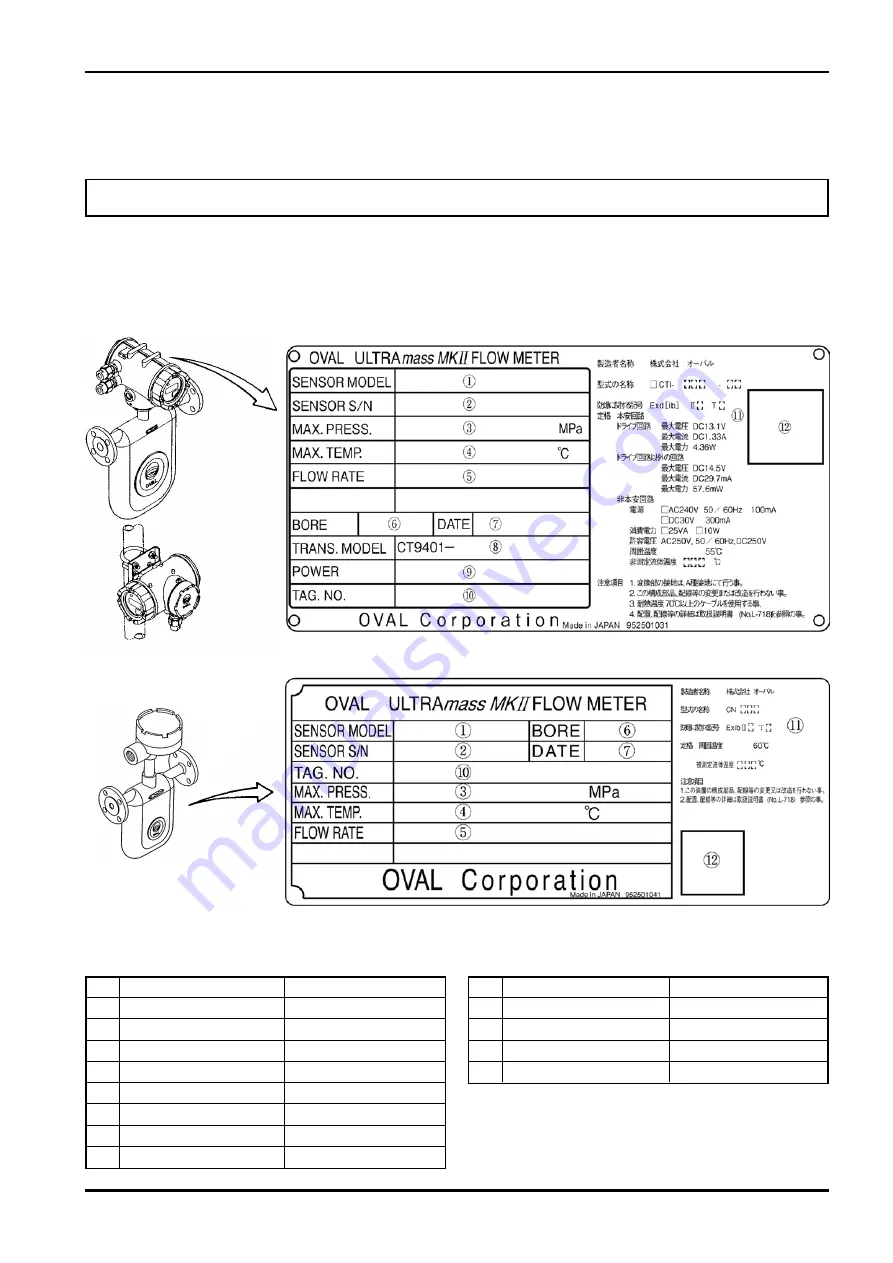
L-718-8-E
1. BEFORE YOU BEGIN
When you received, the sensor and transmitter,
both should be thoroughly inspected for any sign of
damage by rough handling during transit.
If you have something to inquire, contact the nearest OVAL sales/service office in your district.
1.1 Confirming the Tag Information
Product code and major ratings appear on the meter nameplate. Make sure that the product you
received complies with the specifications in your order.
Integrally-
mounted Type
Separately-mounted
Sensor Unit
No.
Item
Description
①
Model
②
Product No.
③
Max. Operating Press.
④
Max. Operating Temp.
⑤
Flow Range
⑥
Nominal Flange Dim.
⑦
Date of Manufacture
⑧
Model
No.
Item
Description
⑨
Power Source
⑩
Tag. No.
Only when so specified.
⑪
Ex. Specification
⑫
Certificate Nameplate
NOTE:
When you inquire, supply complete information
as to the product name, model number,
product number, ratings, etc.
Separately-mounted
Transmitter
Fig. 1.1 Tag Location
Items shown on the tag
Summary of Contents for Ultra mass MKII CN003
Page 66: ...L 718 8 E 66...
Page 67: ...L 718 8 E 67...
Page 68: ...L 718 8 E 68...
Page 69: ...L 718 8 E 69...
Page 70: ...L 718 8 E 70...
Page 71: ...L 718 8 E 71...