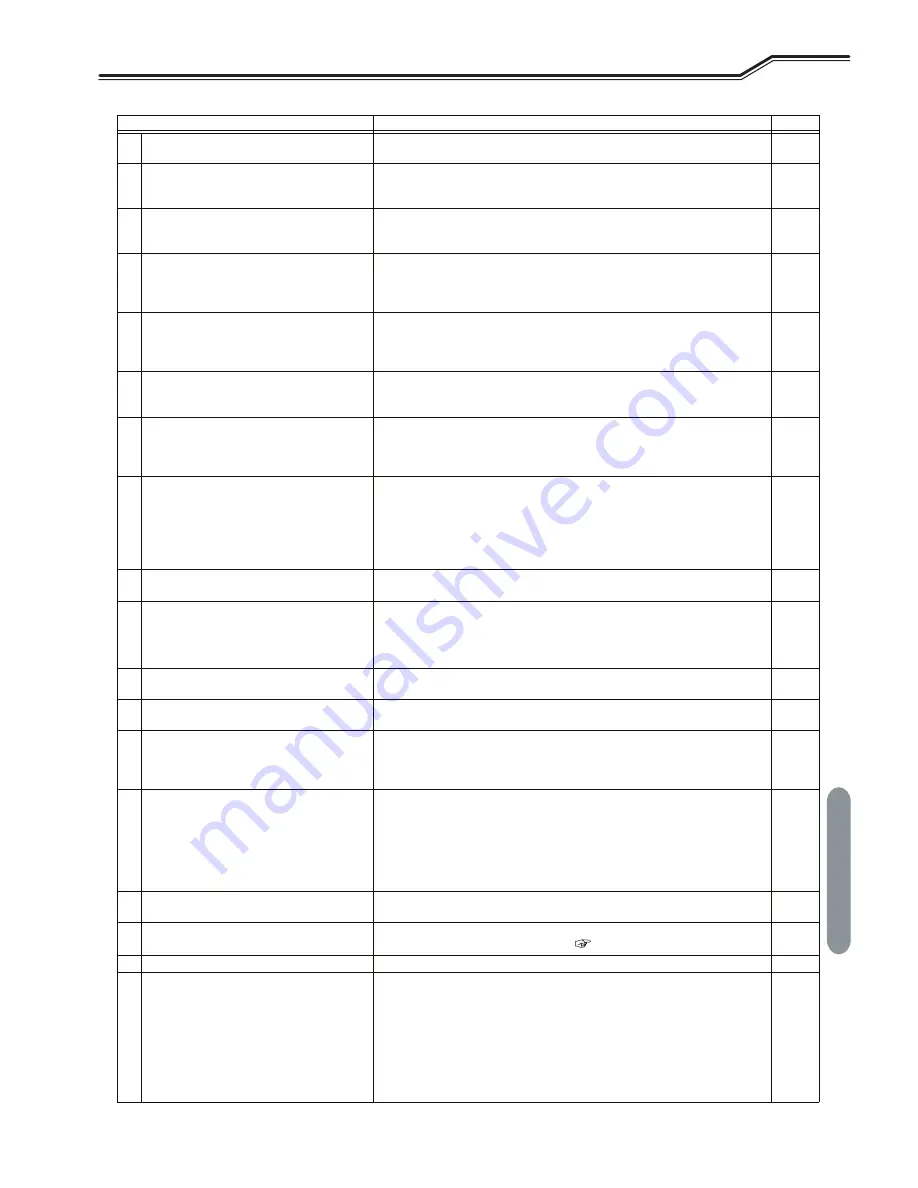
47
Chapter 5
W
elding Operation
C
HECK
BEFORE
W
ELDING
W
ELDING
O
PERATION
C
HAPTER
5
Check parameter
Countermeasures
Check
1
There should be no loose connections of the
cables.
Use a proper tool to ensure connection.
2
There should be no dirt such as oil or spatter
adhering on the connection terminals or
connection part of cables.
Wipe off dirt so that the metal face of connection terminal or connection part is fully
exposed. Using a metal brush is effective.
3
There should be no tightening together of the
voltage detection cable (base metal side) and
the cable at the base metal side.
Connect the voltage detection cable (base metal side) and the cable at the base
metal side separately to a different location.
Each cable should be connected to the position near to the workpiece to be welded.
4
The voltage detection cable should be
adequately wired.
The voltage detection cables at the base metal side and the torch side should be
wired along each other.
Keep the voltage detection cable (base metal side) at least 3.9" (10 cm) away from
the cable at the base metal side.
5
The voltage detection cable should not be
damaged.
If any damage is suspected, use a tester to measure the resistance between the
voltage detection cables.
When the resistance is high, replace the voltage detection cable with a new one.
(Reference value: 15.5 m
Ƙ
/m)
6
The contact part of jig and welding work piece
should not be painted.
Painted contact part could cause increased contact resistance, resulting in
decrease in arc voltage. Polish the painted contact part using a grinder to expose
the metal face.
7
The contact part of jig and welding work piece
should be free from unevenness due to
influence of burn through, spatter, or aging
deterioration.
Polish the surface of the jig using a grinder so that the welding workpiece and the
jig can fully contact each other.
8
The shield gas should be adequate.
The mixing ratio of mixed gas should be
adequate.
For shield gas, follow the mixing ratio as follows:
CO
2
gas
:
Carbon dioxide (CO
2
) 100 %
MAG gas
:
Argon (Ar) 80 % + Carbon dioxide (CO
2
) 20 %
MIG gas (Stainless)
:
Argon (Ar) 98 % + Oxygen (O
2
) 2 %
MIG gas (aluminum)
:
Argon (Ar) 100 %
9
The shield gas should be correctly mixed.
Use a mixer. If welding is unstable, use pre-mix gas to check if the welding condition
is improved. High CO
2
concentration could increase spatter generation.
10 The flow rate of shield gas should be adequate.
Ensure the adequate shield gas flow rate as follows:
CO
2
/MAG gas
MIG gas
TIG welding
:
21 to 53 CFH (10 to 25 L/min)
:
32 to 53 CFH (15 to 25 L/min)
:
11 to 32 CFH (5 to 15 L/min)
11
When the shield gas is mixed, each gas
pressure should be the same.
Set pressures of the respective gas to the same level.
12
Oil or other dirt should not be adhered on the
welding wire.
Consider a measure to wipe off the dirt and to perform degreasing.
13
In the CO
2
- and MAG welding, the particle
diameter of wire tip at the welding completion
should not excessively be large or small.
Adjust anti-stick voltage so that the wire tip particle size becomes 1.2 to 1.5 times
of the wire diameter. If the particle size is smaller than the above, set the anti-stick
voltage to a higher value, whereas if the particle size is larger than the above, set
the anti-stick voltage to a lower value.
14
At start point of welding, the tip of welding wire
and the welding workpiece should not be
contacted.
(When using a robot, operate several times with
"welding OFF" and confirm that the welding wire
and the welding workpiece do not contact each
other.)
If the wire tip contacts with the welding workpiece, set anti-stick voltage to a higher
value to increase meltage of the welding wire at the end of welding.
If anti-stick voltage is set to a value higher than the appropriate range, the wire tip
particle size becomes excessively large, resulting in poor start performance of the
next welding.
15 The tip of the welding torch should not be worn.
Visually check the hole diameter of the tip. If it is 1.2 times or larger than the hole
diameter of a new tip, or when the tip is discolored, replace it with a new one.
16
In wire feeding, pressure roll should not be idled
and the wire reel should rotate smoothly.
Adjust the pressure level of wire feeder. If it is not improved, check for other factor
that generates overload on wire feeding. (
See parameter 12, 17, 18)
17 The groove of feed roll should not be dirty.
Clean the dirty groove with a wiry tool.
18
There should be no large feeding resistance of
wire.
(With the pressurized holder of the wire feeder
held up, hold the tip of welding wire with a plier,
and try pulling it out; if smoothly pulled out, it is
adequate.)
Ensure that the torch cable has no bending at a sharp angle.
If the liner is clogged with dirt or when inched wire has flaw, replace the liner with
a new one.
(In replacing the liner, follow the precautions on the attached manual of welding
torch for appropriate handling.)
In cutting the liner, take care for the followings:
If the liner is too long: feeding resistance increases, resulting in shorter life of wire
feeder.
If the liner is too short: feeding failure occurs.
Summary of Contents for Welbee M350 II
Page 1: ...Welbee M350 II M500 II OWNER S MANUAL July 2021 Manual No P30355 1 DAIHEN Corporation...
Page 140: ...REFERENCE DRAWING REFERENCE MATERIALS CHAPTER 10 138...
Page 141: ...139 Chapter 10 Reference Materials REFERENCE DRAWING REFERENCE MATERIALS CHAPTER 10 WB M502...
Page 142: ...REFERENCE DRAWING REFERENCE MATERIALS CHAPTER 10 140...