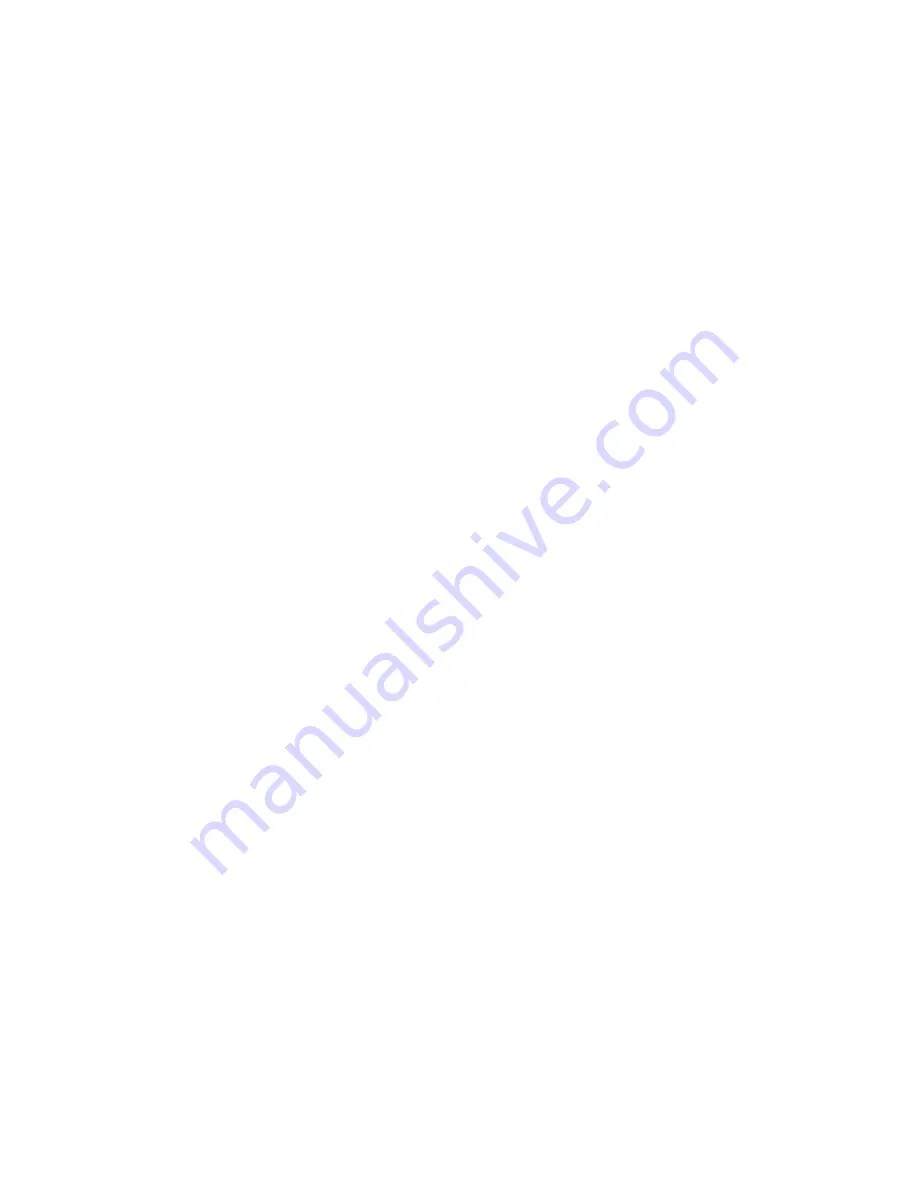
8-16
Routine Maintenance and Repair
DC590+ Series DC Digital Drive
3.
Remove the trigger board by releasing the four M6 Sems nuts fixing the PCB to the assembly. If you are working on a 590+ (4Q), remove the
dummy trigger board, or if working on a 591+ (2Q) remove the thyristor suppression board. Remove the air duct from the top of the phase
assembly to gain access to the DC interconnection plates.
Do not remove the trigger board support spacers.
4.
Remove the DC interconnection plates between the phase assembly and its adjacent assemblies, either output terminals or phase assemblies.
5.
If changing an upper phase assembly on a 590+ or 591+ remove the top baffle. This is achieved by pushing out the two end flaps of the plenum
chamber and unclipping the top baffle from the top cover baffle stops and the top of the phase assemblies. Remove the vertical baffles between
phase assemblies.
6.
If changing a lower phase assembly on a 590+, remove the lower air duct.
7.
Remove the complete phase assembly by removing the four M6 Sems nuts at the top and bottom of the phase assembly.
NOTE
On the 591+ 2Q, the left hand screw retains the phase coding connection which should be pushed to one side before lifting the phase assembly.
Phase Assembly Fitting Procedure
1.
Position the repaired or spare phase assembly on to the back panel spacer. (Remember to re-connect the coding lead to the bottom of the phase
assembly when working on a 591+ 2Q).
Check for correct orientation of the assembly. Fix in position with 4 x M6 Sems nuts and tighten to the correct torque level.
Refit the interconnecting plate stacks between the phase assemblies. A stack of three plates are used on a 1200 Amp unit, four on a 1700 Amp unit,
five on a 2200 Amp unit and six on a 2700 Amp unit. On a 4Q unit the plates interconnect both the upper and lower thyristors and adjacent phase
assemblies. On the 2Q unit the plates interconnect adjacent phase assemblies. Tighten to the correct torque level.
NOTE
a) When fitting a spare phase assembly there may be some misalignment to the new phase where the interconnection plates do not fit easily.
In this case, loosen the trigger support spacers which will allow adjustment of the support bars. Fit the interconnecting plates and re-tighten
all units, including spacers.
b) When re-assembling the interconnection plates it is important that a good electrical contact is made between the plates and the
aluminium heatsink. Apply a layer of `zinc-loaded’ jointing compound between the interconnection plates and the heatsink.
2.
Refit the air duct on the phase assembly ensuring that the duct fits inside the side ducting of the phase assembly.
3.
Refit the trigger board (thyristor suppression board or dummy board as appropriate) and secure with the M6 Sems nuts.
4.
Reconnect the gate leads, thermostat and suppression lead as necessary. The gate leads cannot be fitted incorrectly as they are polarised by the
plugs.
5.
Re-fit the top baffle (either plenum cover or lower 4Q air duct) and vertical baffles.
6.
Replace the fuse.
7.
Re-close the swing-frame.
8.
Replace the trigger board connectors.
Summary of Contents for 590+ series
Page 2: ......
Page 14: ...Cont 12...
Page 16: ...DC590 Series DC Digital Drive...
Page 20: ......
Page 32: ...2 12 Product Overview DC590 Series DC Digital Drive...
Page 34: ......
Page 130: ...3 96 Installing the Drive DC590 Series DC Digital Drive...
Page 132: ......
Page 164: ...4 32 Operating the Drive DC590 Series DC Digital Drive...
Page 166: ......
Page 174: ...5 8 Control Loops DC590 Series DC Digital Drive...
Page 176: ......
Page 202: ......
Page 222: ...7 20 Trips and Fault Finding DC590 Series DC Digital Drive...
Page 224: ......
Page 242: ......
Page 272: ...DC590 Series DC Digital Drive...
Page 288: ...B 16 Certification DC590 Series DC Digital Drive...
Page 290: ......
Page 342: ...C 52 Parameter Specification Tables DC590 Series DC Digital Drive...
Page 344: ......
Page 365: ...Programming D 21 DC590 Series DC Digital Drive Functional Description...
Page 494: ...D 150 Programming DC590 Series DC Digital Drive Programming Block Diagram Sheet 1...
Page 495: ...Programming D 151 DC590 Series DC Digital Drive Programming Block Diagram Sheet 2...
Page 496: ...D 152 Programming DC590 Series DC Digital Drive Programming Block Diagram Sheet 3...
Page 497: ...Programming D 153 DC590 Series DC Digital Drive Programming Block Diagram Sheet 4...
Page 502: ...D 158 Programming DC590 Series DC Digital Drive...
Page 504: ......
Page 506: ...E 2 Technical Specifications DC590 Series DC Digital Drive...
Page 507: ...Technical Specifications E 3 DC590 Series DC Digital Drive...