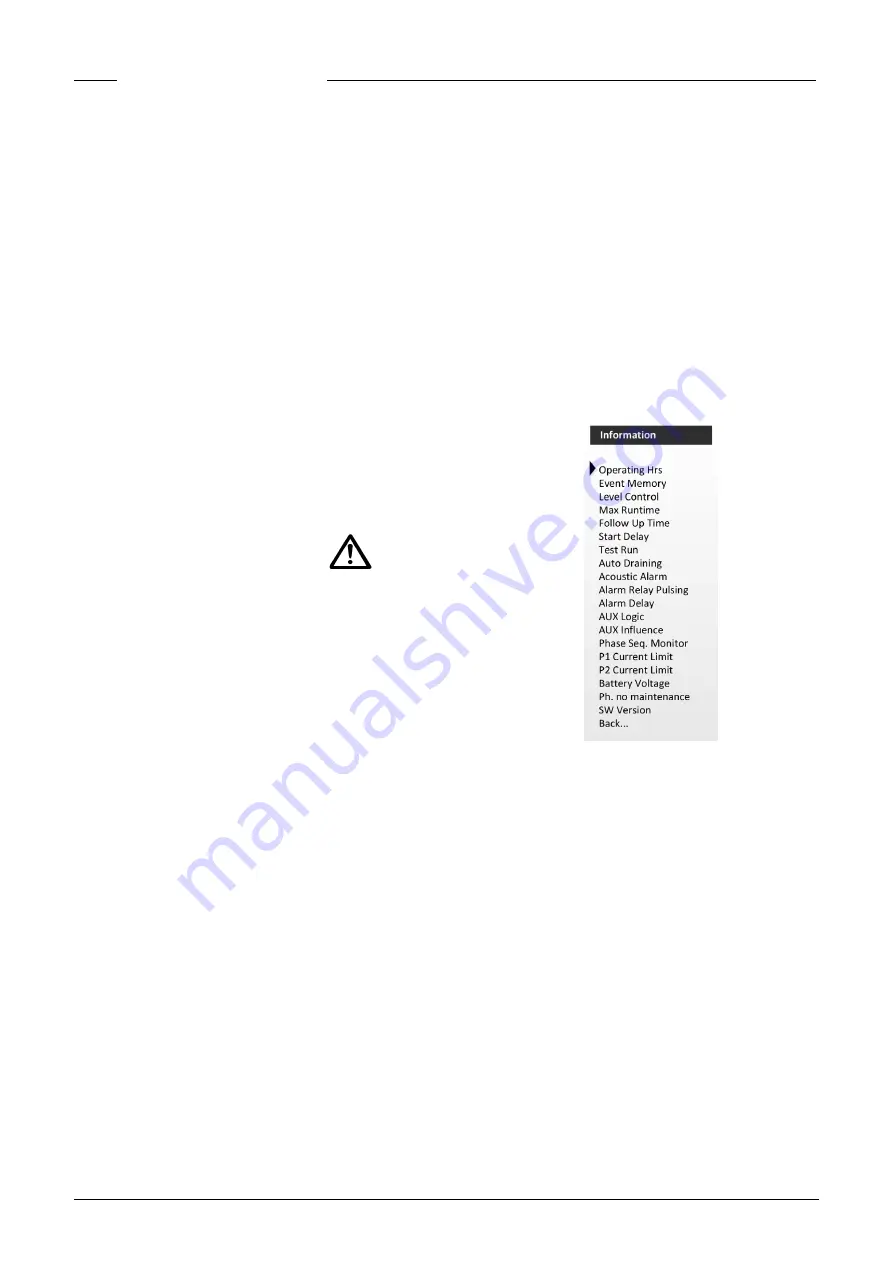
16
ENGLISH
control units, do not use the “Off” func-
tion: always disconnect the system from
the power supply by unscrewing the
pre-fuses or by switching off at a main
switch and taking measures to ensure
that the system cannot be switched
back on inadvertently.
Motor protection
The pump is monitored via a motor
protection switch (or a relay). If this is
activated, the control unit recognises a
motor protection error and triggers an
alarm. The pump is switched off at the
same time. The message is retentively
stored, even if there is no rechargeable
battery power. Once triggered, the mo-
tor protection must always be reset by
pressing the OK button before the pump
is restarted.
Thermal contacts
Thermal contacts are integrated in
the motor windings of the wastewater
pumps to safeguard the windings. If one
of the thermal contacts is triggered, the
control unit recognises a thermostat
fault and triggers an alarm. The pump
is switched off at the same time. The
message is retentively stored, even if
there is no rechargeable battery power.
Once triggered, the motor protection
must always be reset by pressing the
OK button before the pump is restarted.
Running time limit
Depending on its configuration, the
control unit monitors the running time
of the pump. If the preset maximum
running time of the pump is exceeded,
an alarm is triggered. If the maximum
running time is set to 0, this function is
disabled.
Faults / alarm
Faults are indicated via a red LED, an
integrated buzzer, a non-isolated alarm
relay, and a potential-free alarm relay.
The relay can be delayed by up to 999
seconds to suppress short alarms, such
as a brief high water alarm, and so pre-
vent unnecessary external intervention.
The fault text is shown in the display
and alternates with the standard dis-
play text. If more than one fault has oc-
curred, the relevant messages will be
scrolled through consecutively in the
display.
ATTENTION!
In the unlikely event that
an error cannot be reset via the oper-
ating panel, the system must be dis-
connected from the power supply and
restarted.
If a high water alarm is triggered fol-
lowing a power cut, this can only be
acknowledged by removing the “BRX”
jumper on the buzzer.
Before using for the first time, please
ensure that:
∙
When using the control unit, the re-
spective national laws, regulations,
local regulations and the rules of the
local energy utility are adhered to.
∙
The system is professionally secured.
∙
The level detection is properly in-
stalled and connected.
∙
The settings of the control unit cor-
respond to the measurement meth-
od used.
∙
The thermal contacts of the pumps
are properly connected
If the system is operated in an
explosion hazard chamber, the
relevant currently valid regula-
tions for the operation of systems in ex-
plosion hazard areas must be observed.
The sensor power circuits (level sensor,
float) must be intrinsically safe, for ex
-
ample with a suitable safety barrier.
In explosion hazard situations, open
measurement systems that use the
static air pressure system may only
be used in conjunction with pressure
switches that have been approved by
Jung Pumpen for this purpose.
In addition, the Ex mode (explosion
mode) must be activated in the system
settings menu, and dry running protec-
tion must be installed. The level contact
sensor can be connected with a safety
barrier, and connected to terminals
18/20.
Putting into operation for the first
time
Before using for the first time, some
basic parameters that are important for
operation will be polled.
- Select language
- Contrast setting
- Direction of rotation check Yes / No
- Level control (analogue value inputs
with 4-20mA signal / digital inputs /
Compli products)
- Choose a password. The standard
password should be replaced with a
personalised password
- Activating ATEX mode for zone 1
- Watchdog timer in ATEX mode to
prevent motor from overheating
- Restrict motor current for pump 1
and pump 2
After these settings, the control unit re-
verts to normal operation.
OPERATION
The standard display shows the operat-
ing mode of the control unit, the switch-
ing status, the motor current and the
level.
Information
∙
Operating hours
Displays the operating hours per pump
and the pump switching cycles
∙
Event memory
Displays the last events and faults for
the system
∙
Level detection
Displays the level control system that is
set
∙
Max. running time
Displays the running time limit that has
been set for the pumps (S2/S3 time)
∙
Follow-up time
Displays the follow-up time that has
been set for static pressure systems
∙
Start-up delay
Display the period of time that has been
set between supplying power supply
and being operational
∙
Daily test run
Displays whether the daily test run is
activated
Summary of Contents for JUNG PUMPEN HIGHLOGO 1-00
Page 2: ...2...
Page 32: ...32 HighLogo 1 00 E...
Page 35: ...35 HighLogo 1 LCXS...
Page 36: ...36...
Page 38: ...38 HighLogo 2 00 2 910 1...
Page 39: ...39 HighLogo 2 00 2 910 2...
Page 40: ...40 HighLogo 2 LC 1...
Page 41: ...41 HighLogo 2 LC 2...
Page 42: ...42 HighLogo 2 LCXS 1...
Page 43: ...43 HighLogo 2 LCXS 2...
Page 47: ...47...
Page 58: ...4...
Page 59: ...5...
Page 60: ...6...
Page 61: ...7...
Page 62: ...8...
Page 63: ...9...