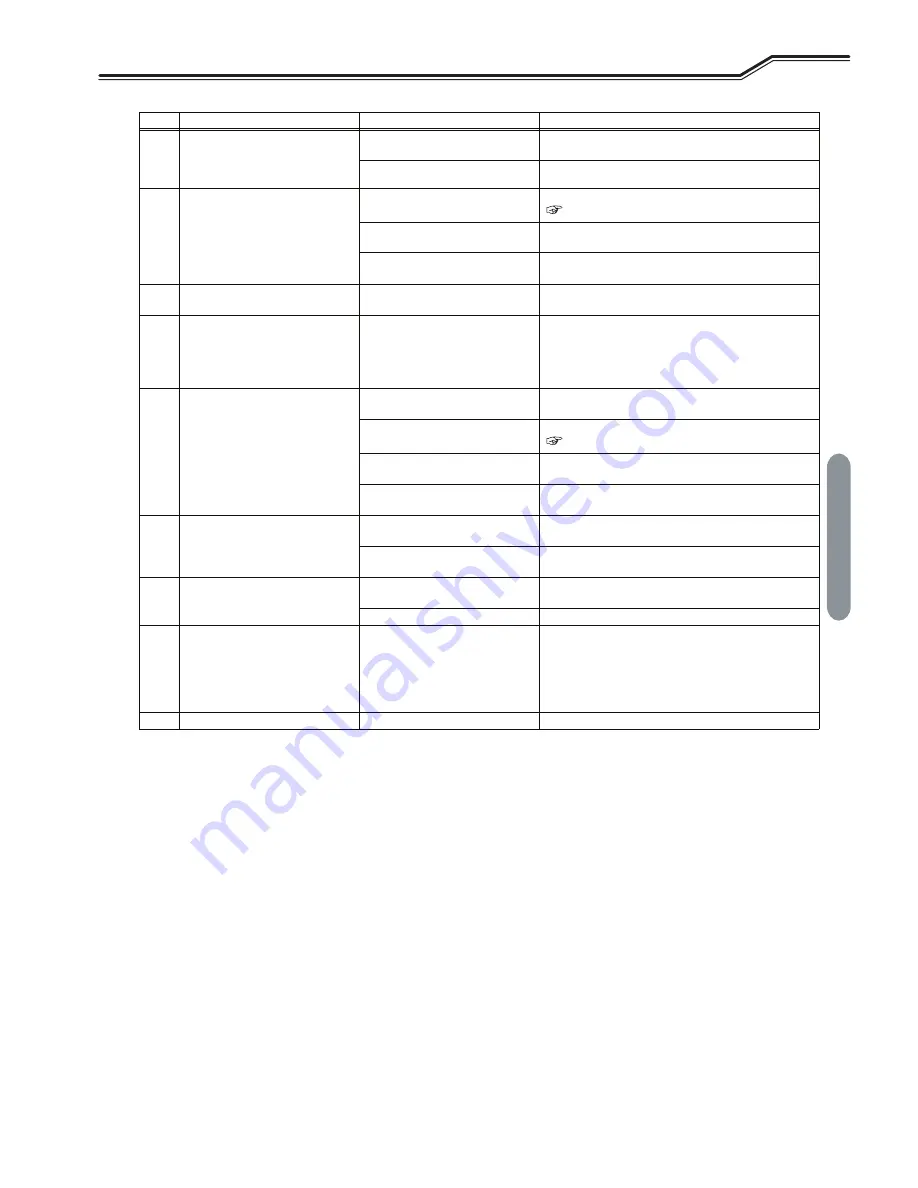
133
Chapter 9
T
roubleshooting
T
ROUBLESHOOTING
T
ROUBLESHOOTING
C
HAPTER
9
7
Arc does not generate even when
the setting of welding conditions is
correct.
(w/o no-load voltage)
Connection of the torch cable is
loose.
Securely connect the torch cable.
The torch switch is broken.
Check that the torch switch works normally.
8
Setting of current/voltage is not
possible.
The automatic machine mode is
selected.
Check that the setting of internal functions F4 is correct.
(
6.7.2.3
-
F4: Auto/Semi-auto mode)
An analog remote control (optional)
is connected.
When an analog remote control (optional) is connected,
the setting of the remote control has priority.
The encoder is broken.
The printed circuit board PCB2 (P30304R00) needs to be
replaced. Contact your dealer.
9
Operation of the CRATER-FILL menu
is not possible.
The internal function F4, F48 or F51
is set to "ON".
Turn the settings to "OFF".
10
The welding conditions cannot be
set with the operation panel.
The welding mode does not change
even when switched with the
operation panel.
The erroneous prevention function
to prevent malfunction of the
operation panel is enabled.
(Erroneous operation prevention
function)
Release the KEY LOCK to disable the erroneous operation
prevention function the operation panel.
11
Arc is unstable.
The setting of welding mode is not
correct.
Check the settings of wire diameter, wire materials and
shield gas.
The wire is defective or there is a
failure in wire feeding.
Check that there is no problem in the wire or wire feeder.
(
5.2
-
Check before Welding)
Connection of the voltage detection
cable is not correct.
Check that connection of the voltage detection cable is
correct.
There is noise in the voltage
detection cable.
Adjust the arc characteristics to the plus side.
12
Wire is not fed (no error code is
displayed).
The pressure roll of wire feeder
came off.
Set correctly the pressure roll of wire feeder. (For setting,
see the instruction manual of the wire feeder.)
There is an abnormality in cables of
the wire feeder.
Check that there is no abnormality in cables of the wire
feeder.
13
There are blowholes.
There is a problem in the shield gas.
Check that there is no abnormality in the gas cylinder or
gas hose.
The tip of the welding torch wore out. Replace the tip.
14
Continuous output of the WCR signal
is shown on the monitor of the robot.
(The WCR signal is used for
communicating with the robot to
check the presence of the welding
current.)
The WCR relay of welding power
source is broken.
The WCR relay on the printed circuit board PCB1
(P30099P00) needs to be replaced.
Contact your dealer.
15
The password is lost.
-
Contact your dealer.
No.
Problem
Possible cause
Corrective action
Summary of Contents for Welbee M350 II
Page 1: ...Welbee M350 II M500 II OWNER S MANUAL July 2021 Manual No P30355 1 DAIHEN Corporation...
Page 140: ...REFERENCE DRAWING REFERENCE MATERIALS CHAPTER 10 138...
Page 141: ...139 Chapter 10 Reference Materials REFERENCE DRAWING REFERENCE MATERIALS CHAPTER 10 WB M502...
Page 142: ...REFERENCE DRAWING REFERENCE MATERIALS CHAPTER 10 140...