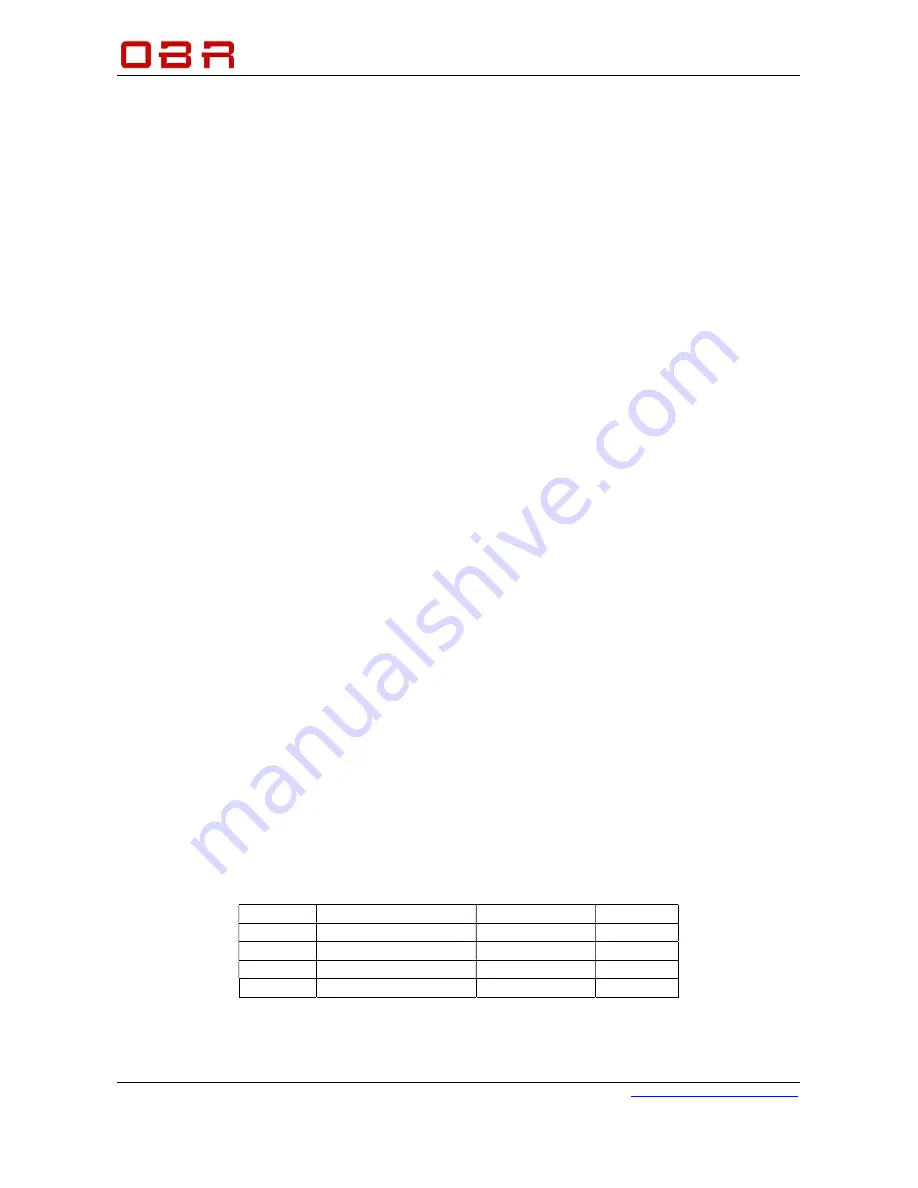
Control Systems
OBR Control Systems Inc
OBR Control Systems Inc
Telephone : +1 (248) 672-3339
32233 West 8 Mile Road
www.obrcontrolsystems.com
Livonia, Michigan 48152
USA
35 / 92
9 Outputs
PCM2 has 48 power channels with current measurement plus 4 tri-state outputs. Additional 3
VREF 5V sensor supplies plus a fault warning light are available, providing max 1A each.
All power outputs are designed for use in harsh environments and include self-recovery features.
Power outputs are designed to handle loads with high inrush current as well as motors and all
types of resistive and inductive loads.
All outputs are protected against reversed battery polarity and too high temperatures
The power channels are divided into groups:
Low power outputs (ON/OFF switches)
Low power wiper outputs (ON/OFF switches) – with recirculation diodes
Low power outputs with pulse width modulation (PWM)
High power outputs (ON/OFF switches)
High power outputs with pulse width modulation (PWM)
Very high power outputs (ON/OFF switches)
The tri-state analogue outputs cannot be used as power supplies; they can only be used as trigger
signals.
It is possible to connect two or more identical power outputs in parallel to increase the allowed
current draw.
Please note that any of the PWM channels may never be connected in parallel!
Click on the number button to the left of the output
name to open the visualisation display.
See section 8.
Please note that the current draw per channel is limited by the connector - not by the driver
stages. We have rated the individual channel’s current draw in relation to the connector
manufacturer’s specifications.
9.1 Tri-State
Tri-state outputs
cannot
be used as a power supplies. They are designed as logic switches and
are used only as trigger signals for analogue inputs on other modules, for example an ECU.
Maximum current draw must stay below 30 mA (milli ampere).
They are controlled by the event handling and the output signals can have these values:
0 Volt
2.5 Volts
5.0 Volts
9.1.1 Pin Configuration Tri-State Outputs
Tri-state Max current, milliA
Connector 3
Pin
1
30
AS2 20-39 SA
Y
2
30
AS2 20-39 SA
B
3
30
AS2 20-39 SA
Z
4
30
AS2 20-39 SA
C