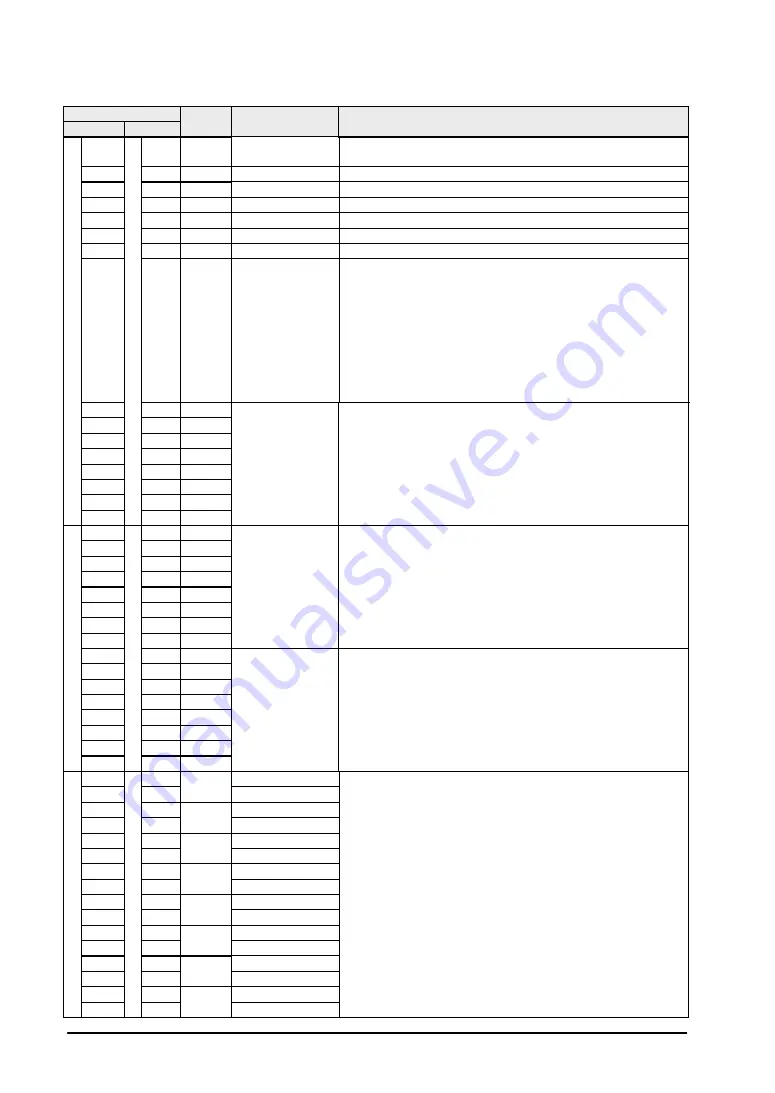
6-6
Contact allocation Target
axis
Name
Descriptions
FP
Σ
FP2
WY
10
Y100
W
Y8
Y80 All axes System stop
Contact for requesting the system stop. When it turns on, all
axes will stop at the deceleration time 0.
Y101
Y81 -
-
-
Y102
Y82 -
-
-
Y103
Y83 -
-
-
Y104
Y84 -
-
-
Y105
Y85 -
-
-
Y106
Y86 -
-
-
Y107
Y87 All axes Recalculation
request
Turn on this signal when each positioning data (standard area) in
the shared memory was changed.
The positioning data after the table number starting the
recalculation specified in the shared memory can be restructured
and will be executable by turning on this signal.
When restructuring of the positioning data completes, the
recalculation done contact (X
_
7) will turn on.
Note) It is used only when the positioning data has been
rewritten by ladder programs.
Y108
Y88 1 axis
Servo ON request
Requests the servo lock for the corresponding AMP.
The servo lock is executed by the ON edge of this contact.
The servo cannot be free automatically even in the program
mode.
To make the servo free, turn on the servo OFF request contact.
(The operation is the edge type.)
Y109
Y89 2 axis
Y10A
Y8A 3 axis
Y10B
Y8B 4 axis
Y10C
Y8C 5 axis
Y10D
Y8D 6 axis
Y10E
Y8E 7 axis
Y10F
Y8F 8 axis
WY
11
Y110
W
Y
9
Y90 1 axis
Positioning start-up
Requests the positioning control for the corresponding AMP.
The starting table is specified in the area for specifying the
position control starting table number in the shared memory.
(The operation is the edge type.)
If this contact turns on during the Tool operation by Configurator
PM, a warning will be output.
Y111
Y91 2 axis
Y112
Y92 3 axis
Y113
Y93 4 axis
Y114
Y94 5 axis
Y115
Y95 6 axis
Y116
Y96 7 axis
Y117
Y97 8 axis
Y118
Y98 1 axis
Home return start-
up
Requests the home return for the corresponding AMP.
The settings for the direction or pattern of the home return are
specified by Configurator PM or the home return operation
setting area in the shared memory.
(The operation is the edge type.)
If this contact turns on during the Tool operation by Configurator
PM, a warning will be output.
Y119
Y99 2 axis
Y11A
Y9A 3 axis
Y11B
Y9B 4 axis
Y11C
Y9C 5 axis
Y11D
Y9D 6 axis
Y11E
Y9E 7 axis
Y11F
Y9F 8 axis
WY
12
Y120
WY
10
Y100 1 axis JOG forward
Requests the JOG operation for the corresponding AMP.
The settings for acceleration time, etc are specified by
Configurator PM or the JOG operation settings in the shared
memory.
(The operation is the level type.)
If this contact turns on during the Tool operation by Configurator
PM, a warning will be output.
Y121
Y101
JOG reverse
Y122
Y102 2 axis JOG forward
Y123
Y103
JOG reverse
Y124
Y104 3 axis JOG forward
Y125
Y105
JOG reverse
Y126
Y106 4 axis JOG forward
Y127
Y107
JOG reverse
Y128
Y108 5 axis JOG forward
Y129
Y109
JOG reverse
Y12A
Y10A 6 axis JOG forward
Y12B
Y10B
JOG reverse
Y12C
Y10C 7 axis JOG forward
Y12D
Y10D
JOG reverse
Y12E
Y10E 8 axis JOG forward
Y12F
Y10F
JOG reverse
Summary of Contents for FP2 Positioning Unit RTEX
Page 1: ......
Page 6: ...iv ...
Page 14: ...xii ...
Page 15: ...Chapter 1 Functions of Unit and Restrictions on Combination ...
Page 21: ...Chapter 2 Parts and Functions ...
Page 22: ...2 2 2 1 Parts and Functions FPΣ Positioning Unit RTEX FP2 Positioning Unit RTEX ...
Page 24: ...2 4 ...
Page 25: ...Chapter 3 Wiring ...
Page 31: ...Chapter 4 Power On Off and Items to Check ...
Page 36: ...4 6 ...
Page 37: ...Chapter 5 4BPreparation For Operation ...
Page 45: ...Chapter 6 5BI O Allocation ...
Page 53: ...Chapter 7 6BSetting Tool Configurator PM ...
Page 83: ...7 31 Setting Font Select Option Font in the menu bar The following dialog is shown ...
Page 102: ...7 50 ...
Page 103: ...Chapter 8 7BAutomatic Operation Position Control ...
Page 118: ...8 16 ...
Page 119: ...8 17 When the X axis and Y axis is the moving axes each axis in the above diagram is replaced ...
Page 141: ...Chapter 9 8BManual Operation JOG Operation ...
Page 146: ...9 6 ...
Page 147: ...Chapter 10 9BManual Operation Home Return ...
Page 155: ...Chapter 11 10BManual Operation Pulser Operation ...
Page 159: ...Chapter 12 11BStop Functions ...
Page 162: ...12 4 ...
Page 163: ...Chapter 13 12BSupplementary Functions ...
Page 177: ...13 15 Sample program When reading AMP parameter No 1 1 of axis 1 with A6N or A5N ...
Page 179: ...13 17 Sample program When writing AMP parameter No 1 1 of axis 1 with A6N or A5N ...
Page 183: ...Chapter 14 Precautions During Programming ...
Page 187: ...Chapter 15 Errors and Warnings ...
Page 212: ...15 26 ...
Page 213: ...Chapter 16 Troubleshooting ...
Page 214: ...16 2 16 1 Cannot Communication With AMP ...
Page 215: ...Chapter 17 Specifications ...
Page 275: ...Chapter 18 Dimensions ...
Page 276: ...18 2 18 1 FPSigma Positioning Unit RTEX ...
Page 277: ...18 3 18 2 FP2 Positioning Unit RTEX ...
Page 278: ...18 4 ...
Page 279: ...Chapter 19 Sample Programs ...
Page 283: ...19 5 ...
Page 286: ...19 8 ...
Page 288: ......