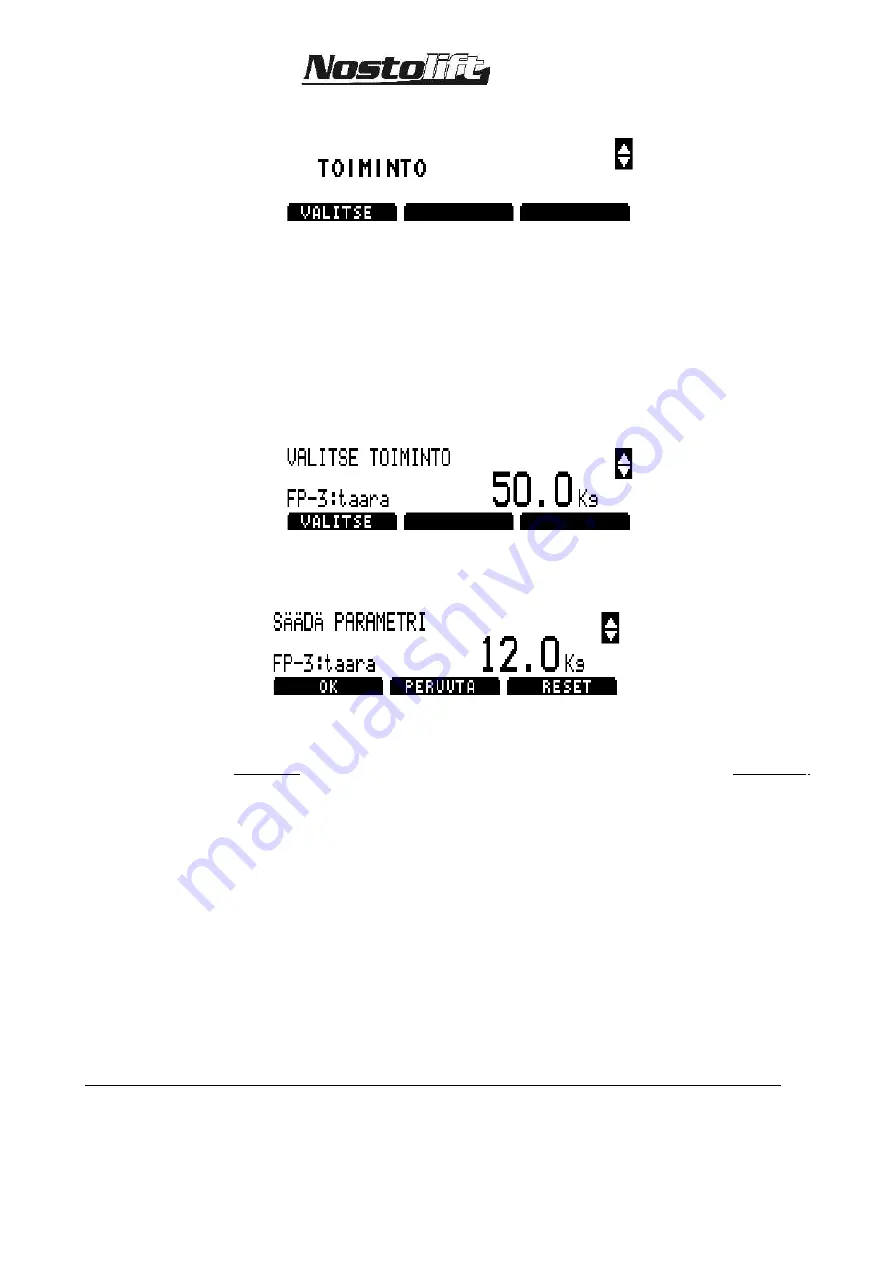
®
XS
240
SELF-PROPELLED TELESCOPIC PLATFORM
8.
Press
F1 SELECT
in the FUNCTIONS menu
9.
Select
FP-3: tare
using the arrow keys
10.
Press F1 SELECT
11.
12.
Adjust taring value using the arrow keys. If platform load control operates too
soon,
reduce
the value. If platform load control operates too late,
increase
the value
13.
Save the taring by pressing
F1 OK
You can cancel the change by pressing
F2 CANCEL
.
F3 RESET
restores the
manufacturer’s default setting (0.0 kg)
14.
Return to the main display by pressing
ESC
twice
15.
Switch off the current, then switch it back on
16.
Check proper operation according to the instructions. Readjust, if needed.
17.
Replace the display cover
The alarm limits have been set by the manufacturer and can not be adjusted separately.
Adjustment affects all values in the same proportion by increasing or decreasing the
weigher sensor reading.
33
Summary of Contents for XS240
Page 1: ...XS240 SELF PROPELLED TELESCOPIC PLATFORM OPERATION MAINTENANCE...
Page 6: ...XS 240 SELF PROPELLED TELESCOPIC PLATFORM 4 SPECIFICATION Figure 3 Specification 5...
Page 10: ...XS 240 SELF PROPELLED TELESCOPIC PLATFORM 5 1 NOSTOLIFT XS 240 BOOM GEOMETRY 9...