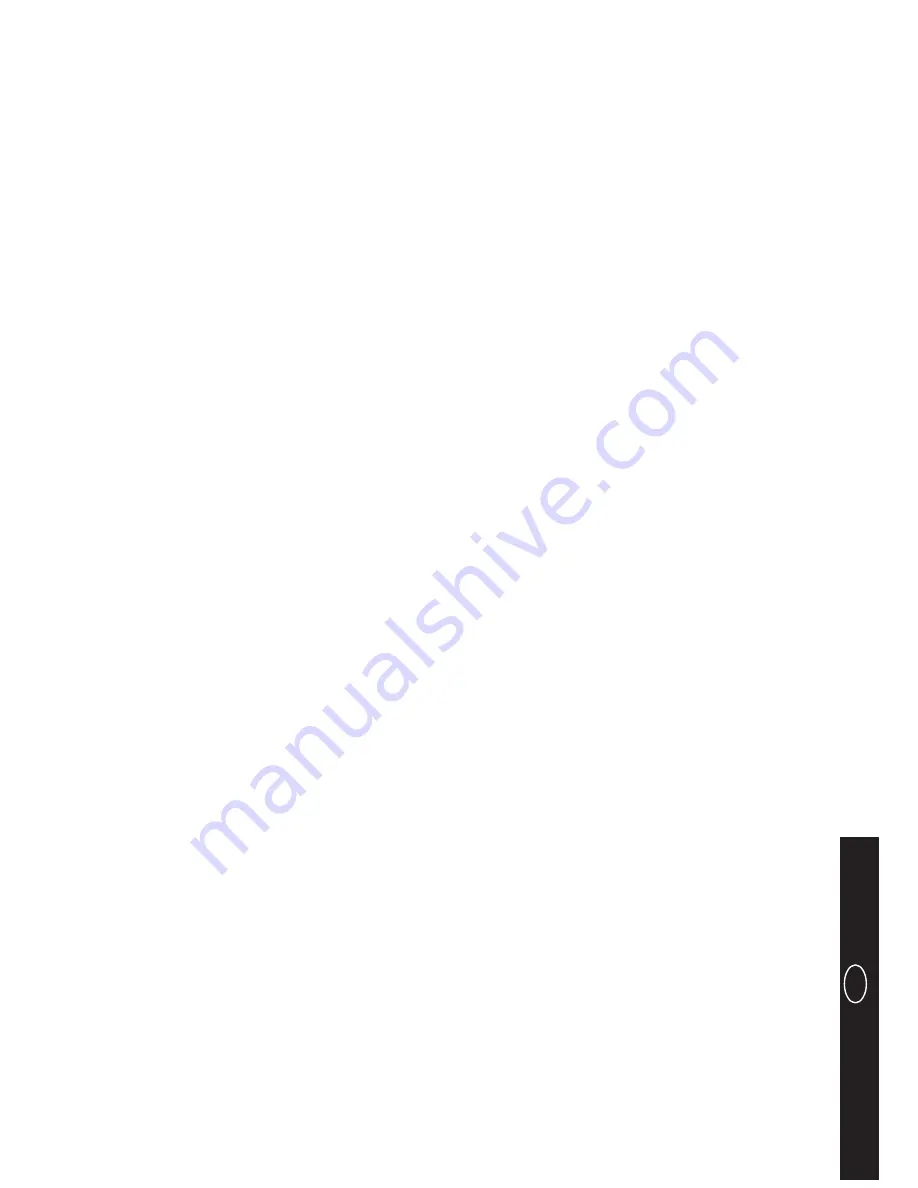
GB
17
Insulation
Stub pipe
Bend
H = 2D
Smoke outlet adjustment butterfly valve
6 x 6 mm adjusting rod to cut to the right side
Adjusting handle
CLOSED
OPEN
2.1.5
COUNTER HOOD
We suggest using plasterboard to make the counter hood, because it is
easy to work with and, most important of all, it will not overload the
underlying structure of the fireplace with hollow tiles: a marble
mantelpiece and timber beams CANNOT act at the bearing structure.
Before the counter hood can be made, the control unit must be installed
and the wiring done (see diagrams on page 10).
2.1.6
SMOKE TEST
•
Before final assembly however it would be advisable to carry out
a smoke test by which we mean testing the fireplace with the
door open.
•
If everything works properly, the counter hood can be mounted
permanently;
•
Vice versa, if malfunctions are found, make certain that all the
technical indications have been complied with.
2.2
PLUMBING
Since this boiler works with solid fuel, TERMOPALEX must be installed
following specific plumbing diagrams. The law (M.D. 1/12/1975)
establishes that an EXPANSION TANK be used of the type OPEN to the
atmosphere, that a safety valve be installed, supplied with the fireplace,
within 50 cm from the boiler’s delivery pipe, as well as all the other
sensors that are used to make the system safe and efficient.
Termopalex BI 300 is designed with a storage tank boiler for the
production of hot sanitary water. It is mounted vertically on the right of
the fireplace but there are supports and fittings for mounting it on the
left.
2.2.1
TYPICAL PLUMBING DIAGRAMS
Different system diagrams can be used with the heating fireplace
because it is so flexible. For this reason please refer to the heating/
plumbing system on pages 14 to 17 where you will find different
examples of fireplace connection diagrams.
The fireplace’s delivery pipe must first be connected to the boiler and
from the boiler to the heating system.
TERMOPALEX BS 300 (without boiler) must be connected to all the
sensors and safety devices established by the MD 1/12/1975, except
of course those relative to the boiler.
NB: Before you start mounting the cladding the boiler and relative
equipment must be TESTED, keeping in mind that the test leak pressure
must not exceed the boiler’s maximum working pressure which is 3
bar.
Figures 11-13 give a few FIREPLACE – BOILER – SYSTEM connection
diagrams.
We remind you that installation, plumbing, adjustment and start-up of
the system are to be performed only by skilled personnel in compliance
with the rules in this instruction manual and all the regulations in force.
1/2M sanitary water outlet
safety pipe;
Heating delivery pipe
Safety valve
Water gauge fitting
Control panel probe holder pit (optional)
Fitting for valve
heat exhaust
1/2 M sanitary water inlet
Temperature control pit
1¼ F fitting
Heating return pipe
boiler storage tank.
Connection with the boiler
Connection without the boiler
exclusively by qualified personnel in compliance with the indications
given in this handbook and with all the standards and laws in force.
For thermal dimensioning consider that the global power available is
about 21,900 kcal/h consequently for heatable surfaces measuring
about 100 ÷ 140 m2 (for buildings whose construction characteristics
conform to the laws regarding energy saving). There is also the
possibility of a connection for the production of hot sanitary water.
2.2.2
ACCESSORIES
TERMOPALEX comes with a few accessories to facilitate its installation
and also so that the plumber can do his job in compliance with current
standards.
a) Supplied with the fireplace
V.S. = Safety Valve DN ½” (Fig. 11 page 8)
These accessories are for installing on the heating fireplace’s
delivery pipe using a DN 1¼” ÷ 1½” size T. Everything must be positioned
so it can be inspected through the hatch which must be on the external
fireplace cladding. Discharge of the V.S. must be connected outdoors
with a pipe draining into the sewer.
The V.S., calibrated at 2.7 bar, must be installed even if the heating
fireplace is equipped with an open type expansion tank. In fact, its
function is to avoid the boiler body from exceeding the test pressure
should the fill-up pipe burst due to nighttimes freezing, or the safety
pipes for the expansion tanks if they are installed under the roof and
are not lagged and subject to temperatures below zero
b) On request
Control panel, (Fig. 14) this electrical equipment allows you to keep
the termopalex under control and comprises the following devices:
•
Pump start thermostat
•
Water gauge
•
Thermometer
•
Alarm bell.
You will find more information on the technical data sheet on page 18
Note: The control panel is an essential accessory for controlling
correct operation of the termopalex; the Customer is not bound to use
the control panel supplied by Palazzetti but he must see to installing and
using a similar one.
2.3
ELECTRICAL CONNECTIONS
2.3.1
INSTALLING THE OPTIONAL CONTROL PANEL
The electrical panel must be installed near the heat generator. The
probes of the operating, protection and control devices must be installed
directly on the generator or, at most, on the delivery pipe at a distance
of no more than 0.5 m from the generator and, in all cases, before any
cutoff mechanism.
2.3.2
INSERTING THE BULBS (Fig. 15)
a) Use a cross fitting (Q) DN 1¼”, as shown in the drawing, positioned
on the hot water outlet.
b) Insert the probe holder pit (P) and put the three bulbs in, i.e. the end
part of the shutdown and minimum pump start thermostat and
thermometer (see also Fig. 12).
c ) The water gauge connection must be screwed down on to the
relative check valve, to be put on the manifold. (I)
2.3.3
EXTERNAL WALL MOUNTING
d) Open the cover with the key.
e) Loosen the centre screw until the black base of the panel comes
away.
f )
Fix the base to the wall using the screws and Rawlplugs provided.
g) The electrical cables can go in from the bottom or from the back.
Break the diaphragms and then wire as shown on the wiring
diagram on the label. The wires of the control, operating and
protection devices must come out through one of the holes with
breakable diaphragm.
h) Before putting the panel back on the base make sure the wiring has
been done properly.
2.3.4
RECESSED MOUNTING (Fig.18)
i)
Make a counter wall A on the back of the hood at a depth of 80 mm
from the front.
j)
Follow the instructions given in points d) and e) .
k) Fix base B to counter wall A.
l)
Make a 140 x 140 mm hole on the front wall C on which to mount the
control panel.
m) Position the bulbs and electrical wires using the prepared holes
that simply need pushing through.
2.3.5
OPERATION (Fig.17)
Control devices:
•
Thermometer 7
•
Water gauge 6
Protection devices: acoustic alarm system
•
Buzzer 1
•
Shutdown thermostat 2
•
Luminous switch 3
The system triggers when the liquid temperature exceeds the limit
value established by Collection R and tells the operator to interrupt the
supply of fuel.
If the alarm sounds for a long time it can become a nuisance: it can be
turned off via the luminous switch. To restore the initial conditions,
after having rearmed the shutdown thermostat, reactivate the switch.
•
ATTENTION: during normal operation check that the switch is
illuminated (that there is electricity).
Operating device: circulating system
Adjustment thermostat 4
Operating pilot light 5
When the temperature of the fluid reaches the value set on the
thermostat, the circulator is activated and the pilot light turns on. The
moment the temperature of the fluid drops below the value considered,
the adjustment thermostat opens the electrical circuit: pilot light off and
the pump stopped.
2.3.6
WIRING DIAGRAM
Wire, following the indications on the connection terminal board (Fig.
18)
2.3.7
TECHNICAL DATA
Power: - 220 V ± 10%
Protection level: IP 40
Min. - max. ambiente temperature: +2 ÷ 50° C
Length of wires: 1.2 m
Thermometer: 0 ÷ 120° C
Summary of Contents for BI300
Page 12: ...12 SCHEMI IDRAULICI INSTALLATORE ...
Page 13: ...13 SCHEMI IDRAULICI INSTALLATORE ...
Page 14: ...14 SCHEMI IDRAULICI INSTALLATORE ...