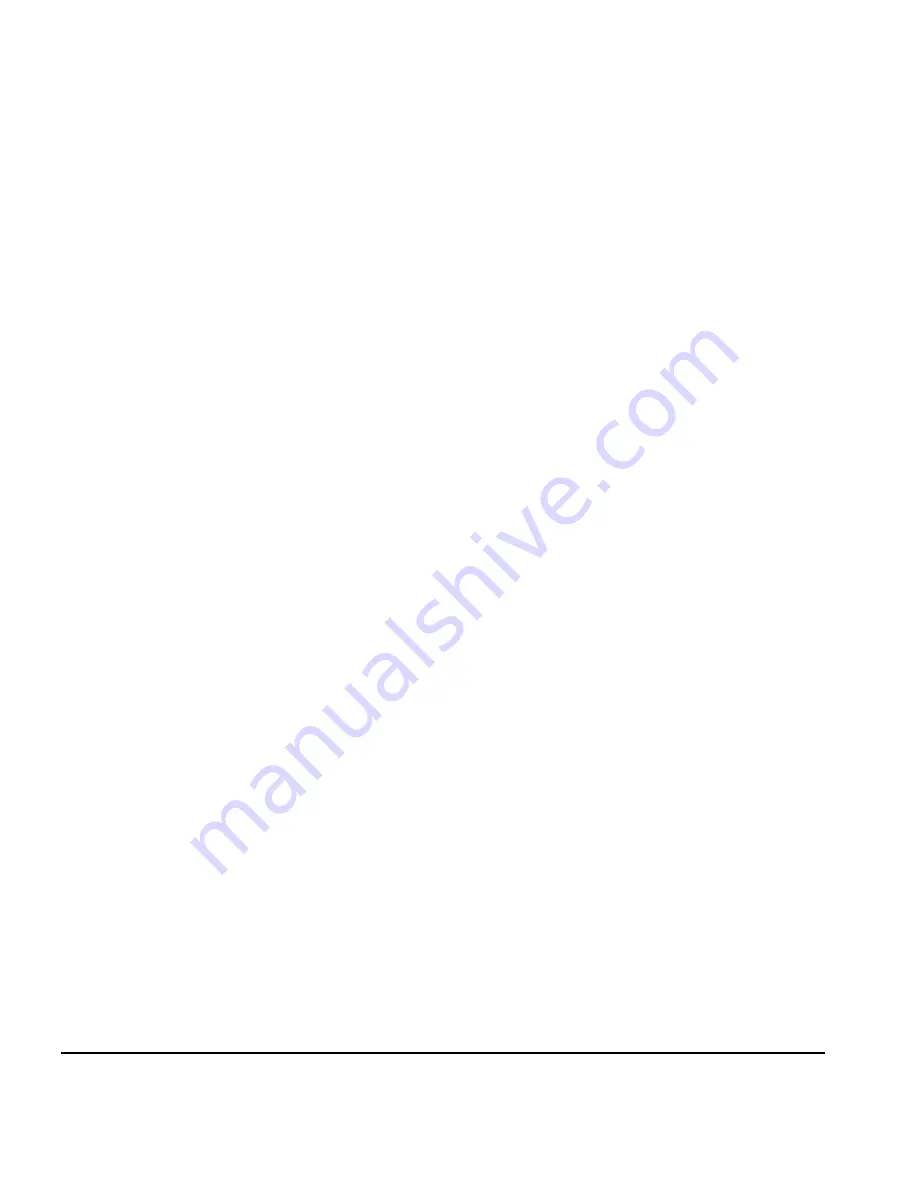
1-10
Safety Warnings
French
◆
L’imprimante doit etre operée avec utiliser tous les mésures
de sécurite. Quand vous utilisez l’imprimante en respecter
tous les instructions de fabricant , lunettes de protection et
vetements de protection n’est pas nécessaire. L’imprimeur
UV doit etre opéree comme écrit dans le mode d’emploi.
◆
Attention aux mains ! L‘mprimante est trop lourd (-) . Il
réquis au moins trois personnes (–) l’imprimante. Veuillez
ne pas excéder le poids maximum pour des tableaux input
et output, comme imprime sur la fiche.
◆
Lire et suivre tous les mésures de securite comme écrit dans
le ‘Material Safety Data Sheet’ pour l’encre. Et poster le doc-
ument comme requis par loi local. Eviter contact avec les
yeux et mains. Ventilation adequat est requis. Verifier si pro-
tection respiratoire est necessaire. Les componants ont pas
établie les standards OSHA, NIOSH ou ACGIH .
◆
Pour etre sur qu il n’ya pas encore d’électricite dans l’impri-
mante déconnecter tous les connections électronique. Pour
deconnecter l’imprimante complet, veuillez déconnecter
l’imprimante completement.
◆
L’émission d’UV peut donner une reaction avec oxygene et
producer ozone. L’imprimeur doit etre opree dans un endroit
avec beacuoup de ventilation enfin d’eviter des effets mineur
comme fatiguance, mal a tete. Ventilation normal evite ca.
◆
L'électronique d'imprimeur contenu une batteriie lithium.
Quand on place le batterie ne pas correct il y a un risque
d'explosion. La batterie doit etre installé par un technicien
certifiee.
Summary of Contents for CS7075
Page 1: ...Oc CS7075 Oc CS7100 User Manual for Oc UV curable inkjet printers 0706341 Rev B...
Page 8: ...viii...
Page 25: ...Workflow Overview 1 13...
Page 28: ...1 16 Workflow Overview...
Page 38: ...1 26 Special Features...
Page 100: ...3 44 Media Wizard...
Page 107: ...Auto Calibrations 4 7 Fig 4 1 Auto calibration patterns and reports...
Page 128: ...4 28 Linearization...
Page 138: ...5 10 Recover Missing Ink Jets...
Page 176: ...B 16 Diagnostics...
Page 177: ...Index 1 Index...
Page 182: ...Index 6...