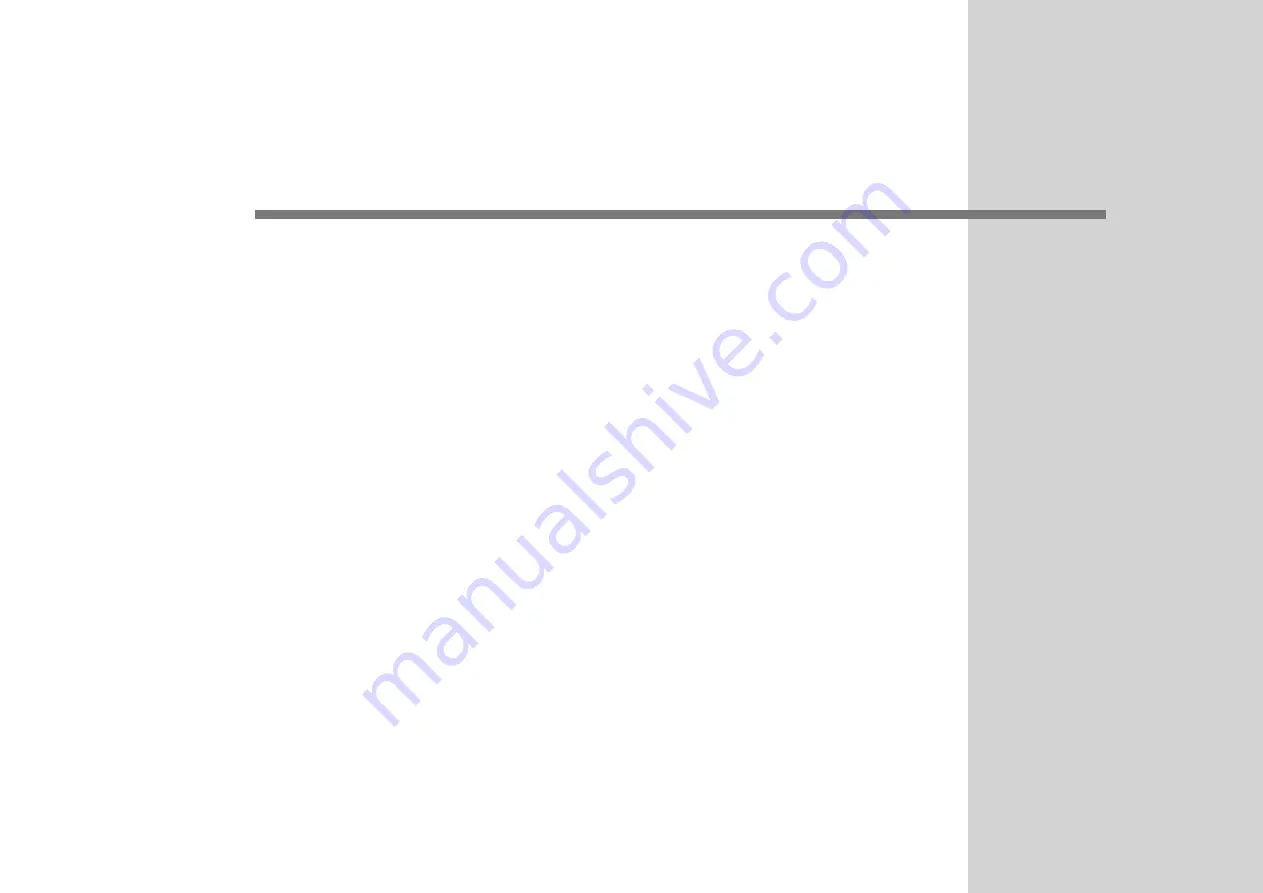
6.1 Connection diagram ..................................................................6-2
6.2 Board Layout .............................................................................6-3
6.3 Resistance value .....................................................................6-11
6.
CONNECTION DIAGRAM