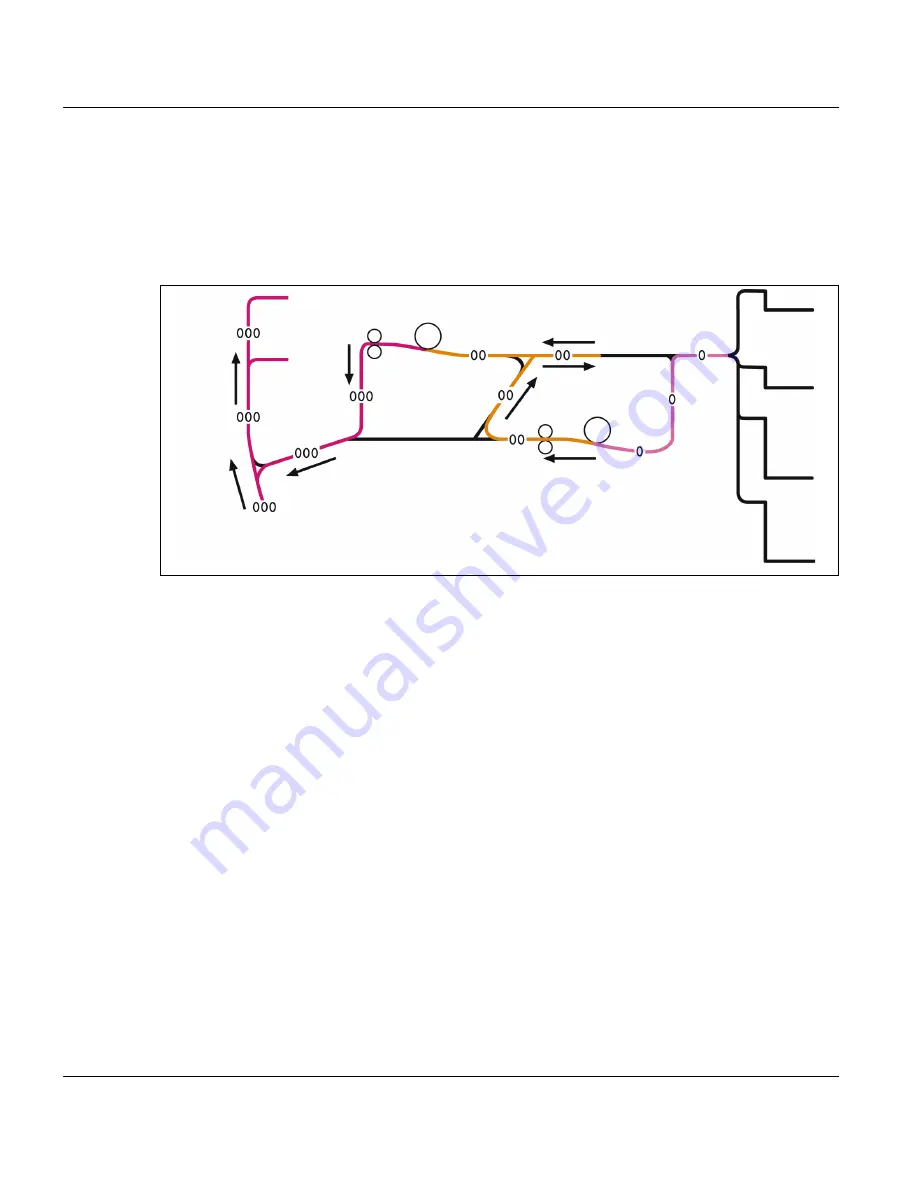
3.4.2 Duplex printing
40
A29246-X17-X-4-7680 / do301.fm
3.4.2 Duplex printing
In duplex printing (auto mode), the paper is printed on both sides. It is conveyed from the
input to the lower print unit and then up via turning bay 1. There it runs through the upper
print unit and is transported to the paper output via turning bay 2.
-o-: Path taken by paper before printing
-oo-: Path taken by paper printed on one side after printing
-ooo-: Path taken by paper printed on both sides after printing
Turning bay 1::Duplex turning bay
Turning bay 2: Face down turning bay
Turning bay 1:
Turning bay 2:
Summary of Contents for VarioPrint 5000
Page 1: ...Océ Océ Operating Manual Océ VarioPrint 5000 ...
Page 4: ......
Page 24: ...1 8 Statutory requirements 14 A29246 X17 X 4 7680 all103 fm ...
Page 56: ...3 5 Interposer 46 A29246 X17 X 4 7680 do301 fm ...
Page 74: ...4 2 3 Menu display 64 A29246 X17 X 4 7680 do401 fm ...
Page 82: ...4 3 2 3 Change language 72 A29246 X17 X 4 7680 all_allg3 fm ...
Page 168: ...5 9 6 Calculation and input of shrinkage compensation 158 A29246 X17 X 4 7680 do501 fm ...
Page 360: ......