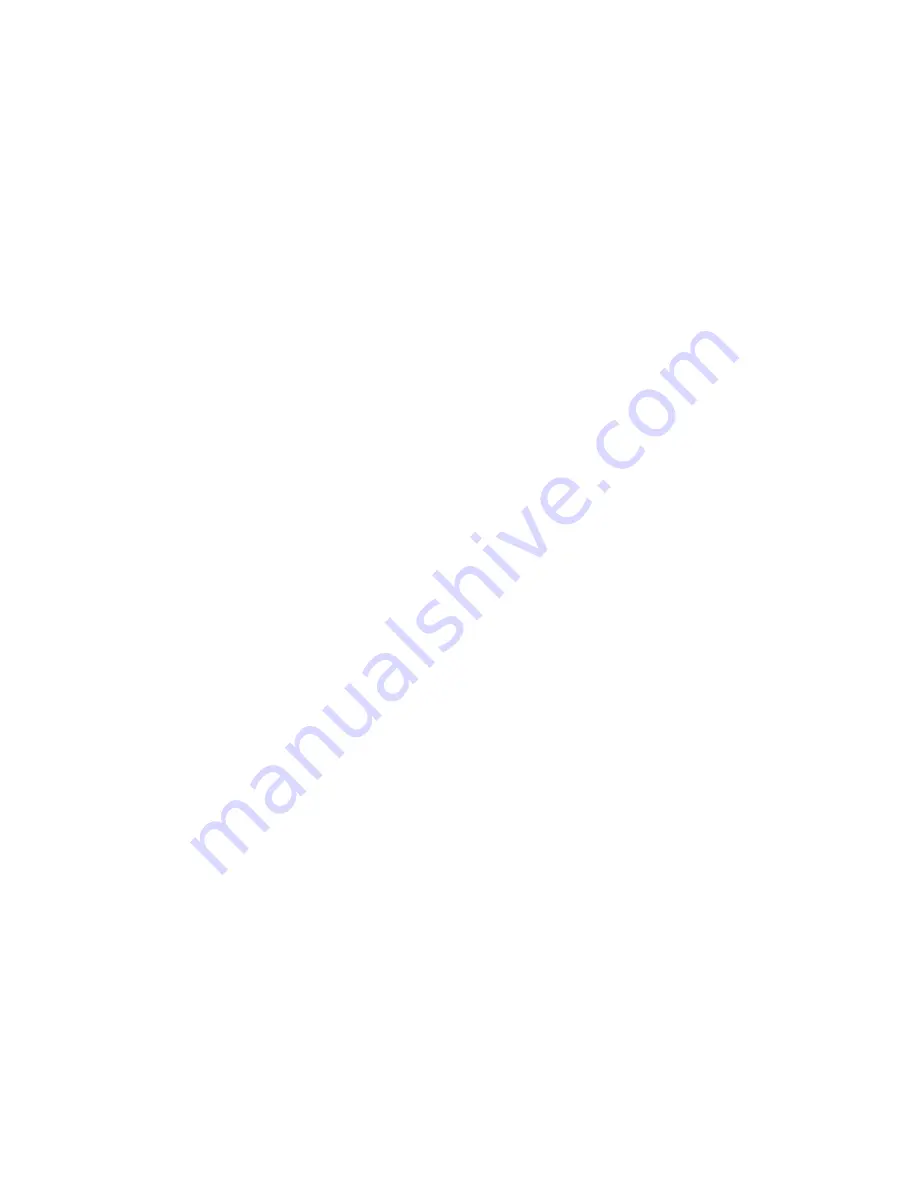
D-2
Programming
DC590+ Series DC Digital Drive
Making and Breaking Function Block Connections
Links can be changed, added or deleted from a block diagram whilst in the Configuration mode. There are 80 general-purpose links available, each has
its own identification number (“link” number). You make a link by setting the link’s “source” and “destination” tags to be the two parameter tag
numbers to be linked. The outputs of function blocks are not updated whilst in this mode.
NOTE
Links 1 to 50 are pre-connected between certain blocks and form the connections shown in the Default Block Diagram. Any of these links can
be re-used elsewhere in the block diagram.
The functions of the special links in previous software versions, (LINK 11 and LINK 12), are replaced by the ADVANCED 1 AND
ADVANCED 2 function blocks.
In previous software versions, certain links were single-ended "special links". This is no longer the case. All links can now be re-used
anywhere in the block diagram.
Programming Rules
The following rules apply when programming:
Operating Mode (CONFIGURE ENABLE = DISABLED)
•
Function block output parameter values cannot be changed (because they are a result of the function block’s processing)
•
Function block input parameter values that receive their values from a link cannot be changed (as the link will overwrite the value when the Drive
is running).
Configuration Mode (CONFIGURE ENABLE = ENABLED)
•
A link’s destination tag must be set to an input parameter (only one link per input parameter).
•
A link’s source tag may be set to any parameter. Both input and output parameters can be used as a source.
•
Disable a link/function block by setting the “destination” and “source” tag to zero.
•
To mark a link as a feedback link, set the source to the negative value of the tag to be connected. Feedback links are ignored when the function
block execution order is determined.
Execution Rules
The complete block diagram is executed every 5ms, with individual control blocks executing within 1ms. Just before a function block is executed, all
the links that have that block as their destination are executed, thereby copying new values in to the block’s parameter inputs. The input parameters are
then processed to produce a new set of output parameters. The execution order of the blocks is automatically arranged for minimal delay.
The output value transferred by a link on execution is clamped to be between the maximum and minimum value for its destination input parameter.
Summary of Contents for 590+ series
Page 2: ......
Page 14: ...Cont 12...
Page 16: ...DC590 Series DC Digital Drive...
Page 20: ......
Page 32: ...2 12 Product Overview DC590 Series DC Digital Drive...
Page 34: ......
Page 130: ...3 96 Installing the Drive DC590 Series DC Digital Drive...
Page 132: ......
Page 164: ...4 32 Operating the Drive DC590 Series DC Digital Drive...
Page 166: ......
Page 174: ...5 8 Control Loops DC590 Series DC Digital Drive...
Page 176: ......
Page 202: ......
Page 222: ...7 20 Trips and Fault Finding DC590 Series DC Digital Drive...
Page 224: ......
Page 242: ......
Page 272: ...DC590 Series DC Digital Drive...
Page 288: ...B 16 Certification DC590 Series DC Digital Drive...
Page 290: ......
Page 342: ...C 52 Parameter Specification Tables DC590 Series DC Digital Drive...
Page 344: ......
Page 365: ...Programming D 21 DC590 Series DC Digital Drive Functional Description...
Page 494: ...D 150 Programming DC590 Series DC Digital Drive Programming Block Diagram Sheet 1...
Page 495: ...Programming D 151 DC590 Series DC Digital Drive Programming Block Diagram Sheet 2...
Page 496: ...D 152 Programming DC590 Series DC Digital Drive Programming Block Diagram Sheet 3...
Page 497: ...Programming D 153 DC590 Series DC Digital Drive Programming Block Diagram Sheet 4...
Page 502: ...D 158 Programming DC590 Series DC Digital Drive...
Page 504: ......
Page 506: ...E 2 Technical Specifications DC590 Series DC Digital Drive...
Page 507: ...Technical Specifications E 3 DC590 Series DC Digital Drive...