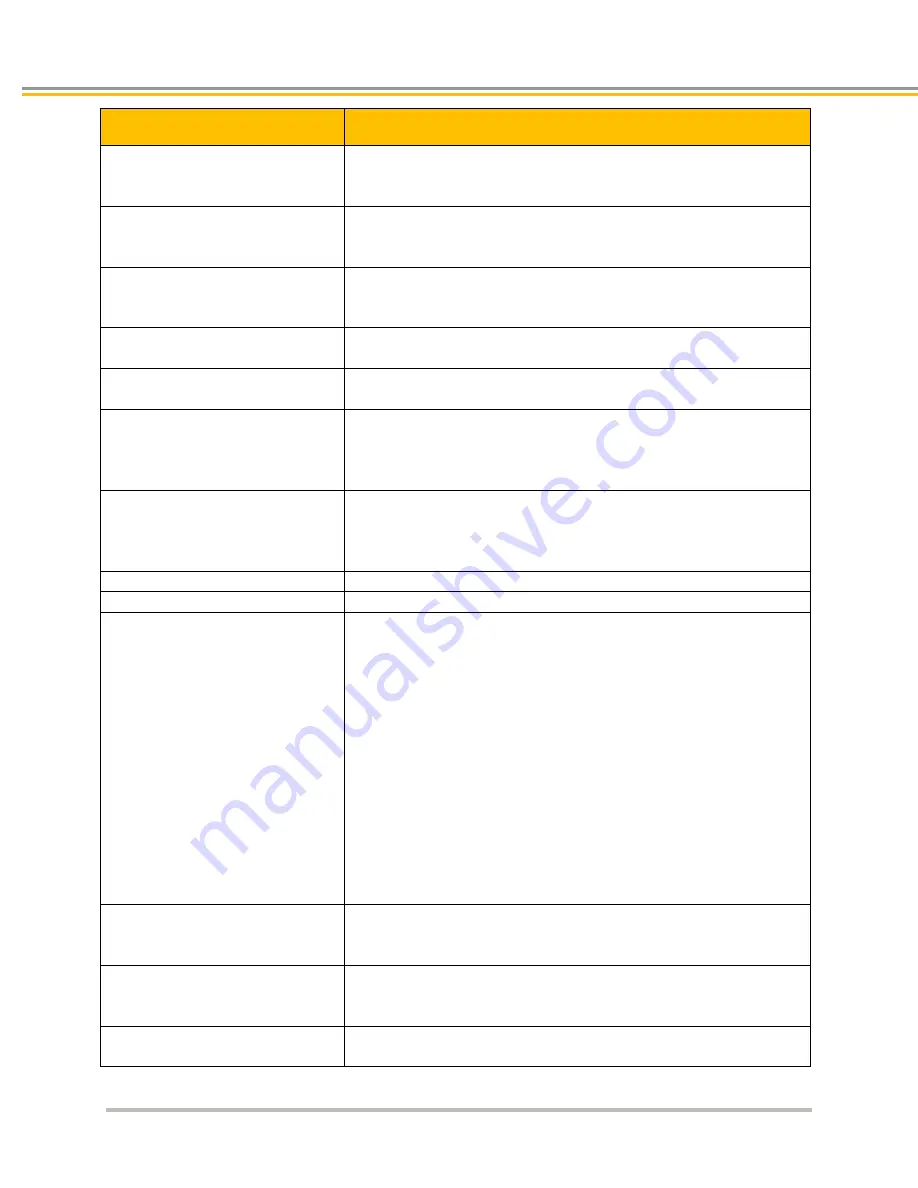
TROUBLESHOOTING
70
IPA Hardware Installation Guide
Error
Resolution
E8 Continuous Current = 0
This parameter is set to zero (0). To correct the error, you must set a
non-zero value. Refer to your motor specifications for the correct value.
(C1 Continuous Current)
E9 Peak Current = 0
This parameter is set to zero (0). To correct the error, you must set a
non-zero value. Refer to your motor specifications for the correct value.
(C3 Peak Current)
E10 Used Drive Continuous Current
Warning
The continuous current of the motor is higher than the continuous
current rating of the drive/controller. Use the continuous current rating
for the drive/controller.
E11 Torque Rating > Peak Power
Rating Warning
The motor’s torque rating is too high for the power level of the
drive/controller. Use the drive/controller’s torque rating.
E12 Used Drive Peak Current
Warning
The peak current of the motor is higher than the peak current rating of
the drive/controller. Use the drive/controller’s value for peak current.
E13 Inertia = 0
This parameter is set to zero (0). The drive/controller will not enable
Velocity or Position Modes. To correct the error, you must set to a non-
zero value. Refer to your motor specifications for the correct value. (C11
Motor Rotor Inertia / Forcer Mass)
E14 Damping = 0
This parameter is set to zero (0). The drive/controller will not enable
Velocity or Position Modes. To correct the error, you must set to a non-
zero value. Refer to your motor specifications for the correct value. (C10
Motor Damping)
E26 Drive Faulted
The drive/controller is faulted.
E27 Bridge Hardware Fault
Excessive current or short on the H-bridge.
E28 Bridge Temperature Fault
Excessive current being commanded:
1.
If the application is operating in the peak range, limiting the peak
current setting with DMTLIM can limit the current commanded
and lower the bridge temperature. Default DMTLIM is 3 x
continuous current, perhaps lowering it to 2.5 x continuous
current or 2 x continuous current can help. This, however, will
limit the motor’s available torque, which may increase position
error and possibly cause a position error fault.
2.
Issue a DIFOLD 1 command. This command enables the “current
foldback” feature in the drive. However, a drive in “foldback”
mode can available torque, which may increase position error
and possibly cause a position error fault.
3.
Use a larger IPA amplifier, which would be capable of higher
current outputs.
E29 Drive Over-Voltage
The bus voltage is too high (>410 VDC). Lower AC Mains voltage
(Motor Input Power) and check for excessive regeneration power. (S22
Transfer Bus Voltage)
E30 Drive Under-Voltage
The bus voltage is too low (<85 VDC) or there is overly aggressive
acceleration or deceleration. Raise AC Mains voltage (Motor Input
Power). (S22 Transfer Bus Voltage)
E31 Bridge Foldback
Drive/controller current was limited to prevent overheating (warning
only).
Summary of Contents for IPA Series
Page 2: ......
Page 14: ...INTRODUCTION 14 IPA Hardware Installation Guide CHAPTER 1 Introduction...
Page 18: ...MECHANICAL INSTALLATION 18 IPA Hardware Installation Guide CHAPTER 2 Mechanical Installation...
Page 24: ...ELECTRICAL INSTALLATION 24 IPA Hardware Installation Guide CHAPTER 3 Electrical Installation...
Page 54: ...TROUBLESHOOTING 54 IPA Hardware Installation Guide CHAPTER 4 Communications...
Page 63: ...TROUBLESHOOTING IPA Hardware Installation Guide 63 CHAPTER 5 Troubleshooting...
Page 77: ......
Page 100: ...REGULATORY COMPLIANCE UL AND CE 100 IPA Hardware Installation Guide...
Page 101: ......
Page 102: ...APPENDIX A 102 IPA Hardware Installation Guide APPENDIX A VM25 Expansion Module...
Page 114: ...APPENDIX C 114 IPA Hardware Installation Guide APPENDIX C IPA with Parker Mechanics...