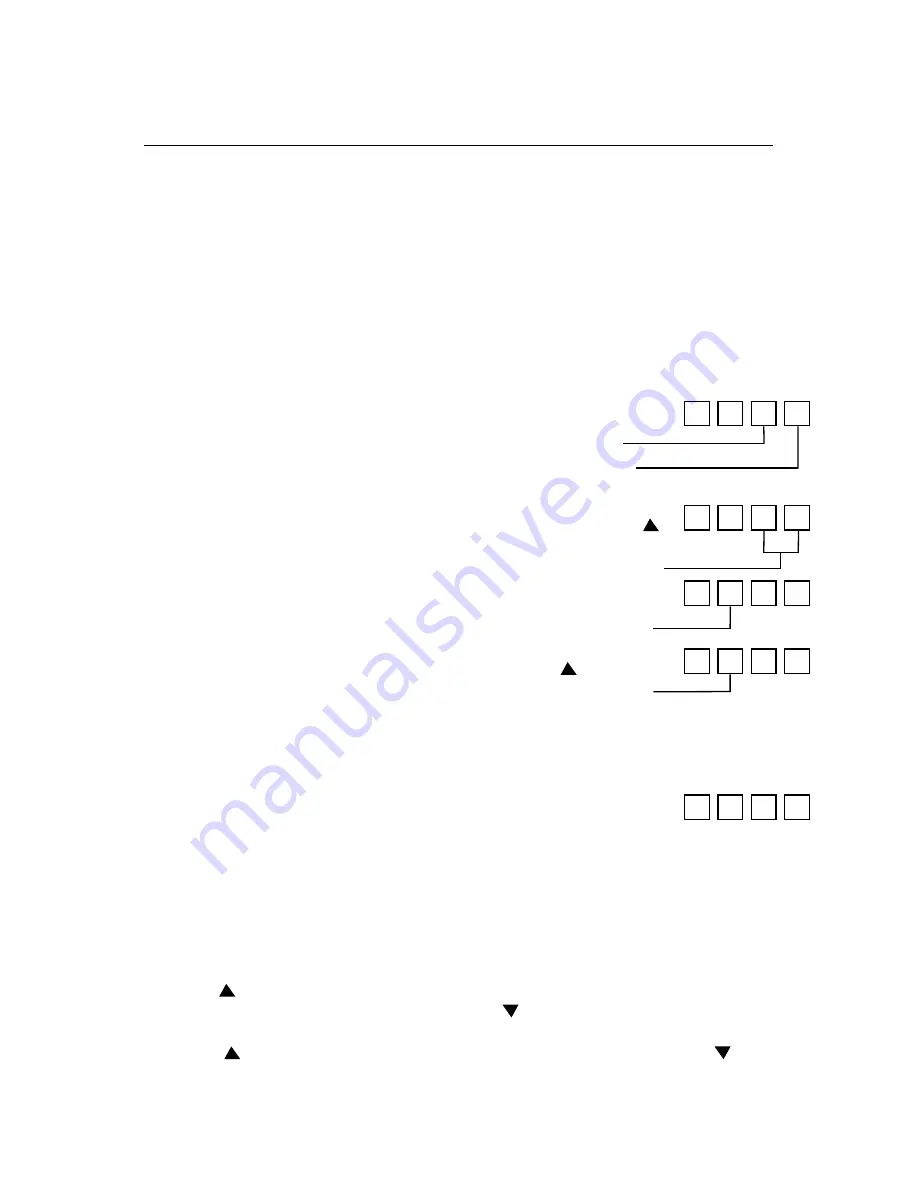
19
Ensure that the jumper behind
the lower front bezel is in the
Parameter Setting Position
(refer to Section 3.13). Note
Functions .1, .2, .3 are not
protected by the Parameter
Lock Jumper.
To convert the main display
from a temperature read-out
to the Function/Option Mode:
To change from Function .0 to
Function .16 (for example)
†
:
To change flashing Function
digit to Option digit:
To change from Option 0 to
Option 2 (for example)
††
:
To go to another Function:
When finished selecting the
Functions and Options (exiting
Program Mode), the
process temperature is
displayed. Control begins with
the new instructions now
entered into memory.
3.5.1.1 Example of Programming Functions. 0, .1,.2,.3,-.23
STEP
ACTION
DISPLAY
1
2
3
4
5
6
7
The following steps apply only to Functions .0,-.23. Section 3.6
covers more examples.
Press P
Option 0
Function .0
(flashing)
Press and Hold
until you see 0.16
Function (flashing)
Press
★
Option (flashing)
Press 2
times
Option (flashing)
Press
★
and
repeat steps 3-5 as
necessary
Press P
†
If using
button, the Function number changes in the following sequence:
":0, .1, .2,.... .25” and back to “.0”. If using
button, and the display shows
“.0" in Function place, the display changes to “.13” and then “.12, .11, ..., .0".
††
If using
button, the Option number goes as high as 100. If using
button,
the Option number goes down to 0.
0.
0
0.
1
6
0.
1
6
2.
1
6
T
E
M
P
Summary of Contents for C9000A SERIES
Page 6: ...This page is intentionally blank iv ...
Page 76: ...70 NOTES ...
Page 90: ...84 NOTES ...